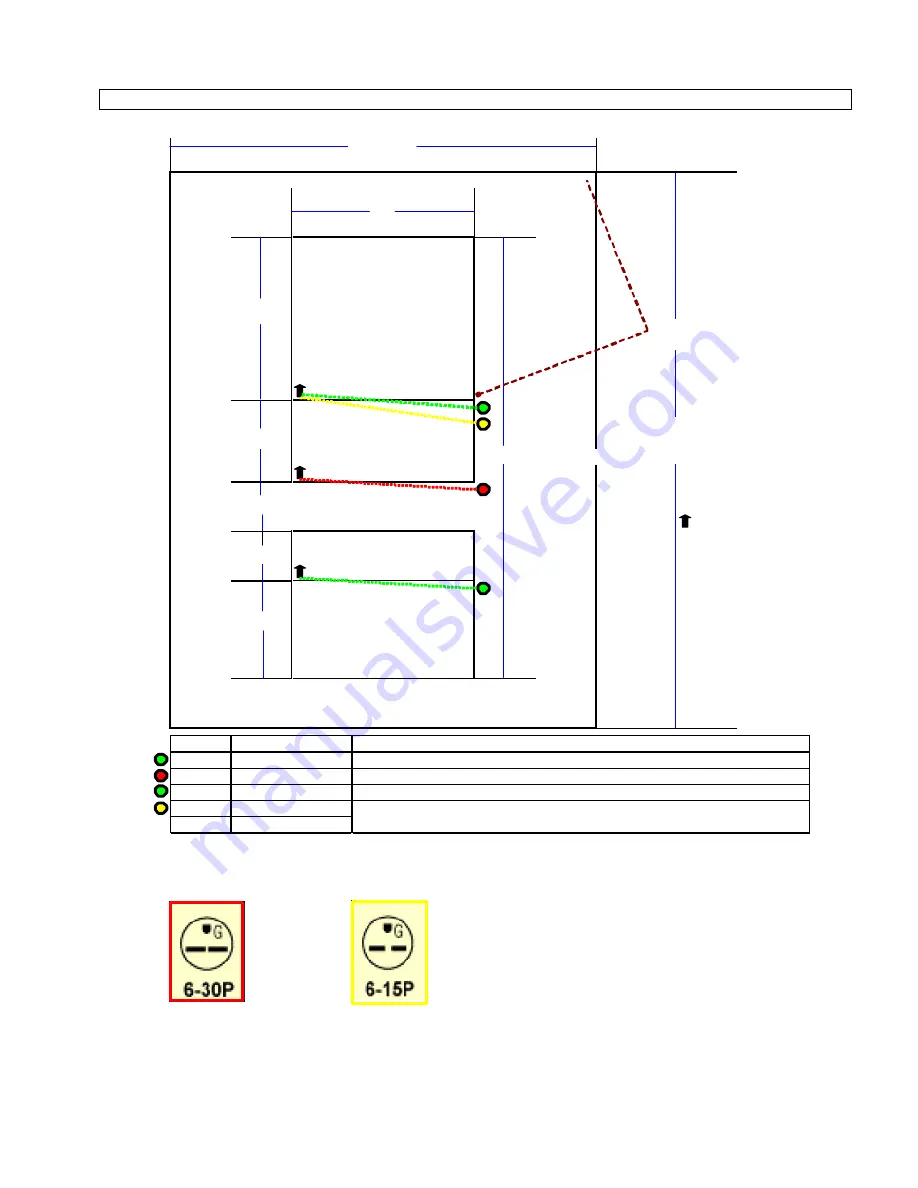
GBC 5031TS
OPERATION MANUAL
© 2006 General Binding Corporation
28
SPACE AND POWER REQUIREMENTS FOR THE 5031TS SYSTEM
120" (10 ft)
Recommended work
space: 10' x 17.5'
52"
49"
Feeder
Feeder swings out for
Film loading and unloading
- - Nema 5-15
- - Nema 6-15
28"
Laminator
139" -
Minus a 2" overlap at feeder and laminator.
- - Nema 6-30
15"
AC Cord location
17.5"
Cutter
- - Nema 5-15
31.5"
Stacker
Tray
Machine
Wire and Plug
Feeder
115 VAC 2 Amp
Wired with 69" cord, NEMA 5-15 plug
Laminator 220 VAC 30 Amp
Wired with 65" cord, NEMA 6-30 plug - Single Phase (see below)
Cutter
115 VAC 2.2 Amp Wired with 69" cord, NEMA 5-15 plug
Air Unit
220 VAC 9.6 Amp
Air Unit
S
uggest NEMA 6-15P
NEMA 6-30P
NEMA 6-15P
Notes:
Note:
Drops or poles recommended, outlets should be no higher than 24" above floor
211" (17.5 ft)
Power Requirements
O
pe
ra
to
r S
id
e
of
S
ys
te
m
Does not come with wire, plug, or switch. Suggest mounting switchbox between AC
source and Air Unit. Mount on feeder under feeder on/off switch. 220vac Single Phase.
Содержание 1711718
Страница 1: ...GBC 5031TS Roll Laminator 1711718 Instruction Manual...
Страница 2: ...5031TS OPERATION MANUAL...