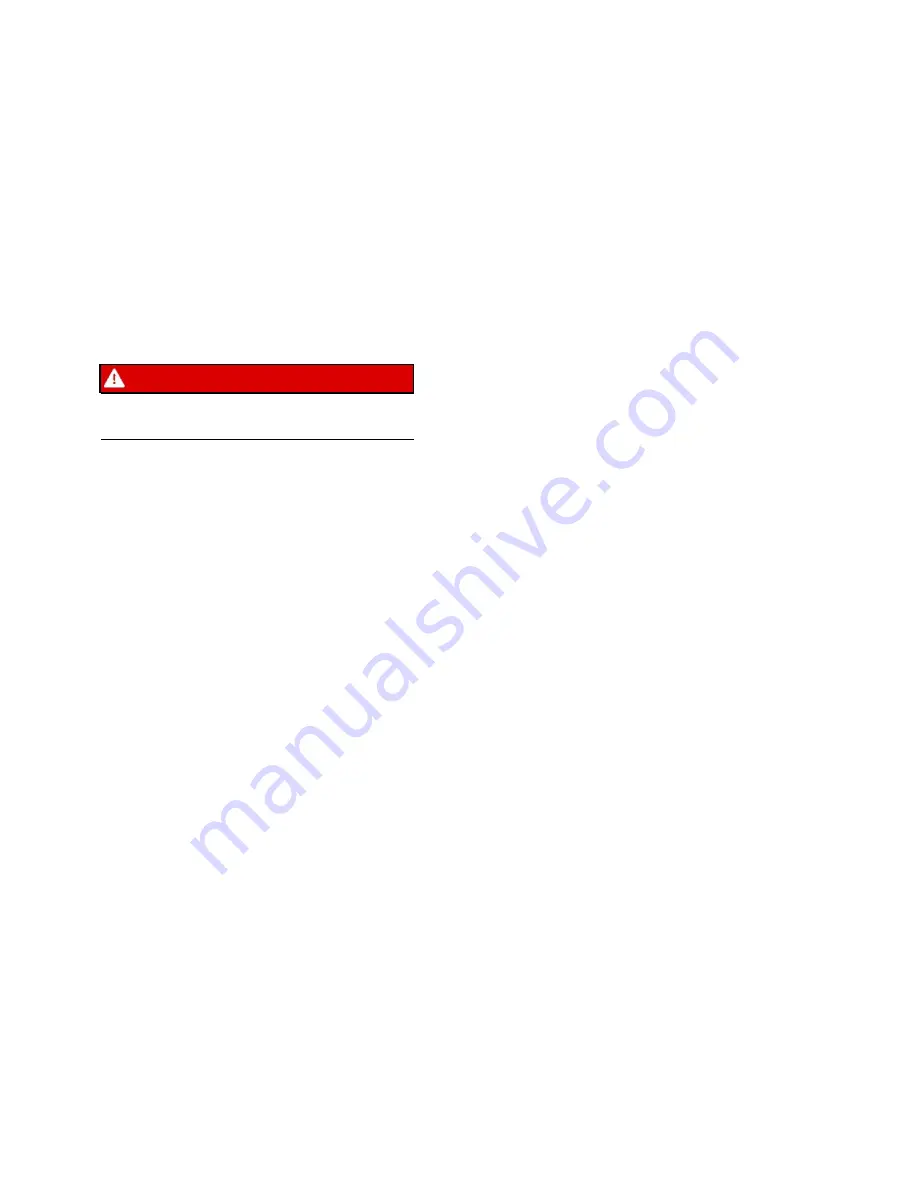
13-25-637 v02 Page 7
• the use of improper fuel
• failing to use genuine Gardner Denver replacement parts
• alterations to the equipment.
The warranty
or liability terms of Gardner Denver’s Terms and
Conditions are not expanded by the foregoing.
Any independent alterations to the compressor
equipment/station or installing components which have not been
approved by the manufacturer (e.g., separator) will result in the
loss of the CE mark, or other factory certifications. As a
consequence, all liability and warranty claims against the
manufacturer will be terminated.
Safety Regulations
Technical Changes
We reserve the right to make changes in the course of technical
development without prior notice.
DANGER
Always observe the safety regulations in
Section 4 of the user manual.