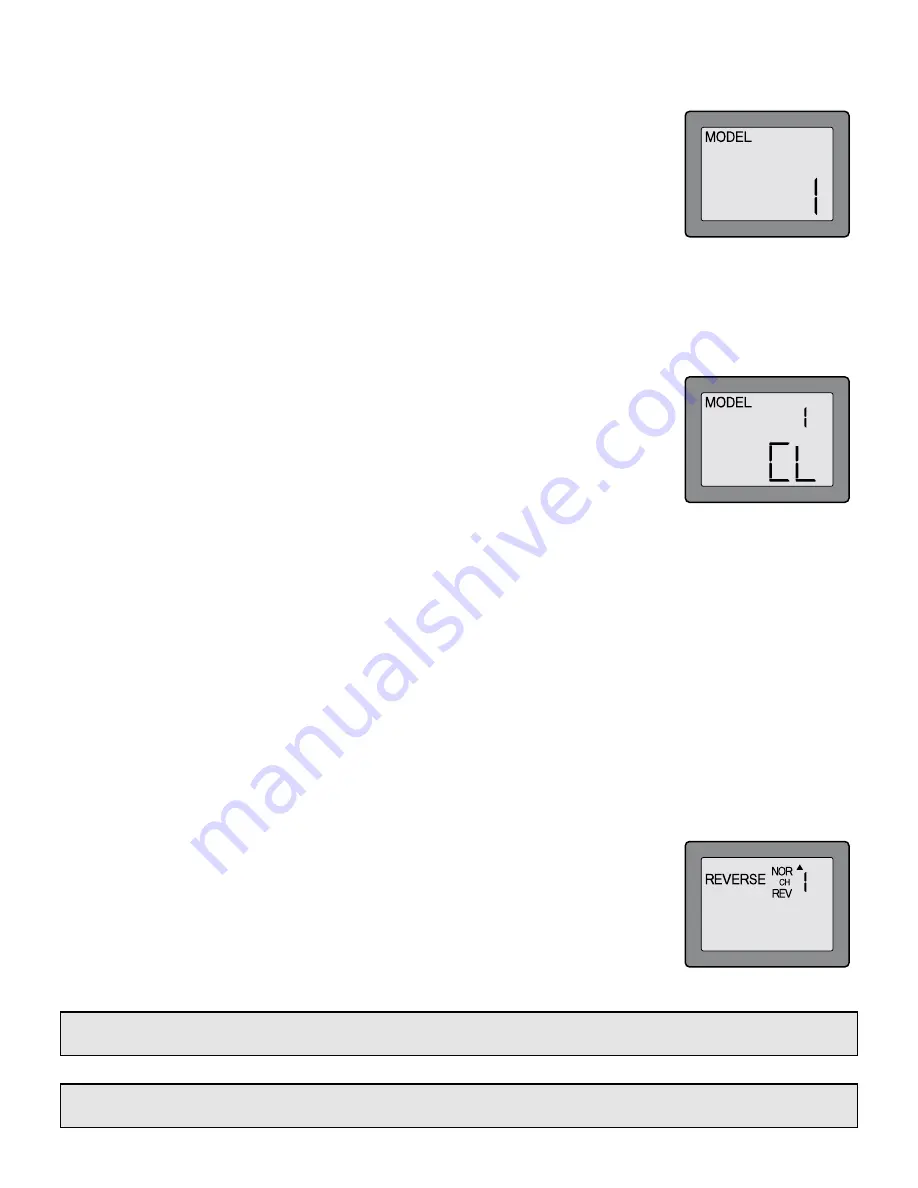
MODEL Model Select/Data Reset
Model select function
Access the Model Select function in the programming mode (by pressing the MODE and SELECT
keys simultaneously and holding them down for one second). The number for the current, active
model will be blinking. To activate a different model memory press the DATA INPUT lever until
the desired model number appears. Now the model has been selected. All programming inputs
from this point forward will affect only the model number on the screen (until another model
number is selected).
Data reset function
All the data for any model memory can be reset to the original, factory defaults. Often this function is done to get a fresh
start and clear the memory before inputting new model settings.
To reset data:
1. Access the Model Select function in the programming mode (by pressing the MODE and
SELECT keys simultaneously and holding them down for one second). Use the DATA INPUT
lever to select the model memory you wish to reset.
2. Once the desired model number is displayed on the screen, press the SELECT key. A CL will
appear on the screen.
3. Press the DATA INPUT up or down for two seconds to clear and reset the memory. Now the
data for this model has been reset to the original, factory defaults.
CAUTION:
Resetting the current model memory will permanently erase
ALL
programming
information for that model. The data cannot be recovered (unless you recorded it on a Model Data Recording Sheet in the back
of this manual). Do not reset the model unless
certain
you want to flush-out that memory and start from scratch.
When actually setting up a model you should have the model in front of you with the power on so you can actually see the
effects of your programming inputs and measure the control throws.
REVERSE Servo Reversing
The servo reversing function is used to change the direction that a servo responds to a control input from the transmitter
(stick, dial or switch). After using the reversing function, check
all
the controls on the model to
be certain
they are operating
in the correct direction and that you did not inadvertently reverse a servo other than the one intended. Reversing the wrong
servo (and not checking the response of the controls before each flight) may be the most common cause of a crash!
To reverse a servo:
1. Enter the programming mode and use the MODE key to access the REVERSE function.
2. Use the SELECT key to select the channel you wish to reverse. The active channel number will be displayed in the upper,
right corner of the screen.
3. Push the DATA INPUT lever down to reverse the servo (REV), or push the lever up to make
the servo operate normally (NOR). The arrow will indicate the condition of the servo (normal
or reversed). In the diagram channel 1 (aileron) is normal (
not reversed
).
4. Use the SELECT key to display other channels to be reversed.
D/R Dual Rates/Exponential Settings
The aileron and elevator dual rates on the 6EXA are simultaneously activated by the dual rate
switch. The amount of travel decrease for each control may be set between 0% and 100% of
the values set for the end points (explained in End Point Adjustment on page 11).
Note:
When performing initial model setup, the E.P.A.s should be set
prior to
setting the dual rates. When setting the
E.P.A.s for the first time on a new model, the dual rates should be set to 100%.
Note:
It is possible to set a dual rate value to zero, thus causing no response from that channel. If the dual rates are
inadvertently set to zero, a crash could result.
10