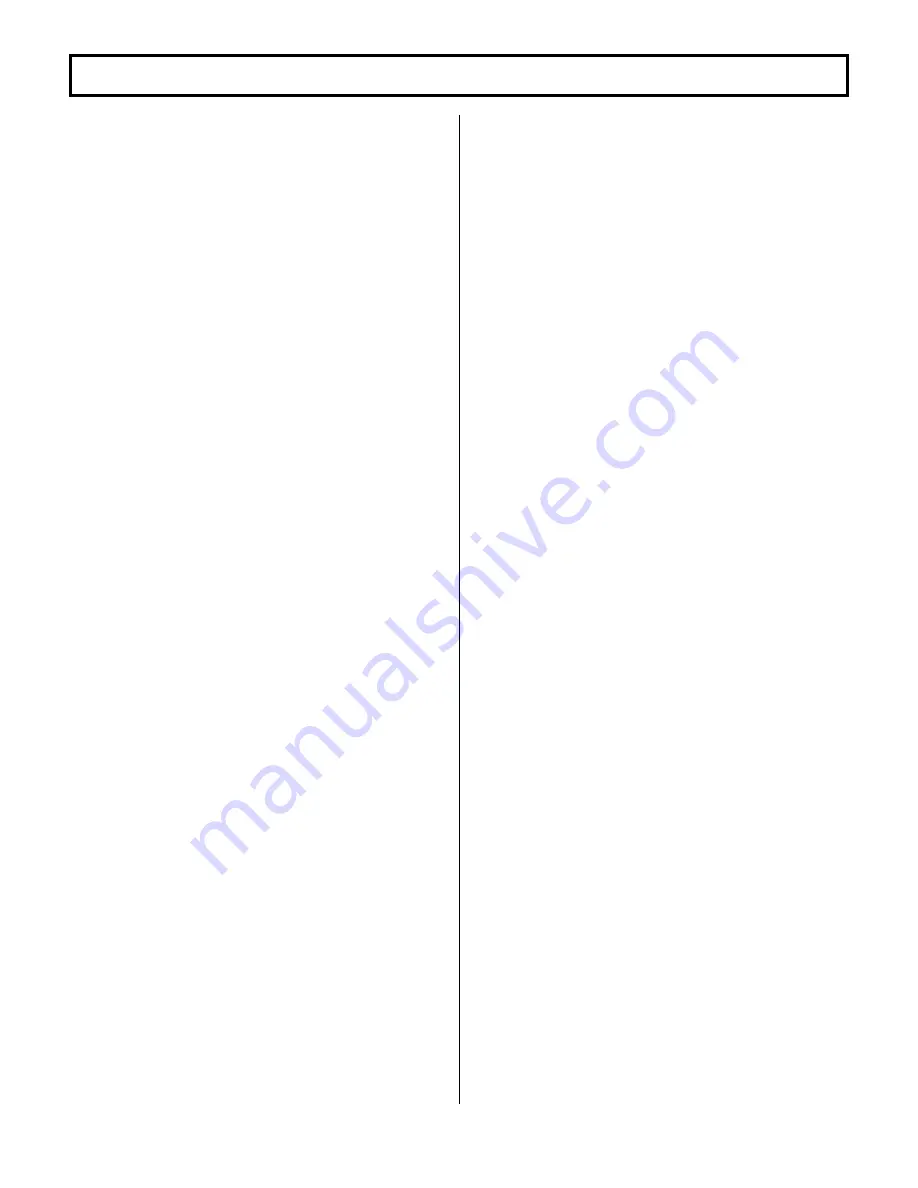
BASIC OPERATION AND FEATURES
SX TRANSISTOR CONTROL
Page 6
July 2001
the level surface, the control automatically transitions back
to the normal running mode.
Section 2.1.5 Ramp Start
This feature provides maximum control torque to restart a
vehicle on an incline. The memory for this function is the
directional switch. When stopping on an incline, the
directional switch must be left in its original or neutral
position to allow the control to initiate full power when
restarted. The accelerator potentiometer input will
modulate ramp start current.
Section 2.1.6 On-Board Coil Drivers and Internal Coil
Suppression
A coil driver for the LINE contactor is on-board the control
card. This contactor must have a coil rated for the vehicle
battery volts, with a maximum current of 1 amp.
Section 2.2 System Protective Override
Section 2.2.1 Start Switch Check
If the key switch is opened, the control shuts off and
cannot be restarted until the start switch opens (see Status
Code –11, described in Section 4.5 of this manual).
Section 2.2.2 Accelerator Volts Hold Off
This feature checks the voltage level at the accelerator
input whenever the key switch is activated. If, at key on, the
voltage is greater than 1.24 volts, the control will not
operate. This feature assures that the control is calling for
low speed operation at start up (see Status Code –8,
described in Section 4.5 of this manual).
Section 2.2.3 Pulse Monitor Trip (PMT)
The PMT design contains three features which shut down,
or lock out, control operation if a fault conditions occurs
that would cause a disruption of normal vehicle operation:
•
=
Look ahead
•
=
Look again
•
=
Automatic look again and reset
The PMT circuit will not allow the control to start under the
following conditions:
•
=
The control monitors armature FET's at start-up and
during running.
•
=
The control will not allow the line contactor to close at
start-up, or will drop it out during running, if the
armature FET's are of low resistance, so as to cause
uncontrolled vehicle movement.
Section 2.2.4 Thermal Protector (TP)
This temperature sensitive device is internal to the power
transistor (Q1) module. If the transistor's temperature
begins to exceed the design limits, the thermal protector
will lower the maximum current limit, and maintain the
transistors within their temperature limits. As the control
cools, the thermal protector will automatically reset,
returning the control to full power.
Section 2.2.5 Low Voltage
Batteries under load, particularly if undersized or more
than 80 percent discharged, will produce low voltages at
the control terminals. The SX control is designed for use
down to 50 percent of a nominal battery voltage of 36-84
volts, and 75 percent of a nominal battery voltage of 24
volts. Lower battery voltage may cause the control to
operate improperly, however, the resulting PMT should
open the Line contactor, in the event of a failure.
Section 2.3 Diagnostics
The control detects the system's present operating status
and this status can be displayed to either the Dash Display
or the Handset.
Section 2.3.1 Status Codes
Section 2.3.1a Standard Status Codes
The SX control has a wide variety of Status Codes that
assist the service technician and operator in trouble
shooting the vehicle. If mis-operation of the vehicle occurs,
a status code will be displayed on the Dash Display for
vehicles so equipped, or be available from the status code
displayed when the Handset is plugged into the “Y” plug of
the logic card.
With the status code number, follow the procedures
outlined in DIAGNOSTIC STATUS CODES to determine the
problem and appropriate corrective action.
Note: The Status Code Instruction Sheets do not purport to
cover all possible causes of a display of a "status code ".
They do provide instructions for checking the most direct
inputs that can cause status codes to appear.
Section 2.3.1.b Stored Status Codes
This feature records the last 16 "Stored Status Codes" that
have caused a PMT controller shut down and/or disrupted
normal vehicle operation. (PMT type faults are reset by
cycling the key switch). These status codes, along with the
corresponding BDI and hourmeter readings, can be
accessed with the Handset, or by using the RS 232