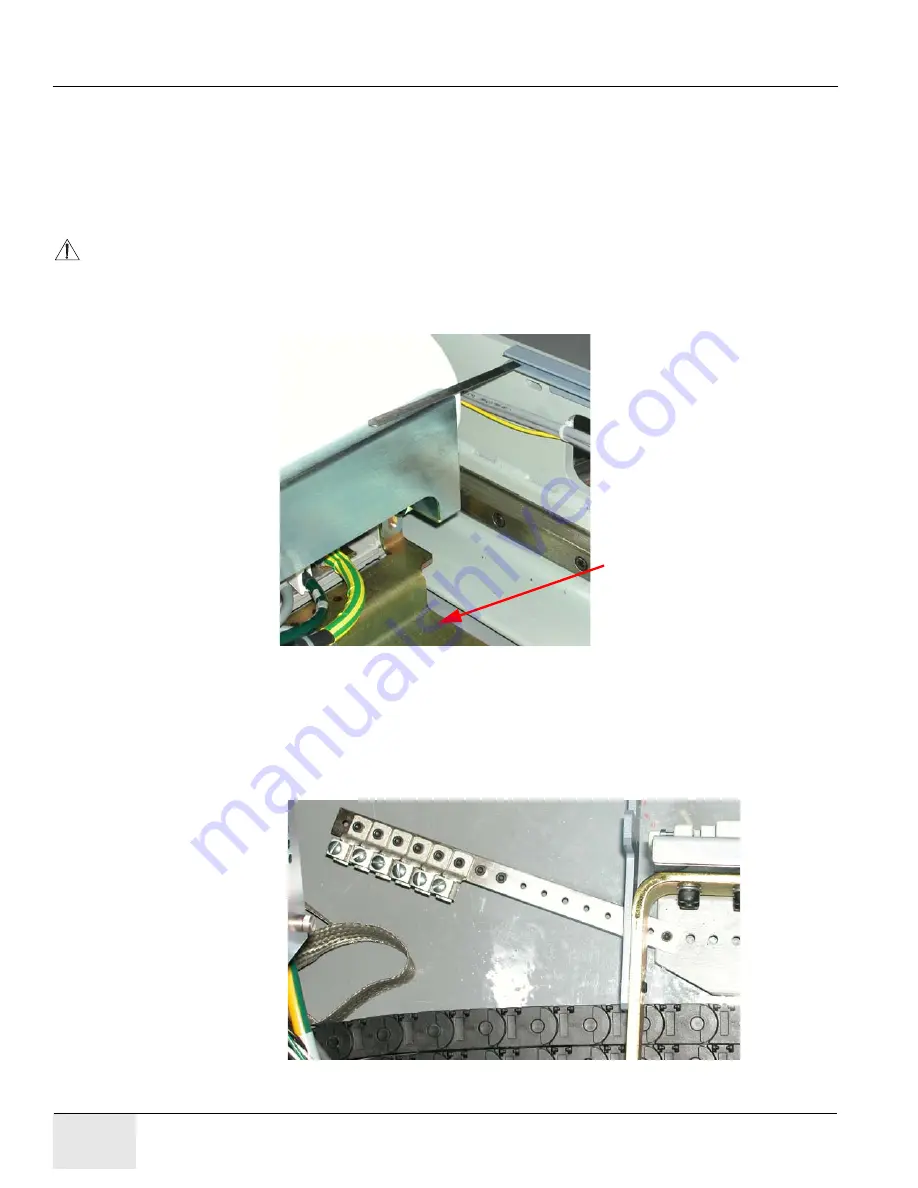
GE H
EALTHCARE
D
IRECTION
2307224-100, R
EVISION
6
D
ISCOVERY
LS S
YSTEM
S
ERVICE
M
ANUAL
Page 194
Chapter 6 - Table
4.) Refer to
. Lay a ruler or the flat edge of an allen wrench across the top of the
bracket to the lower cover guide rail.
5.) Adjust the cover bracket until the top of the bracket is even with the top surface of the lower
cover guide rail.
6.) Repeat the process on the opposite side.
7.) Tighten the bracket hardware and remove the props used to support the cable retractor
bracket
CAUTION
To prevent damage to the floor and the table, carefully push the table base between the CT
and PET positions while watching the cable retractor, retractor plate, and front table bracket
(crossbeam). Make sure the table bracket does NOT drag on the floor or make contact with
the front of the table. Readjust as necessary to clear the floor and table.
Figure 6-118:
Align Cover Bracket with Cover Guide
6.2.7.6 Reposition the Ground Bus Bar
If necessary, reposition the table ground bus to accommodate the roller cover canister. The ground
connections may need to be rearranged to clear the roller assembly. For best results, angle the bus
bar away from the table. (Fasten to the last hole with one screw.)
Figure 6-119:
Reposition the Ground Bus Bar
Watch for interference
with front of table.
Содержание Discovery LS
Страница 1: ...GE Healthcare OPERATING DOCUMENTATION 2307224 100 Rev 6 Discovery LS System Service Manual ...
Страница 2: ...GE HEALTHCARE DIRECTION 2307224 100 REVISION 6 DISCOVERY LS SYSTEM SERVICE MANUAL Page 2 ...
Страница 24: ...GE HEALTHCARE DIRECTION 2307224 100 REVISION 6 DISCOVERY LS SYSTEM SERVICE MANUAL Page 24 Table of Contents ...
Страница 32: ...GE HEALTHCARE DIRECTION 2307224 100 REVISION 6 DISCOVERY LS SYSTEM SERVICE MANUAL Page 32 List of Figures ...
Страница 110: ...GE HEALTHCARE DIRECTION 2307224 100 REVISION 6 DISCOVERY LS SYSTEM SERVICE MANUAL Page 110 Chapter 5 Console ...
Страница 222: ...GE HEALTHCARE DIRECTION 2307224 100 REVISION 6 DISCOVERY LS SYSTEM SERVICE MANUAL Page 222 Chapter 6 Table ...
Страница 242: ...GE HEALTHCARE DIRECTION 2307224 100 REVISION 6 DISCOVERY LS SYSTEM SERVICE MANUAL Page 242 Chapter 7 Gantry ...
Страница 357: ......