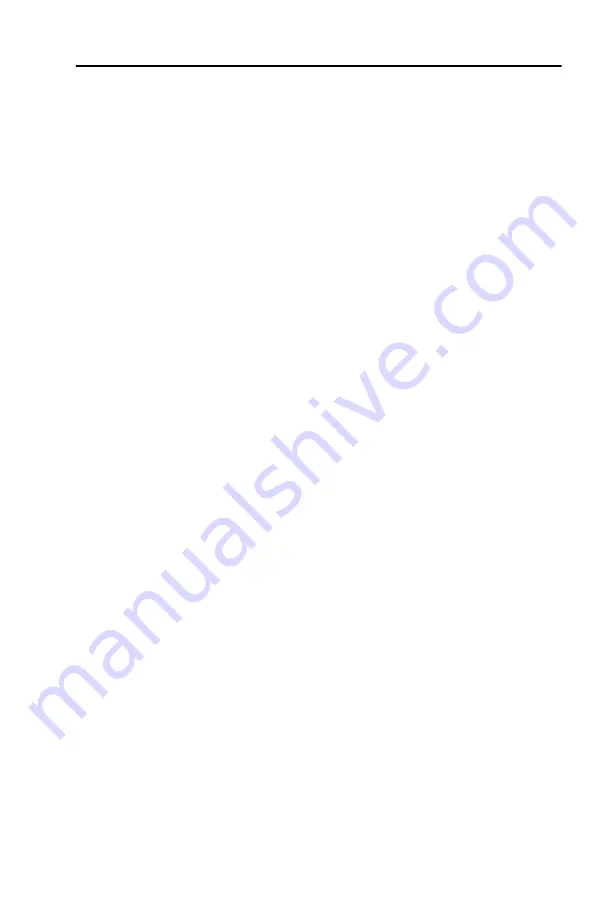
50950106/AP0313
117
Bucket Selection
To use the table, find the material to be loaded and its maximum density. Then
multiply the volumetric rating of the attachment by the material density to deter-
mine if the attachment can safely be used. See page 114 for a listing of attach-
ments and their ratings.
Where the material density is listed as a range (snow at 15-50 lbs./ft
3
, for
example), always use the maximum density (50 lbs./ft
3
in this example) for
making calculations. Also, see the following examples.
Example 1
: Clay (density of 80-100 lbs./cu. ft.) is to be hauled with a R220
model skid loader using a 70 in. dirt/construction bucket (SAE-rated heaped
capacity of 16 cu. ft.). With this bucket, the R220 has a rating of 2200 lbs. Multi-
plying the maximum density of the material by the bucket capacity (100 x 16)
yields a load that weighs 1600 lbs. This number is less than the machine rating
and thus indicates that the loader/bucket combination is safe to use in this appli-
cation.
Example 2
: Granite (density of 1488-1776 kg/m3) is to be hauled with a R260
model skid loader using a 1778 mm dirt/construction bucket (SAE-rated heaped
capacity of 0.46 m3). With this bucket, the R260 has a rating of 1179 kg. Multi-
plying the maximum density of the material by the bucket capacity (1776 x 0.46)
yields a load that weighs 817 kg. This number is less than the machine rating and
thus indicates that the loader/bucket combination is safe to use in this application.
Содержание R190
Страница 1: ...Skid Steer Loaders Operator s Manual Form No 50950106 AP0313 English R190 R220 R260 ...
Страница 4: ......
Страница 22: ...18 50950106 AP0313 Notes ...
Страница 36: ...32 50950106 AP0313 Information Center Electronic Display cont ...
Страница 37: ...50950106 AP0313 33 Information Center Electronic Display cont ...
Страница 50: ...46 50950106 AP0313 Notes ...
Страница 86: ...82 50950106 AP0313 Engine Diagnostic Chart ...
Страница 87: ...50950106 AP0313 83 Engine Diagnostic Chart cont ...
Страница 88: ...84 50950106 AP0313 Engine Diagnostic Chart cont ...
Страница 89: ...50950106 AP0313 85 Engine Diagnostic Chart cont ...
Страница 90: ...86 50950106 AP0313 Engine Diagnostic Chart cont ...
Страница 108: ...104 50950106 AP0313 Maintenance Log Date Hours Service Procedure ...
Страница 109: ...50950106 AP0313 105 Maintenance Log Date Hours Service Procedure ...
Страница 110: ...106 50950106 AP0313 Maintenance Log Date Hours Service Procedure ...
Страница 122: ...118 50950106 AP0313 Notes ...