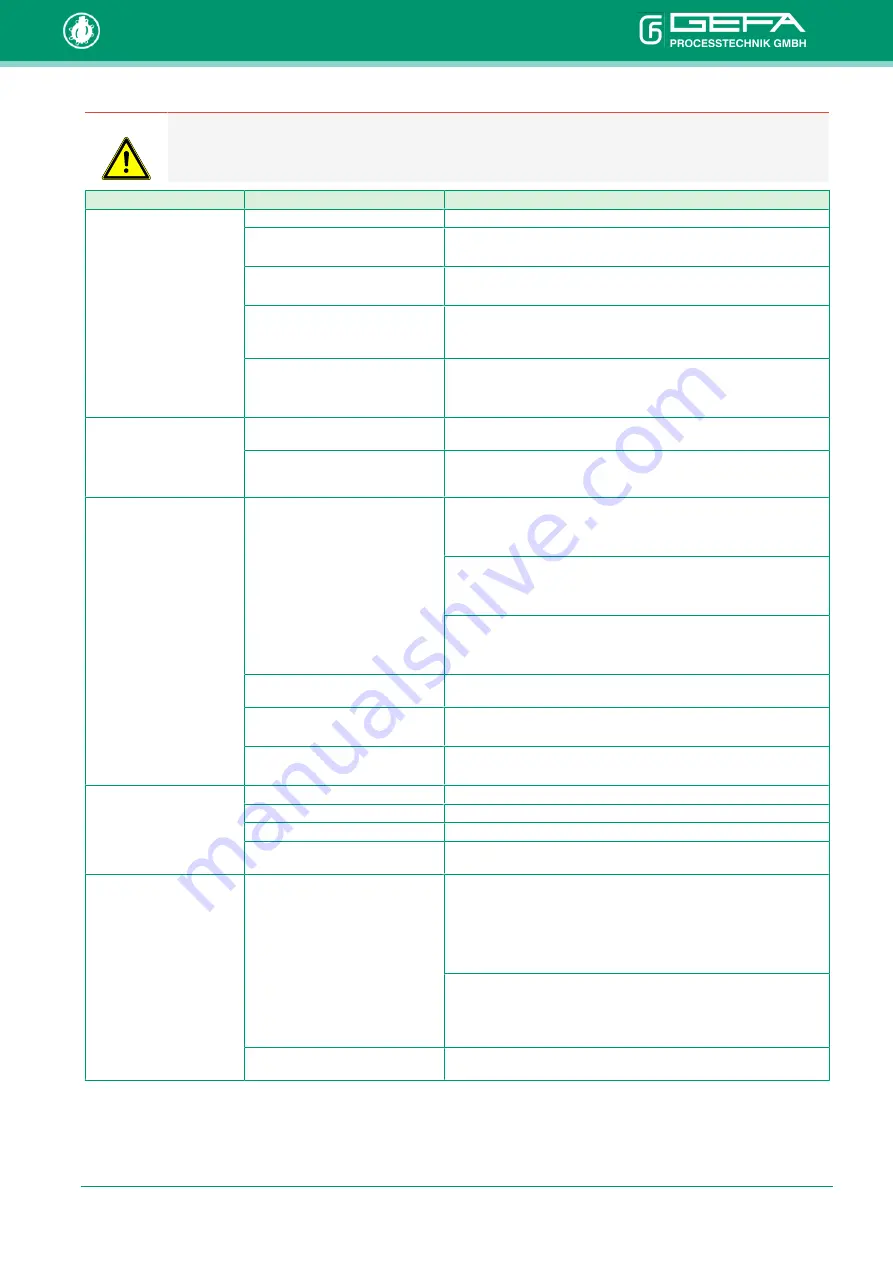
HG1
9 How to proceed in case of malfunctions
DANGER
When eliminating malfunctions, all safety-relevant information in these operating instructions must
be observed.
Type of malfunction
Possible Cause
Action
Leakage at the flange con-
nection to the pipeline
Flange screws are loose
Tighten the flange screws with the specified torque.
Flange seal defective
Loosen flange connection, remove valve and flange seals.
Replace flange seals.
Flange seal not suitable
Loosen flange connection, remove valve and flange seals.
Replace flange seals with a suitable one.
Flange connection not parallel
Loosen flange connection, remove valve and flange seals.
Check plane parallelism of the flange connection and - if not sufficient -
correct.
Damaged sealing surfaces
Loosen flange connection, remove valve and flange seals.
Check sealing surfaces on all flanges and the valve.
Replace flanges or valve if necessary.
Leakage at the
Gland
(Leakage at the
stem)
Gland screws are loose
Tighten the gland packing screws in accordance with the maintenance
chapter.
Gland packing worn out
Replace gland packing in accordance with the maintenance chapter.
Leakage at the seat of the
valve in closed position of
the shut-off element
Valve not completely closed
Manually operated valve:
Open the valve slightly and repeat the closing process.
Check whether the valve is completely closed.
Pneumatically and hydraulically operated valve:
Open the valve slightly and repeat the closing process.
Check and if necessary reset the stroke limits on the actuator.
Electrically operated valve:
Open the valve slightly and repeat the closing process.
Check and, if necessary, reset the limit switches.
Trapped parts between the valve
disc and seat ring
Open the valve fully and remove any jammed parts.
Contamination on the valve disc or
seat ring
Open the valve fully and flush the pipeline.
Open and close the valve several times.
Seat ring damaged
Remove the valve.
Replace seat ring in accordance with the maintenance chapter.
Closing or opening process
sluggish
Insufficient control pressure
Check the control pressure, possibly increase the control pressure.
Control valve dirty
Remove and clean the control valve, install strainer if necessary.
Actuator defective
Check actuator and replace if necessary.
Clogged valve
Remove and clean the valve, if necessary replace defective parts ac-
cording to the instructions of the manufacturer.
Operational malfunction
(Valve disc cannot be
moved)
Actuator elements defective
Pneumatically and hydraulically operated valve:
- Control of the control pressure
- Check whether there is power for the control valve
- Check whether the control valve is defective
Replace elements if necessary.
Electrically operated valve:
- Check whether power is available
- Check whether the motor is defective
- Check whether the limit switch is defective or misaligned
Replace actuator if necessary.
Valve clogged or damaged
Remove and clean the valve, if necessary replace defective parts ac-
cording to the instructions of the manufacturer.
23 / 26
Version 0 • Dokument-Nr. 74572811
Internet: www.gefa.com • E-Mail: [email protected]