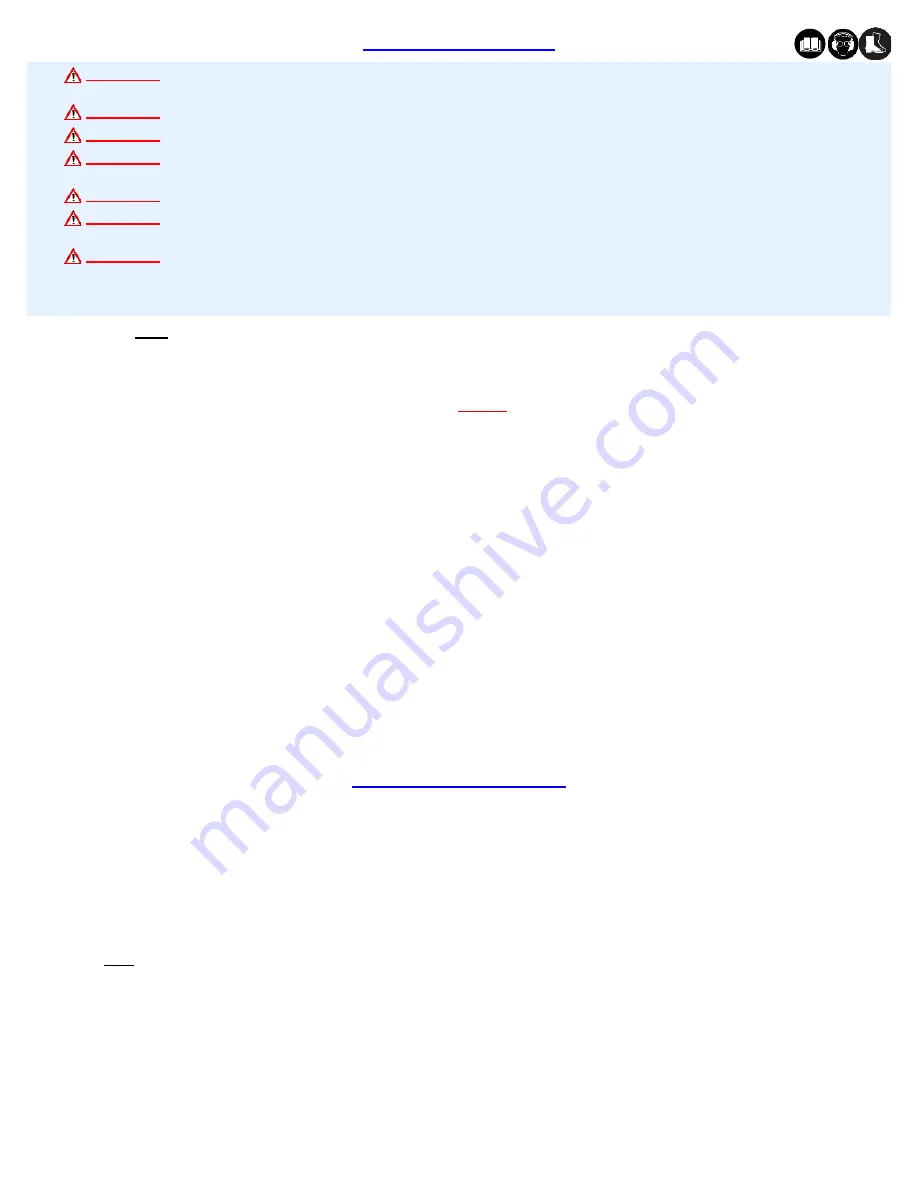
12
GB947 HYDRAULIC POWER UNIT
8/23
DAILY MAINTENANCE
WARNING
:
Pump must be maintained in a safe working condition at all times and examined on a daily basis for damage or
wear. Any repair must be done by qualified personnel trained on Gage Bilt procedures.
WARNING
:
Excessive contact with hydraulic oil and lubricants must be avoided.
WARNING:
Maintenance personnel
MUST
read and understand all warnings and cautions.
WARNING
:
Disconnect pump from its power source before performing maintenance, cleaning or when replacing worn or
damaged components. Severe personal injury may occur if power source is not disconnected.
WARNING:
Read Safety Data Sheet documents for all applicable materials.
WARNING:
To avoid crushing and related injuries, NEVER work on, around, or under a lifted load before it is properly
supported by the appropriate mechanical means. Never rely on hydraulic pressure alone to support load.
WARNING:
Avoid the use of extension cords. If necessary, for extension cords lengths up to 25 ft (7.6 m), use SJT
-
14X3 or
heavier. For cords up to 50 ft. (15.2 m), use SJT
-
12X3 or heavier. For extension cord lengths up to 100 ft. (30.4 m),
use SJT
-
10X3 or heavier. NEVER use a 3 prong adapter. To avoid electrocution hazard connect ONLY to a properly
grounded source. Connect to GFI outlet ONLY.
Note:
•
Dispose of hydraulic oil in accordance with manufacture safety datasheet.
•
All tool materials are recyclable except rubber o
’
rings, seals and wipers.
•
To ensure smooth operation, bleed air from the system by fully advancing and retracting the cylinder several times.
•
Avoid the use of extension cords if possible. (See
warning
above).
The performance of any tool depends upon good maintenance practices. Following these minimal requirements daily will extend the
life of your pump. Scheduled inspections to detect and correct minor problems are part of an effective preventative maintenance program.
Owners and operators of this equipment shall be aware that the use and subsequent repair of this equipment may require special
training and knowledge. Proper care by operators is necessary in maintaining full productivity and reducing downtime.
* Keep areas around the pump obstruction free in order to provide good air flow around the pump and motor. Keep pump and motor clean.
* Inspect hoses and couplings for wear, damage and leaks. (Replace/Repair if necessary). Couplings must be clean and free of dirt.
* Verify that hydraulic hose fittings, couplings and electrical connections are secure. Tighten, Replace or Repair if necessary.
* Check hydraulic oil every 40 hours of operation and add/replace hydraulic oil based on recommendations below.
* Keep hydraulic system and exterior surface clean.
* Any unusual differences noted, would suggest this course of action before further operation: Drain and discard used oil. Refill with new oil.
* Check electrical cord for damage or wear before and after each use. Replace if necessary.
* Do not operate this powerunit if line voltage varies ±5% from recommended specifications (120V/230V).
SEE TROUBLESHOOTING (PGS. 14
-
15) FOR FURTHER GUIDANCE.
WEEKLY MAINTENANCE
Keep the hydraulic system filled with hydraulic oil. We recommend DEXRON® III or equivalent. Use only recommended oil as other
hydraulic oil may result in pump failure and will void your warranty.
*
Changing hydraulic oil: Change oil every 300 hours or once a year depending on use and environmental conditions. When changing
oil, clean filter screen with nonflammable solvent, blow dry before reassembling. (Note: Replace filter screen if damaged).
a) Remove drain plug, tilt the pump, then pour used oil into a sealable container.
b) Clean area around vent cap hole. Fill hydraulic oil to about
2” (50.8
mm) from top of reservoir plate, then reinstall vent cap.
Wipe area clean (if spillage occurs).
Note: Avoid getting particles, dust or debris into clean oil once filled. Damage to pump could occur.
c) Dispose of hydraulic oil in accordance with the material safety datasheet.
* The following conditions would warrant more frequent hydraulic oil changes:
a) Very dusty environment where dust enters reservoir.
b) Hourly operations near 60°C (140°F), evidence of oxidation and formation of gum, sludge and/or varnish.
c) Exposure to frequent extreme temperature changes and high humidity resulting in excessive condensation in the reservoir
while in storage.