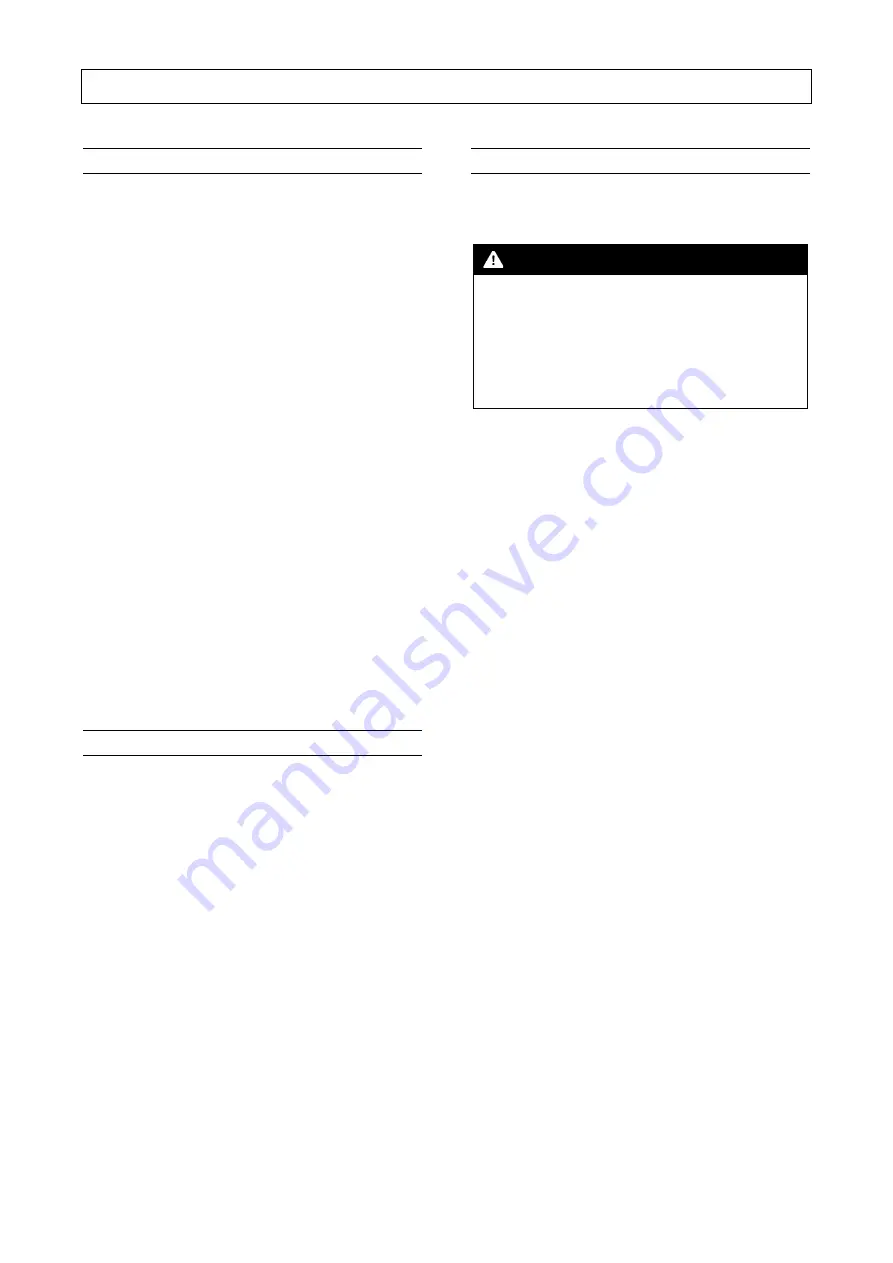
5 Design and functioning
21
5.3
Oil circuit
The oil flows from the pressure reservoir (- 6 -) into the
oil thermostat (- 22 -). With oil temperatures < 131 °F
the oil flows via the by-pass of the oil cooler directly into
the oil filter (- 11 -) and is then injected into the screw
compressor (- 4 -).
With oil temperatures of between 131 °F and 158 °F the
oil flow is divided and fed into the oil cooler (- 12 -) and
the by-pass.
With oil temperatures above 158 °F the entire oil flow is
directed via the oil cooler through the oil filter into the
screw compressor.
The oil separated by the oil separator element (- 7 -) is
fed through an oil scavage line to the screw
compressor.
The entire oil circulation is based on a differential
pressure in the system. Considering the pressure
difference of approx. 29 PSI within the oil circuit, the oil
is then injected into the screw compressor with approx.
116 PSI at a reservoir pressure of e.g. 145 PSI.
When the screw compressor is in the off-load mode, a
sufficiently high pressure differential and thus the
required oil injection quantity is achieved owing to the
fact that when the suction regulator (- 2 -) is closed, a
vacuum pressure occurs in the intake connection and at
the place of injection, and an overpressure of approx.
22 PSI (residual pressure) in the reservoir.
5.4
Air circuit
The intake air passes through the intake filter (- 1 -) and
the suction regulator (- 2 -) into the screw compressor
(- 4 -). During the compression process, the intake air is
cooled via the injected oil. The developed air/oil mixture
flows tangentially into the pressure reservoir (oil
reservoir) (- 6 -). After pre-separation and subsequent
fine separation by the separator element (- 7 -), the
compressed air with a low oil content is fed via the
minimum pressure valve (- 12 -) and the air cooler
(- 14 -) into the consumer network.
5.5
System control
(See also operating instructions for the compressor
control GD Pilot TS)
DANGER
The lower control area of the operating
cylinder (2.1) is generally pressurised (even
when the system is at a standstill).
•
Before working on the suction regulator
this must be bled by carefully
unscrewing the return valve (2.3).
Standstill of the system
•
If the plant is shut down, the suction controller (- 2 -)
is closed by pressurisation in the lower control area
of the operating cylinder (-2.1-).
•
The solenoid valves (- 19 - (Y1) and - 20 - (Y4)) are
de-energized.
•
The pressure reservoir (- 6 -) is unloaded to
atmospheric pressure by means of the relief valve
(-21-).
Starting the system
•
The drive motor (- 3 -) starts up in the Y-mode.
•
The suction regulator (- 2 -) is closed.
•
The compressor aspires a certain amount of air
through a bypass valve. Pressure builds up in the
reservoir.
•
Oil is supplied to the screw compressor (- 4 -) due to
the pressure differential between the pressure
reservoir (- 6 -) and the place of injection in the
screw compressor (- 4 -).
•
When the drive motor (- 3 -) switches to
Δ
operation,
solenoid valves (- 19 - (Y1) and - 20 - (Y4)) perform
a switching operation, since they are energized.
•
The air circulating in the system flows through
solenoid valve - 19 - (Y1)) into the upper control
chamber of the actuator (- 2.1 -). The relief valve
(-21-) is closed.
•
The pressure control valve (- 2.2 -) in the suction
regulator (- 2 -) opens.
•
At a reservoir pressure of approx. 4.5 bar/65 PSI the
minimum pressure and non-return valve (- 15 -)
opens.
•
Compressed air is now delivered into the consumer
network.
•
The system is now in load running mode.
Содержание L30RS
Страница 2: ......
Страница 59: ...12 Annex 57 Fig 31 all dimensions in mm...