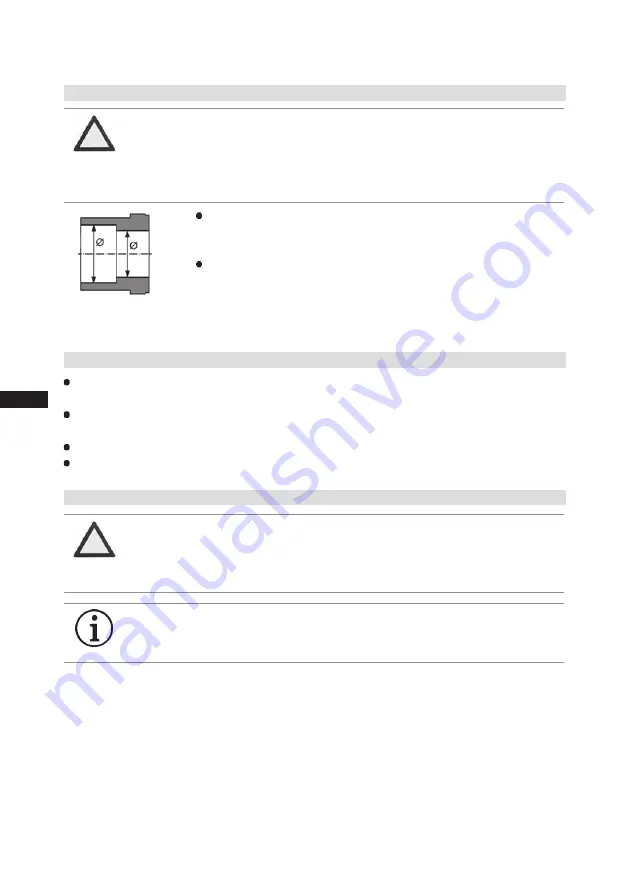
10
D
GB
F
E
96507-11.2019-DGbFEI
4.5 Laying suction and pressure lines
4
|
Compressor assembly
4.4 Pipes
Pipes and system components must be clean and dry inside and free of scale, swarf and layers of
rust and phosphate. Only use air-tight parts.
Lay pipes correctly. Suitable vibration compensators must be provided to prevent pipes being
cracked and broken by severe vibrations.
Ensure a proper oil return.
Keep pressure losses to an absolute minimum.
The
pipe connections
have graduated inside diameters so that pipes with
standart millimetre and inch dimensions can be used. The pipe connections
are suitable for soldering and welding.
The connection diameters of the shut-off valves are rated for maximum
compressor output.
The actual required pipe cross section must be
matched to the output. The same applies for non-return valves.
Abb. 5: graduated
internal diameter
4.3 Pipe connections
ATTENTION Damage possible
Superheating can damage the valve.
Remove the pipe supports therefore from the valve for soldering/
welding. Only soldering/welding using inert gas to inhibit oxida-
tion products (scale).
ATTENTION Property damage possible.
Improperly installed pipes can cause cracks and tears, the result
being a loss of refrigerant.
Lay Discharge and suction gas line stress-free and professional.
INFO
Proper layout of the suction and discharge lines directly after
the compressor is integral to the system’s smooth running and
vibration behaviour.
Содержание HGX44e CO2 Series
Страница 31: ...D GB F E 31 96507 11 2019 DGbFEI ...