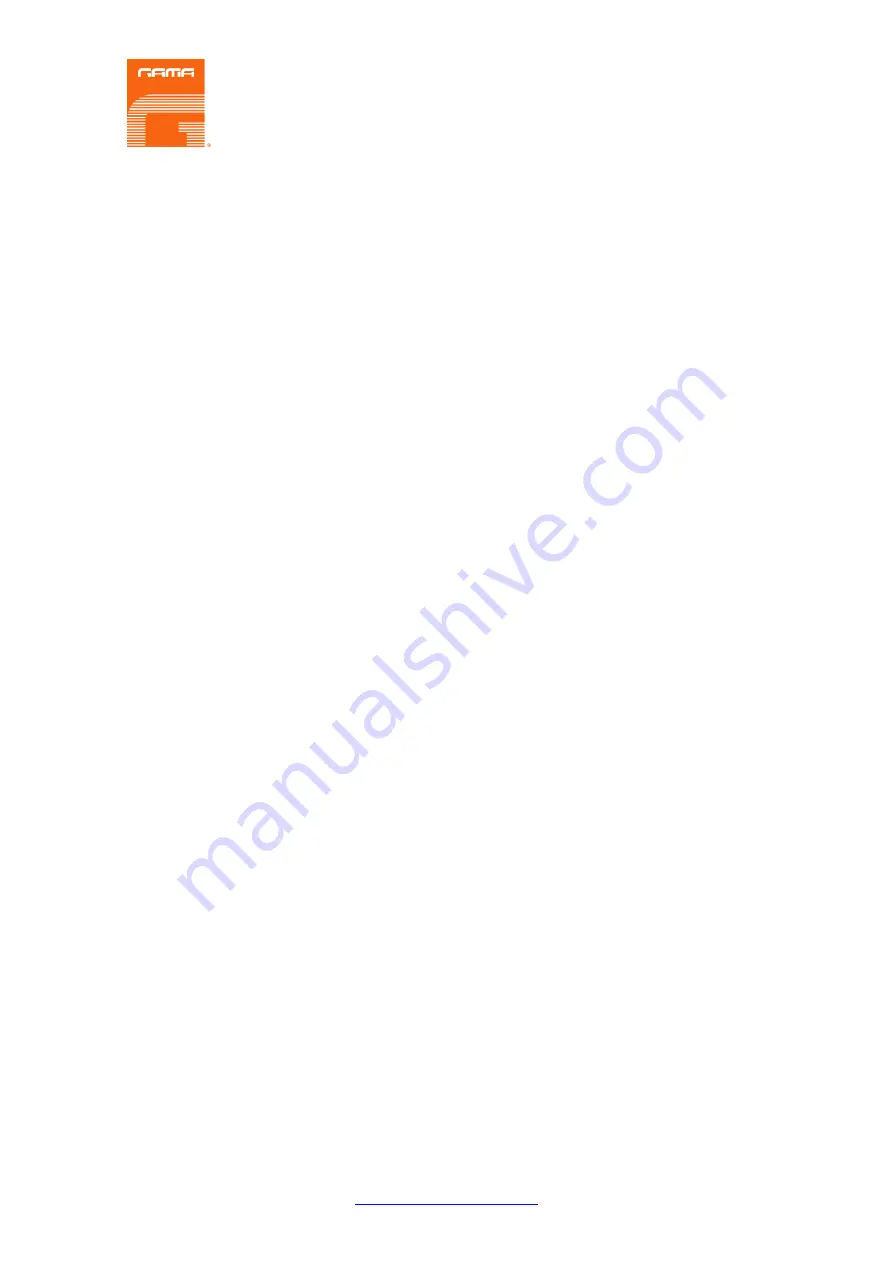
evolution G-50 H
Service Manual
42/48
Issue 3.2
Metering pumps
WARNING!
Before proceeding with maintenance works, make sure that all push
buttons are switched off, the general switch is in the off position, and the Unit is
unplugged from the power supply. Never handle the control panel interior while the Unit
is plugged into the electricity grid. Dosing pumps are components that work under
pressure, do not open any connections or perform any repair or maintenance work on
components submitted to pressure until all pressures have been completely released.
When the pump works properly, it is not uncommon for a small amount of resin to filter through
the joints and reach the visible part of the pump axis. Periodically inspect the axis and clean the
residue when dosing pumps are stationary and the machine is switched off.
Disassemble and clean the dosing pumps annually, despite no obvious signs of leaks. Use this
time to completely replace the joints and bearings given that, if you reassemble an element that
does not seem damaged, it can cause premature wear in the remaining components (the NR-
00065 Components Manual includes the joint kits that correspond to each pump model and
size). Pump distribution bases must also be inspected, checking that the ball valves show no
signs of wear, dent
s or marks that affect the pump’s proper operation.
Perform a daily inspection of the Isocyanate pump lubrication bowl and check the condition of
the DOTP plasticiser oil it contains. Replace the oil when you observe colour changes or when it
shows signs of solidification. If this circumstance persists, replace the isocyanate pump joints
using the corresponding kit.
In cases where the machine is submitted to large workloads or special work conditions,
disassemble, clean and replace the dosing pump joints every six months.
Inspect rods, pistons and inside the sleeves for marks or scratches that may cause leaks or
premature damage to the joints.
Only qualified personnel will be authorised to replace dosing pump joints, since they have the
required expertise to that effect.
NOTICE:
Three special tools can be used to simplify the seal assembly. Tools A and B
to insert the shaft seal into the seal housing and tool C for the packing retainer flange
assembly insertion through the shaft (see Table 3 in pg.43)
.