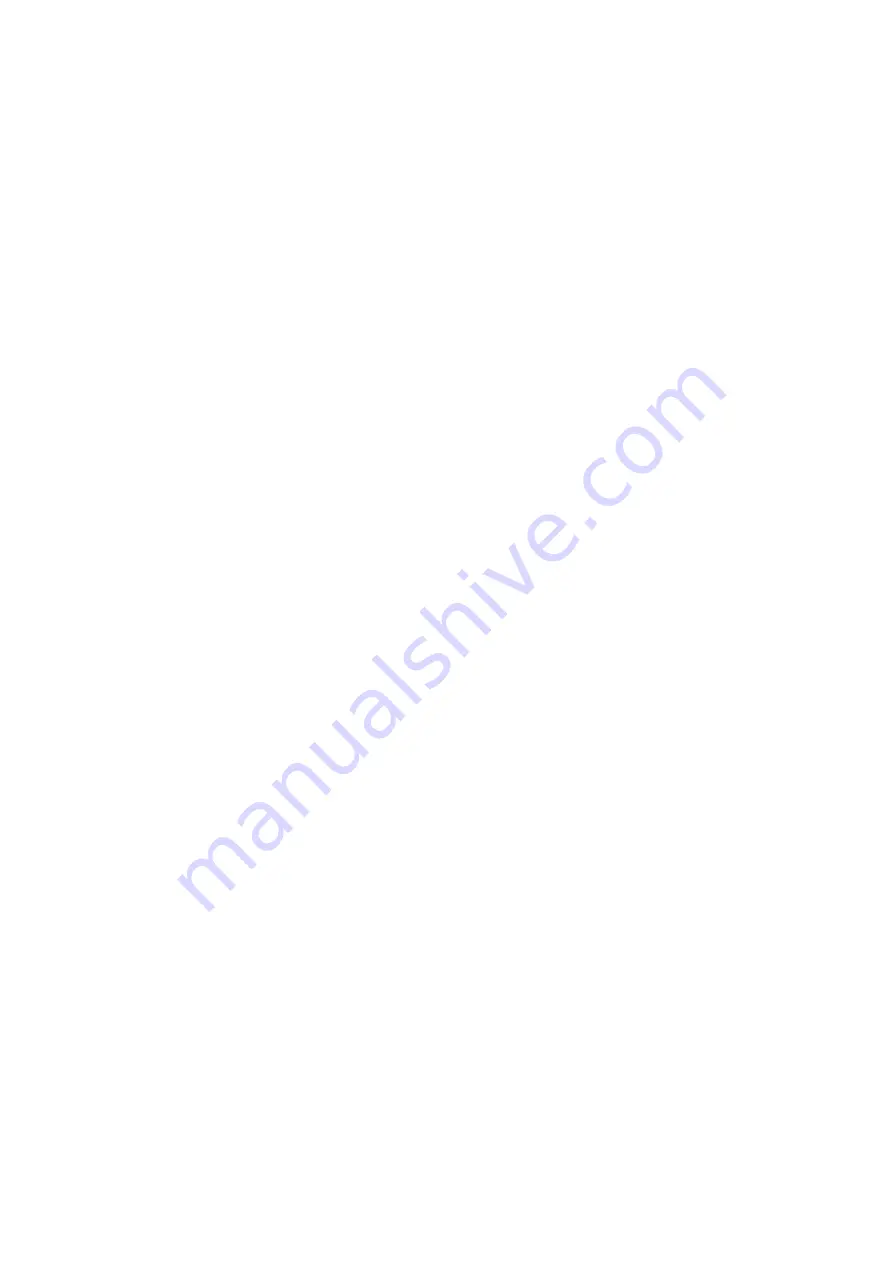
8
SENSOR SUPPLY ADJUSTMENT (CATALYTIC SENSOR)
Factory set – no further adjustment required unless a change of sensor type is being made.
For ease of setting, measurements are taken across a 1ohm resistor (located on each sensor board) which is
connected in series with the supply to the detector head. Current required by each type of sensor is (VQ21–300mA/
VQ23 DCP–335mA) therefore, measuring mV across the 1 ohm resistor at test point TP1 or TP2 (on the mother
board) and sv test point on each sensor board, will provide a mV reading proportional to mA’s supplied, adjustment
may be carried out using the sensor volts adjustment potentiometer.
Alternatively the sensor voltage may be set at the detector head across terminals P and W (VQ21 2v/VQ23 DCP
2.5v) and again use the sensor volts adjust potentiometer.
4–20MA OUTPUT ADJUSTMENT
Adjustments: With the load connected to the appropriate 4~20–mA output terminal (typically 100 ohms) and a
digital volt meter connected to the test pins TP3 + TP4 – ensure that the sensor is in clean air, and that the instrument
is reading zero.
Adjust the 4mA potentiometer to read 4mV on the digital voltmeter.
Using the appropriate sensor zero potentiometer adjust the alarm panel digital display for full scale reading.
Adjust the 20mA output potentiometer until the digital voltmeter reads 20mV
Return the alarm panel digital display reading to zero by readjusting the zero potentiometer.
Service – routine attention
The owner or occupier of the premises should place the supervision of the system in the charge of a responsible
executive whose duty it should be to ensure the day to day operation of the system and to lay down the procedure
for dealing with a gas alarm or fault warning. To ensure reliability an agreement should be negotiated for regular
servicing. When a service contract cannot be arranged an employee with suitable experience of electrical equipment
should be trained to deal with the more simple servicing and instructed not to attempt to exceed the scope of such
training.
Liaison should be established with those responsible for maintenance of the building fabric or redecoration etc. to
ensure that their work does not cause a fault or otherwise interfere with the operation of the gas alarm installation.
Particular attention appertaining to the Detector Head.
The operating instructions should be kept available preferably with the control unit, all faults, service tests and
routine attention given should be recorded.
DAILY:
A check should be made that any fault condition which may be indicated is in fact being attended to and that
all other indicators are normal.
WEEKLY:
In plants involving a high risk process or having gases which may cause loss of sensitivity a check on
calibration should be carried out.
TWICE YEARLY MAINTENANCE SCHEDULE
1. All zeros at the control unit to be checked, logged and aligned.
2. Each detector to be gas tested and reading logged (sensitivity checked).
3. Field indicators to be tested.
4. All alarm set points checked and re–aligned.
5. Lamp Test.
6. All faulty parts replaced where required.
7. All filter elements checked and replaced as necessary.
8. Power supply – complete functional check.
9. Visual inspection made to confirm that all cabling fitting and equipment is secure, undamaged and adequately
protected.
FAULT DIAGNOSIS
Unable to zero meter 1. Sensor open circuit
2. Sensor leads incorrectly connected
3 Alarm card not positioned correctly
No front panel indication – Check ribbon cable is connected correctly
Содержание 404+ Series
Страница 23: ......