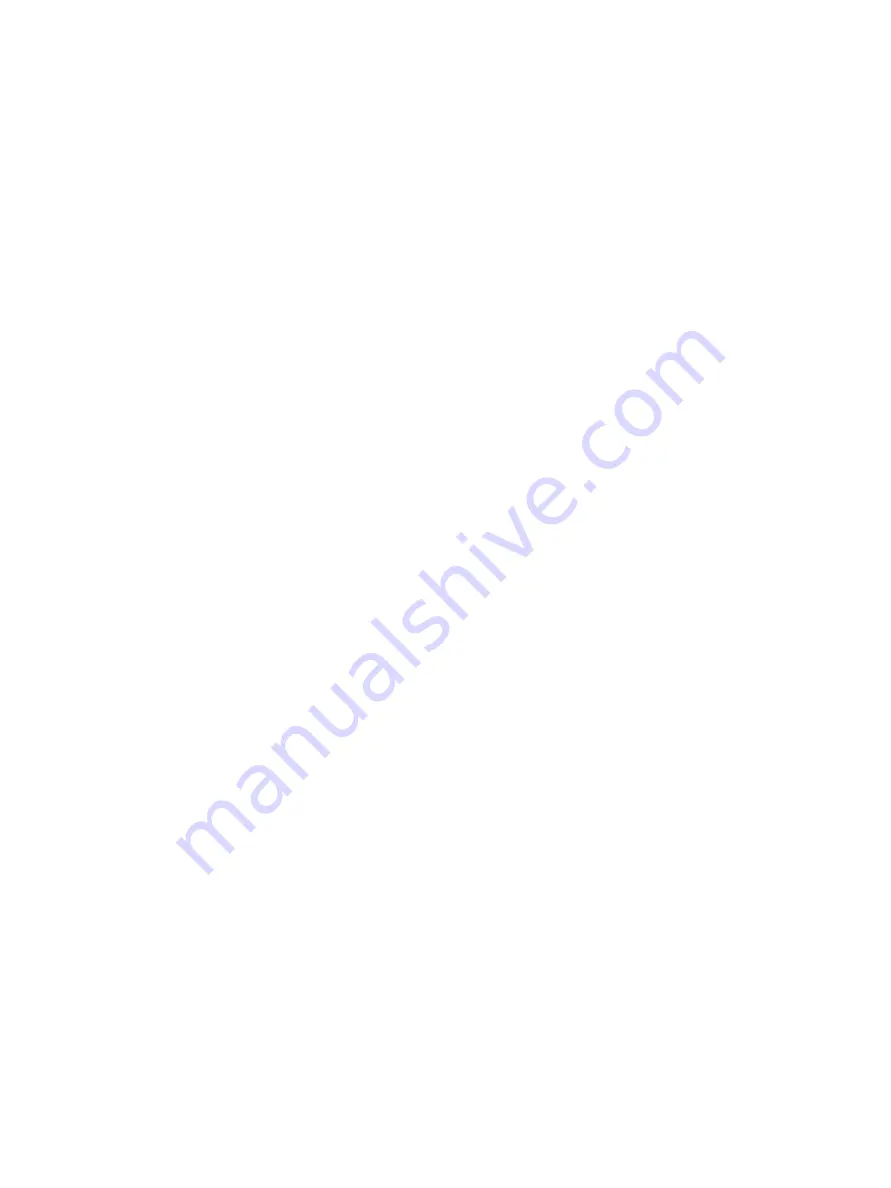
6 | GE Oil & Gas
© 2015 General Electric Company. All rights reserved.
2.
Installation
Prior to installing the valve, clean the pipeline of all foreign matter such as dirt, spatters (welding chips), scale,
oil or grease. Install the valve in the pipeline so that the fluid flows in the direction indicated by the flow arrows
attached to the body, or the fluid flows from "IN" toward "OUT" marked at the connection point.
When securing the lower flange to the pipeline, press the seat ring against the body until it touches the flange
surface of the pipeline. The lower flange and the pipeline pinch the seat ring and the pipeline’s gasket which is
prepared in advance, and tighten the pipeline bolts rigidly.
If the valve is installed in a horizontal position, be sure to take the support from the yoke or other part of the
actuator.
In case of the extension type bonnet, do not apply insulation to the extended portion.
Provide the required air tubing for the signal pressure and air supply, and the electrical wiring to the
positioner. Make sure no air leaks from the air pipeline.
3.
Maintenance
When the control valve needs to be disassembled for inspection, cleaning or polishing the valve seat, follow
the procedures described below.
It explains the following procedure as an example of the attached drawing (MNS-148001).
3.1.
Disassembly
Shut off all air supplies, disconnect the tubing for the air supply and the positioner signal pressure, and
the air tubing from the volume tank.
To disassemble the valve, it must be removed from the piping. Bring a chain block over the valve to
remove it from the piping for disassembly and reinstall it after reassembly.
1)
Run a strong rope through the actuator yoke and remove the valve retaining bolts from the piping
while slightly pulling the valve upward.
If the valve is installed in a horizontal position, also run a rope around the body so that no lopsided
force is exerted on the valve, when disconnecting the valve from the pipeline.
2)
Seat ring (12) and gasket (11) can be taken apart, after the valve body is removed from the pipeline.
At this time, pay attention not to be damaged with the seat ring.
3)
Remove the positioner linkage from the split clamp (18) which connects the piston rod (19) of actuator
and the plug (13) of the body side.
4)
Loosen the nut (16) or bolt (26) of the split clamp (18) in order to remove the split clamp (18).
Take the record on the depth of insertion of the stem and the position of the split clamp so that they
can be reassembled to the same dimension.
5)
Remove the seat ring (12) first from the bottom of the body. The actuator can also be removed by
loosening the drive nut (5) which connects the body (10) and the yoke (14). However, in case of the
stud and nut type connection that connects the yoke to the body by the stud (23) and nut (24), loosen
the nut (24) to remove the actuator from the body.
Remove the packing flange (3) and the packing follower (4), after loosening and removing the stud nut
(2) which have tightened the packing flange. In the case of keeping connecting the valve body and the
yoke, the packing flange can be passed through the space between the bottom end of the piston rod