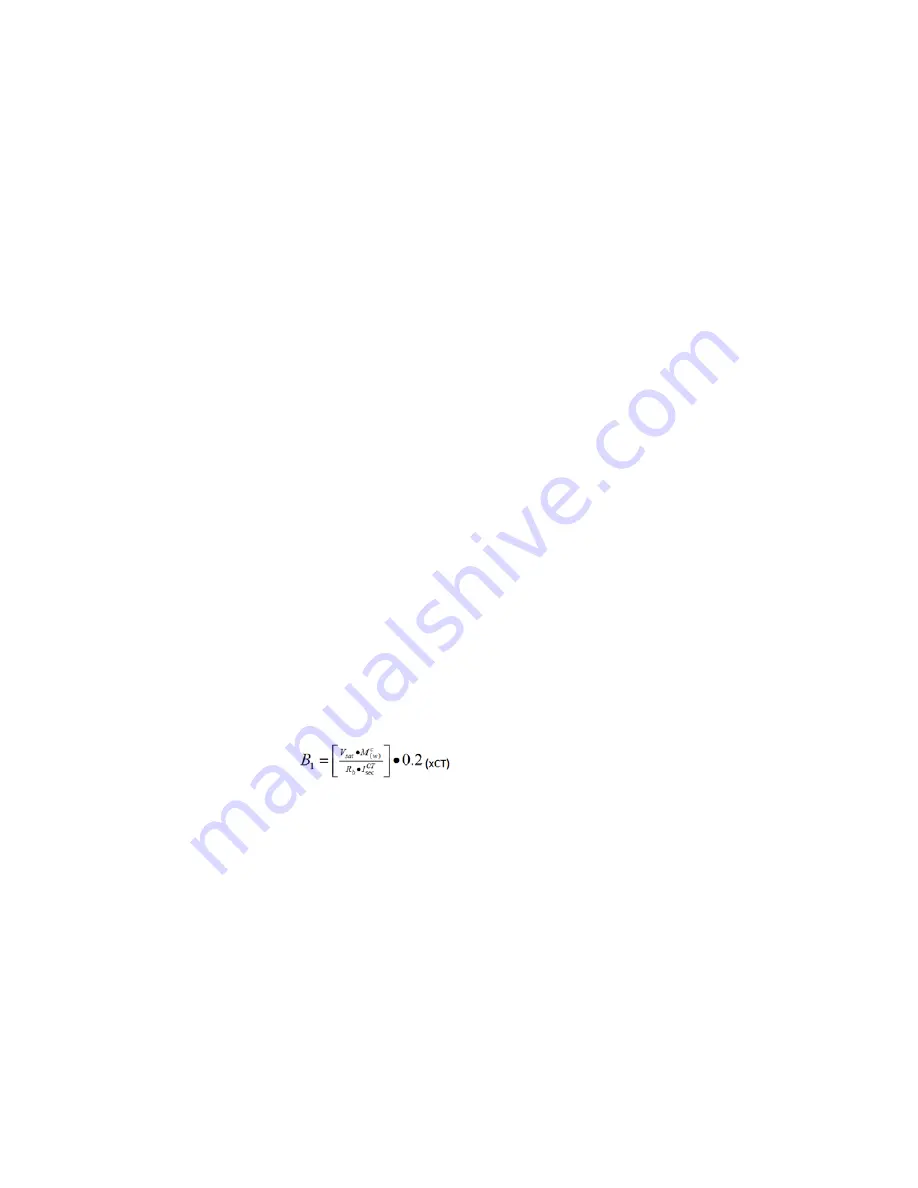
CHAPTER 4: SETPOINTS
PROTECTION
845 TRANSFORMER PROTECTION SYSTEM – INSTRUCTION MANUAL
4–143
Winding 2 rated current =28MVA/(4.16*sqrt(3)) = 3890 Amps
The accuracy of the Class C current transformer is defined in the IEEE standard C37.110 as
not exceeding 10% for symmetrical current magnitudes of up to 20 times the rating for a
standard burden resistance:
117Amps *10% = 11.7 Amps = > 11.7/200 = 0.0585 xCT(w1)
3890 Amps *10% = 389 Amps = > 389/3000*M(w2) = 389/3000*0.4521 =0.0585 xCT (w1)
In the worst case, the errors from the two CTs as expressed in xCT(w1) as a reference can
be summed:
Minimum Pickup = 0.0585 + 0.0585 = 0.117 (0.2xCT setting for Pickup is sufficient)
Slope 1:
This setting defines the desired differential/restraint ratio for detecting internal
faults. The percent Slope 1 setting must be above the differential/restraint ratio during
external faults with non-significant fault current magnitude, but with long lasting DC
component, which is able to cause CT saturation.
The Slope 1 setting can be calculated based on the restraint current during emergency
loading of the transformer:
Restraint current Winding 1 = 117 Amps/200 = 0.585 xCT
Restraint current Winding 2(scaled) = 3890/3000*0.4521 = 0.585 xCT
Differential current = CT error = 0.117 xCT
Slope 1 = (0.117/0.585)*100 = 20%
Adding 5% margin, produces a Slope 1 setting of 25%
Slope 2:
The Slope 2 setting ensures stability during heavy through fault conditions, where
CT saturation results in high differential current. Slope 2 must be set high enough to cope
with the worst case when the CTs from one winding saturate but the CTs from the other
winding do not saturate during external fault. In such case the ratio of the differential to
restraint current can be as high as 95 to 98%.
Break 1:
Break 1 must be set to reflect the through current (restraint current) expressed in
times winding 1 CT (w1) below which CT saturation due to DC components and/or residual
magnetism is not expected. The latter may be as high as 80% of the nominal flux,
effectively reducing the CT capabilities by factor of 5.
Therefore, this setting must correspond to the end of the linear operation of the CT with the
worst characteristic, counting up to 80% remnant flux in the CT core. To calculate this
setting, CTs knee-point voltage and CT secondary burden are needed.
where R
b
= 2 • R
lead
+ R
CTsec
+ R
relay
is the CT burden resistance which includes CT
secondary resistance R
CTsec
, 2 times conductor resistance R
lead
and the relay input
resistance R
relay
.
I
CT
sec
is the CT secondary nominal current. V
sat
is the CT knee-point voltage. The Break 1 is
calculated per the formula above for each winding CT, and then the smallest per value is
entered as a setting.
Break 2:
Break 2 setting defines the beginning of Slope 2 used to provide stability during
heavy through fault conditions, where CT saturation results in high differential current.
Break 2 must be set to the through-fault current which causes the worst CT to saturate,
with saturation free time of at least half power cycle.
To define the degree of CT saturation, the IEEE CT saturation tool can be used:
Содержание 845
Страница 10: ...VIII 845 TRANSFORMER PROTECTION SYSTEM INSTRUCTION MANUAL ...
Страница 74: ...2 30 845 TRANSFORMER PROTECTION SYSTEM INSTRUCTION MANUAL ELECTRICAL INSTALLATION CHAPTER 2 INSTALLATION ...
Страница 123: ...CHAPTER 3 INTERFACES SOFTWARE INTERFACE 845 TRANSFORMER PROTECTION SYSTEM INSTRUCTION MANUAL 3 49 ...
Страница 128: ...3 54 845 TRANSFORMER PROTECTION SYSTEM INSTRUCTION MANUAL SOFTWARE INTERFACE CHAPTER 3 INTERFACES ...
Страница 219: ...CHAPTER 4 SETPOINTS SYSTEM 845 TRANSFORMER PROTECTION SYSTEM INSTRUCTION MANUAL 4 91 ...
Страница 221: ...CHAPTER 4 SETPOINTS SYSTEM 845 TRANSFORMER PROTECTION SYSTEM INSTRUCTION MANUAL 4 93 ...
Страница 222: ...4 94 845 TRANSFORMER PROTECTION SYSTEM INSTRUCTION MANUAL SYSTEM CHAPTER 4 SETPOINTS ...
Страница 223: ...CHAPTER 4 SETPOINTS SYSTEM 845 TRANSFORMER PROTECTION SYSTEM INSTRUCTION MANUAL 4 95 ...
Страница 224: ...4 96 845 TRANSFORMER PROTECTION SYSTEM INSTRUCTION MANUAL SYSTEM CHAPTER 4 SETPOINTS ...
Страница 225: ...CHAPTER 4 SETPOINTS SYSTEM 845 TRANSFORMER PROTECTION SYSTEM INSTRUCTION MANUAL 4 97 ...
Страница 226: ...4 98 845 TRANSFORMER PROTECTION SYSTEM INSTRUCTION MANUAL SYSTEM CHAPTER 4 SETPOINTS ...
Страница 227: ...CHAPTER 4 SETPOINTS SYSTEM 845 TRANSFORMER PROTECTION SYSTEM INSTRUCTION MANUAL 4 99 ...
Страница 396: ...4 268 845 TRANSFORMER PROTECTION SYSTEM INSTRUCTION MANUAL MONITORING CHAPTER 4 SETPOINTS ...
Страница 526: ...6 22 845 TRANSFORMER PROTECTION SYSTEM INSTRUCTION MANUAL FLEXELEMENTS CHAPTER 6 METERING ...
Страница 542: ...8 10 845 TRANSFORMER PROTECTION SYSTEM INSTRUCTION MANUAL DGA HISTORICAL TREND CHAPTER 8 TRANSFORMER M D ...
Страница 544: ...9 2 845 TRANSFORMER PROTECTION SYSTEM INSTRUCTION MANUAL ENVIRONMENTAL HEALTH REPORT CHAPTER 9 MAINTENANCE ...
Страница 546: ...9 4 845 TRANSFORMER PROTECTION SYSTEM INSTRUCTION MANUAL GENERAL MAINTENANCE CHAPTER 9 MAINTENANCE ...
Страница 552: ...A 6 845 TRANSFORMER PROTECTION SYSTEM INSTRUCTION MANUAL REVISION HISTORY CHAPTER A APPENDIX A ...