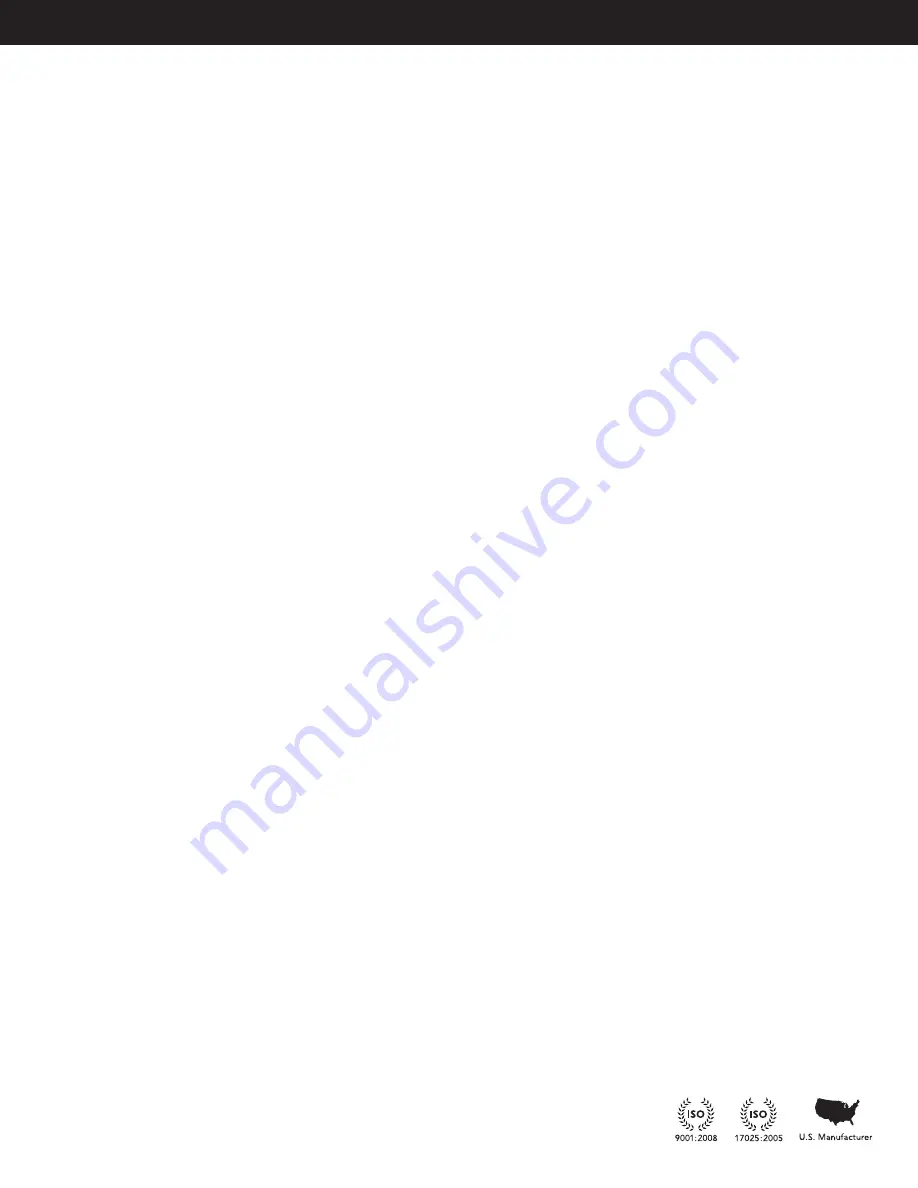
IHH500 Profile Setup Guide
2
CREATING A SENSOR PROFILE
1. Connect the sensor cable to the IHH500 sensor port and turn on the
IHH500 by pressing the POWER button in the lower right corner.
a.
During the power up of the IHH500 an internal auto calibration
will be performed.
b.
Next, a screen showing the current selected channel, serial
number, sensor type, and sensor sensitivity will briefly be
displayed.
c.
The normal operating screen will now be displayed with the
updated peak, tracking, valley, selected channel, gross/tare
mode, and sampling rate (samples per second).
2. Press the red MENU button to enter into the IHH500 main menu.
a.
The menu mode is controlled by the red arrow keys and red
command words.
3. Using the red Enter button select SENSOR PROFILE.
4. Using the red down arrow key followed by the red Enter button select
NEW CHANNEL.
5. Using the red left and right arrow keys followed by the red Enter
button set the number for the sensor channel to be created.
a.
Channel 01 is a calibrated reference channel, set in the IHH500 at
the factory, and cannot beoverwritten or selected during a sensor
profile setup.
6. Using the red Enter button select SENSOR CONFIGURATION.
a.
Each step in this menu must be completed before moving on to
the next step.
7. Using the red left and right arrow keys followed by the red Enter
button set the sensor type.
a.
Sensor type is usually listed on the sensor calibration certificate
by output and can be:
FULL BRIDGE for mV/V output sensors.
BRIDGE & PULSE for mV/V output sensors with encoder.
VOLTAGE OUTPUT for amplified voltage output sensors.
VOLTAGE & PULSE for amplified voltage output sensors with
encoder.
CURRENT OUTPUT for amplified current output sensors.
CURRENT & PULSE for amplified current output sensors with
encoder.
* For more information on sensor type see section 6.1.3.1 of the
IHH500 manual.
8. Using the red down arrow key followed by the red Enter button select
DIRECTION.
9. Using the red left and right arrow keys followed by the red Enter
button set the sensor direction type.
a.
UNI-DIRECTION is used for sensors with one direction of output
such as compression only.
b.
BI-DIRECTION is used for sensors with two directions of output
such as compression and tension.
*For more information on sensor direction see section 6.1.3.2 of
the IHH500 manual.
10. Using the red down arrow key followed by the red Enter button select
UNIT SELECTION.
11. Using the red up and down arrow keys followed by the red Enter
button select the type of output to be measured by the sensor.
12. Using the red left and right arrow keys followed by the red Enter
button select the engineering units to correspond with the measured
output of the sensor.
* For more information on selectable engineering units see section
6.1.3.3.1 of the IHH500 manual.
13. Using the red down arrow key followed by the red Enter button select
SENSOR CAPACITY.
14. Using the red left and red right arrow keys select the digit to be
changed. Using the red up and down arrow keys set the value for the
selected digit that corresponds to the sensors full capacity. Use the
red ENTER button to save the value.
a.
The decimal place can be set by first changing the decimal to a
number and then changing another selected digit into a decimal.
b.
The sensor’s full capacity is usually listed on the sensor calibration
certificate.
15. Setup SENSITIVITY (+)
a.
Using the red down arrow key followed by the red Enter button
select SENSITIVITY (+).
•
The sensitivity (+) will be the positive mV/V output for
bridge type sensors and the maximum positive voltage
output for amplified sensors.
•
The output of the sensor is usually listed on the sensor
calibration certificate.
•
For current output sensors, +/- Sensitivity is not available.
CALIBRATION must be used for current output sensors. See
step 19 below.
* For more information on sensitivity see section 6.1.3.5 of the
IHH500 manual.