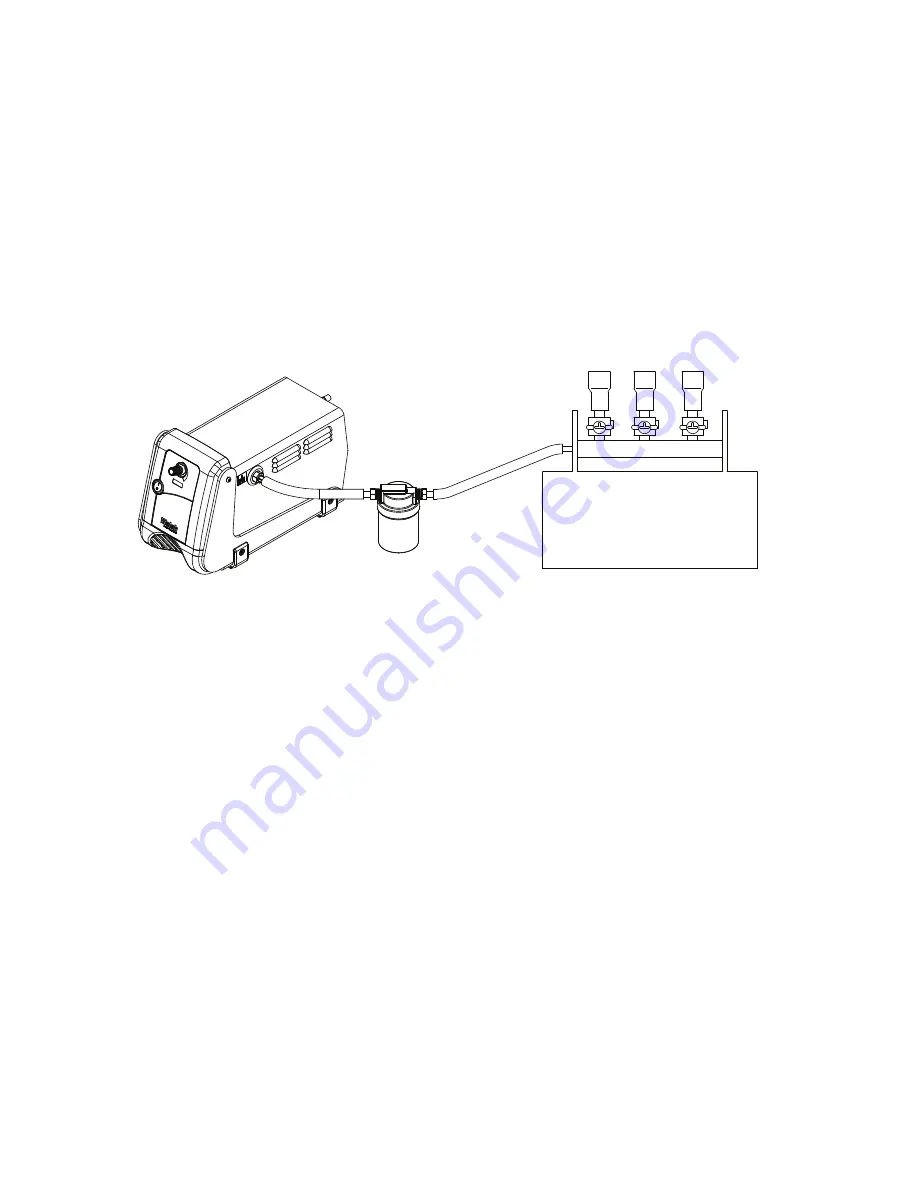
Section 3: OPERATION
3.10 Starting a Welch Dry Vacuum Pump
Before attaching the pump to a system it is well to familiarize yourself with the function and action of
the pressure vacuum pump which you have acquired. Review the power requirements as described
in Section 2.6. Welch recommends running the pump for a few minutes to warm it up before use. The
warm-up improves the pumps ability to pass water and organic vapor. A warm pump will handle more
vapor without liquefying it than a cold pump.
3.11 Cleanliness
Take every precaution to prevent foreign particulates or liquid from entering the pump. Particulates will
damage the pump’
s performance. If you fi nd that particulates or liquid will come off during the process
of evacuation, a simple liquid trap can be made out of readily available material for protecting the pump.
The trap would consist of a fi ltering fl ask placed between the pump and the vacuum chamber.
Dry Vacuum Pump
Liquid Trap
Filtration Manifold
3.12 Leak Detection
Eliminating all leaks in a vacuum system is a key to obtaining maximum vacuum. The pump must
remove this added volume of leaked gas to maintain the desired vacuum. Leaks can be located by
slightly pressuring the system and painting the suspected area with a thick soap solution. Escaping air
will produce soap bubbles.
3.13 Operating Pressure Range
Vacuum pumps are designed to be run from slightly below atmospheric to their maximum vacuum level
on the intake side. Consult the Specifi cation Table in the back of this manual for the ratings for your
model.
3.14 The Effects of Unwanted Vapor
Systems which contain undesirable vapors cause diffi culty both from the standpoint of attaining
desirable ultimate pressures. A vapor is defi ned as the gaseous form of any substance which is usually
a liquid or a solid. Water, oil, and mercury vapors are three of the more common vapors encountered in
typical vacuum systems. When such vapors exist in a system, the vapors or mixtures of gas and vapors
are subject to condensation within the pump; the precipitated liquid may thus ultimately solidify on the
PTFE heads and diaphragm causing corrosion.
3.15 Shutdown Procedures
After use, Welch recommends the pump be run for about 2 minutes disconnected from the vacuum
process. The air pumped through the mechanism will purge out water vapor or droplets of condensate
that may have formed on the inside of the pump. This purge of the pump mechanism helps prevent
build up of solute crystals inside of the pump head. Over time, these crystals will shorten pump lifetime.
10