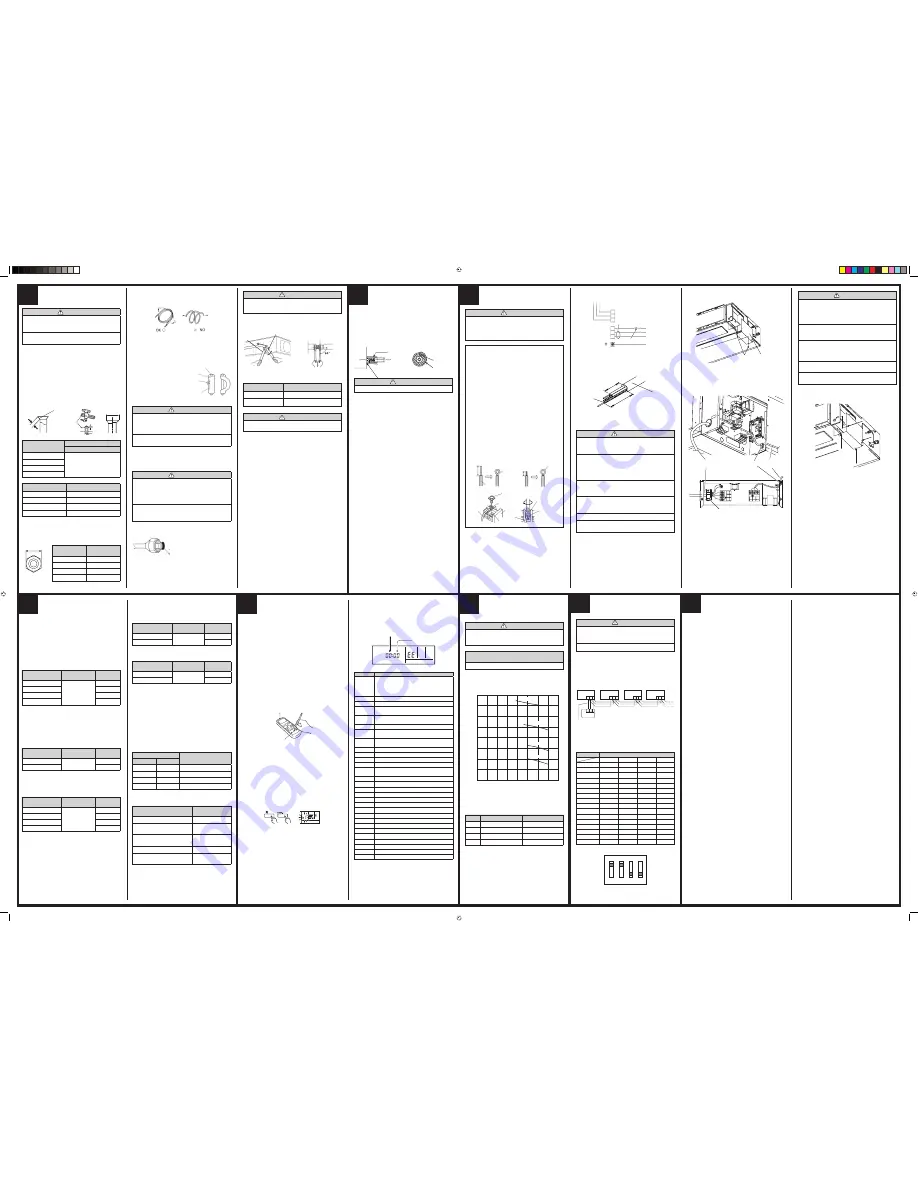
PART NO. 9374318148
500
600
700
800
900
1000
1100
1200
1300
0
20
40
60
80
100
120
140
160
AIR FLOW (m
3
/h)
EXTERNAL STATIC PRESSURE (Pa)
Mode
4
High
Mode
3
High
Mode
2
High
Mode
1
High
CAUTION
Do not bundle the remote controller cord, or wire
the remote controller cord in parallel, with the
indoor unit connection wire (to the outdoor unit)
and the power supply cord. It may cause errone-
ous operation.
3. CONNECTION PIPES
Indoor unit
(1) Detach the caps and plugs from the pipes.
CAUTION
1
To prevent breaking of the pipe, avoid sharp
bends.
Bend the pipe with a radius of curvature of 150
mm or over.
2
If the pipe is bent repeatedly at the same place,
it will break.
CAUTION
1
Do not use mineral oil on
fl
ared part. Prevent
mineral oil from getting into the system as this
would reduce the lifetime of the units.
2
While welding the pipes, be sure to blow dry
nitrogen gas through them.
Transmitter section
Test run button
CONNECTING THE
PIPE
When bending the pipe, do not
bend it as is. The pipe will be
collapsed. In this case, cut the
heat insulating pipe with a sharp
cutter as shown on the right, and
bend it after exposing the pipe.
After bending the pipe as you
want, be sure to put the heat
insulating pipe back on the pipe,
and secure it with tape.
Pipe
Heat insulating
Pipe
Cutter
Cut line
Flare nut tightening torque
2
Strip 25 mm
Loop
Insulation
Strip 10 mm
Round
terminal
Round
terminal
Screw with
special washer
Screw with
special washer
Round terminal
Wire
Wire
Terminal block
Terminal
board
B. Strand wire
A. Solid wire
ELECTRICAL WIRING
4
1. CONNECTION DIAGRAMS
3
2
1
3
2
1
Remote controller
Red
White
Black
Red
White
Black
Power line
Control line
Outdoor unit
Indoor unit
side terminal
2. BENDING PIPES
The pipes are shaped by your hands. Be careful not to collapse
them.
Extend the pipe
by unwinding it
Do not bend the pipes in an angle more than 90°.
When pipes are repeatedly bent or stretched , the material will
harden, making it dif
fi
cult to bend or stretch them any more. Do
not bend or stretch the pipes more than three times.
(1) Remove the control box cover and install each connection
wire.
Control box cover
Screw
(2) After wiring is complete, secure the remote controller cord,
connection cord, and power cord with the cord clamps.
Connection cord
(to outdoor unit)
Cord clamp
Remote
controller cord
Cord clamp
45 mm
7
5
3
INSTALLING THE
COUPLER HEAT
INSULATION
Body
Be sure to overlap the
insulation
Coupler heat insulation
No gap
Coupler heat
insulation
After checking for gas leaks, insulate by wrapping insulation
around the two parts (gas and liquid) of the indoor unit coupling,
using the coupler heat insulation.
After installing the coupler heat insulation, wrap both ends with
vinyl tape so that there is no gap.
3. CONNECTION OF WIRING
2. CONNECTION CORD PREPARATION
Keep the earth wire longer than the other wires.
Power supply cord
or connection cord
20
mm
50
mm
or
m
or
e
Earth wire
TEST RUN
6
STATIC PRESSURE
CHARACTERISTIC
2. AIR FLOW SETTING
The air
fl
ow is set according to the DIP switch settings in the
following tables.
1. FLARING
(1) Cut the connection pipe to the necessary length with a pipe
cutter.
(2) Hold the pipe downward so that cuttings will not enter the pipe
and remove the burrs.
(3) Insert the
fl
are nut (always use the
fl
are nut attached to the
indoor and outdoor units respectively) onto the pipe and
perform the
fl
are processing with a
fl
are tool.
Use the special R410A
fl
are tool, or the conventional
fl
are
tool.
Check if [L] is flared uniformly
and is not cracked or scratched
L
Die
A
Pipe
B
CAUTION
1
Be sure to apply the pipe against the port on the
indoor unit correctly. If the centering is improper,
the
fl
are nut cannot be tightened smoothly. If
the
fl
are nut is forced to turn, the threads will
be damaged.
2
Do not remove the
fl
are nut from the indoor unit
pipe until immediately before connecting the
connection pipe.
(2) Centering the pipe against port on the indoor unit, turn the
fl
are nut with your hand.
To prevent gas leakage, coat the flare
surface with alkylbenzene oil (HAB).
Do not use mineral oil.
When the
fl
are nut is tightened properly by your hand, use a torque
wrench to
fi
nally tighten it.
Holding
spanner
Torque wrench
Unit
side
CAUTION
Hold the torque wrench at its grip, keeping it in the
right angle with the pipe , in order to tighten the
fl
are nut correctly.
Flare nut
Tightening torque
6.35 mm (1/4 in.) dia.
14 to 18 N·m (140 to 180 kgf·cm)
15.88 mm (5/8 in.) dia.
63 to 77 N·m (630 to 770 kgf·cm)
CAUTION
Be sure to connect the gas pipe after connecting
the liquid pipe completely.
CAUTION
Must
fi
t tightly against body without any gap.
HOW TO CONNECT WIRING TO THE
TERMINALS
A. For solid core wiring
(1) Cut the wire end with a wire cutter or wire-cutting pliers,
then strip the insulation to about 25 mm (15/16”) to expose
the solid wire.
(2) Using a screwdriver, remove the terminal screw(s) on the
terminal board.
(3) Using pliers, bend the solid wire to form a loop suitable for
the terminal screw.
(4) Shape the loop wire properly, place it on the terminal
board and tighten securely with the terminal screw using
a screwdriver.
B. For strand wiring
(1) Cut the wire end with a wire cutter or wire-cutting pliers,
then strip the insulation to about 10 mm (3/8”) to expose
the strand wiring.
(2) Using a screwdriver, remove the terminal screw(s) on the
terminal board.
(3) Using a round terminal fastener or pliers, securely clamp
a round terminal to each stripped wire end.
(4) Position the round terminal wire, and replace and tighten
the terminal screw using a screwdriver.
WARNING
1
Before starting work, check that power is not
being supplied to the indoor unit and outdoor
unit.
2
Match the terminal board numbers and con-
nection cord colors with those of the outdoor
unit.
Erroneous wiring may cause burning of the
electric parts.
3
Connect the connection cords firmly to the
terminal board. Imperfect installation may
cause a
fi
re.
4
Always fasten the outside covering of the
connection cord with the cord clamp. (If the
insulator is chafed, electric leakage may occur.)
5
Always connect the ground wire.
6
Install the remote controller wires so as not to
be direct touched with your hand.
(3) Install control box cover.
Adjust the position of the screws for control box cover according
to the installation.
Pipe outside
diameter
Width across
fl
ats
of Flare nut
6.35 mm (1/4 in.)
17 mm
9.52 mm (3/8 in.)
22 mm
12.70 mm (1/2 in.)
26 mm
15.88 mm (5/8 in.)
29 mm
Pipe outside diameter
Dimension A (mm)
Flare tool for R410A, clutch type
6.35 mm (1/4 in.)
0 to 0.5
9.52 mm (3/8 in.)
12.70 mm (1/2 in.)
15.88 mm (5/8 in.)
Width across flats
When using conventional
fl
are tools to
fl
are R410A pipes, the
dimension A should be approximately 0.5 mm more than
indicated in the table (for
fl
aring with R410A
fl
are tools) to achieve
the speci
fi
ed
fl
aring. Use a thickness gauge to measure the
dimension A.
Pipe outside diameter
Dimension B (mm)
6.35 mm (1/4 in.)
9.1
9.52 mm (3/8 in.)
13.2
12.70 mm (1/2 in.)
16.6
15.88 mm (5/8 in.)
24.0
0
-0.4
CAUTION
1
Tighten the indoor unit connection cord (to the
outdoor unit) and power supply indoor and
outdoor unit terminal board connections
fi
rmly
with the terminal board screws. Faulty connec-
tion may cause a
fi
re.
2
If the indoor unit connection cord (to the outdoor
unit) and power supply are wired incorrectly, the
air conditioner may be damaged.
3
Wire the indoor unit connection cord (to the
outdoor unit) by matching the numbers of
the outdoor and indoor units terminal board
numbers as shown in terminal label.
4
Ground both the indoor and outdoor units by
attaching a ground wire.
5
Unit shall be grounded in compliance with the
applicable local and national codes.
RECOMMENDED RANGE OF
EXTERNAL STATIC PRESSURE
30Pa to 150Pa
Mode
Setting condition
Static pressure range
1
Normal
30
g
P
g
40
2
High static pressure 1
56
g
P
g
65
3
High static pressure 2
95
g
P
g
105
4
High static pressure 3
142
g
P
g
150
CAUTION
If the applicable static pressure does not match the
static pressure mode, the static pressure mode may
be changed to another mode automatically.
1. FAN PERFORMANCE AND AIR FLOW
EXTERNAL STATIC PRESSURE
CHECK ITEMS
(1) Is operation of each button on the remote control unit nor-
mal?
(2) Does each lamp light normally?
(3) Do not air
fl
ow direction louvers operate normally?
(4) Is the drain normal?
(5) Is there any abnormal noise and vibration during operation?
• Do not operate the air conditioner in the running state for a
long time.
• To end test operation, press the remote control unit START/
STOP button.
(When the air conditioner is run by pressing the test run button,
the OPERATION indicator lamp and TIMER indicator lamp will
simultaneously
fl
ash slowly.)
[Using the wired remote control]
• For the operation method, refer to the operating manual.
(1) Stop the air conditioner operation.
(2) Press the master control button and the fan control button
simultaneously for 2 seconds or more to start the test run.
Test run display
FAN
MODE
(3) Press the start/stop button to stop the test run.
[Troubleshooting at the remote control LCD]
This is possible only on the wired remote control.
[SELF-DIAGNOSIS]
If an error occurs, the following display will be shown.
(“EE” will appear in the set room temperature display.)
SU MO TU WE TH FR SA
Unit number
Error code
EX. Self-diagnosis
Error code
Error contents
01
13
26
27
Indoor signal error
00
Wired remote controller abnormal
02
Indoor room temperature sensor error
04
Indoor heat exchanger temperature sensor
(middle) error
28
Indoor heat exchanger temperature sensor
(inlet) error
09
Float switch operated
0C
Outdoor discharge pipe temperature sensor
error
06
Outdoor heat exchanger temperature sensor
(outlet) error
0A
Outdoor temperature sensor error
15
Compressor temperature sensor error
1d
2-way valve temperature sensor error
1E
3-way valve temperature sensor error
29
Outdoor heat exchanger temperature sensor
(middle) error
20
Indoor manual auto switch abnormal
2A
Power supply frequency detection error
17
IPM protection
18
CT error
1A
Compressor location error
1b
Outdoor fan error
1F
Connected indoor unit abnormal
1c
Outdoor unit computer communication error
12
Indoor fan abnormal
0F
Discharge temperature error
24
Exessive high pressure protection on cooling
2c
4-way valve abnormal
16
Pressure switch abnormal
2b
Compressor temperature error
19
Active
fi
lter abnormal
25
PFC circuit error
[Using the wireless remote control]
• For the operation method, refer to the operating manual.
• The outdoor unit may not operate depending on the room
temperature. In this case, press the test run button on the
remote control unit while the air conditioner is running. (Point
the transmitter section of the remote control unit toward the
air conditioner and press the test run button with the tip of a
ball-point pen, etc.)
If “CO” appears in the unit number display, there is a remote
controller error. Refer to the installation instruction sheet included
with the remote controller.
SPECIAL INSTALLATION
METHODS
8
CAUTION
1
When setting DIP switches, do not touch any
other parts on the circuit board directly with
your bare hands.
2
Be sure to turn off the main power.
GROUP CONTROL SYSTEM
A number of indoor units can be operated at the same time using
a single remote controller.
(1) Wiring method (indoor unit to remote controller)
1 2 3
1 2 3
1 2 3
1 2 3
1 2 3
Indoor unit
No.
0
Indoor unit
No.
1
Indoor unit
No.
2
Indoor unit
No.
3
Remote controller wire
Remote
controller
(2) DIP switch setting (Indoor unit)
Set the unit number of each indoor unit using DIP switch on the
indoor unit circuit board. (See following table and
fi
gure.)
DIP switch is normally set to make unit number No. 0.
Indoor unit
Unit number
DIP SWITCH No.
1
2
3
4
0
OFF
OFF
OFF
OFF
1
ON
OFF
OFF
OFF
2
OFF
ON
OFF
OFF
3
ON
ON
OFF
OFF
4
OFF
OFF
ON
OFF
5
ON
OFF
ON
OFF
6
OFF
ON
ON
OFF
7
ON
ON
ON
OFF
8
OFF
OFF
OFF
ON
9
ON
OFF
OFF
ON
10
OFF
ON
OFF
ON
11
ON
ON
OFF
ON
12
OFF
OFF
ON
ON
13
ON
OFF
ON
ON
14
OFF
ON
ON
ON
15
ON
ON
ON
ON
Example : No. 3
ON
1
2
3
4
CUSTOMER GUIDANCE
9
Explain the following to the customer in accordance with the
operating manual:
(1) Starting and stopping method, operation switching, tempera-
ture adjustment, timer, air
fl
ow switching, and other remote
control unit operations.
(2) Air filter removal and cleaning, and how to use the air
louvers.
(3) Give the operating and installation manuals to the customer.
(4) If the signal code is changed, explain to the customer how it
changed (the system returns to signal code A when the bat-
teries in the remote control unit are replaced).
*(4) is applicable to using wireless remote control.
FUNCTION SETTING
Setting
Setting Value
Static pressure
Cooler room temperature
correction
Heater room temperature
correction
Auto restart
Indoor room temperature sensor
switching function
• Follow the instructions in the Local Setup Procedure, which is
supplied with the remote control, in accordance with the installed
condition. After the power is turned on, perform the Function
Setting on the remote control.
• The settings may be selected between the following two: Func-
tion Number or Setting Value.
• Settings will not be changed if invalid numbers or setting values
are selected.
Setting the Static Pressure
Determine the wind volume in each mode i.e., applicable
range of static pressure, refering to [7] STATIC PRESSURE
CHARACTERISTICS. (The unit is factory-set to “00”)
Setting the Cooler Room Temperature Correction
• Depending on the installed environment, the room temperature
sensor may require a correction. The settings may be selected
as shown in the table below. (The unit is factory-set to “00”.)
Setting the Heater Room Temperature Correction
• Depending on the installed environment, the room temperature
sensor may require a correction. The settings may be changed
as shown in the table below. (The unit is factory-set to “00”.)
Setting Other Functions
• The following settings are also possible, depending on the
operating conditions. (The unit is factory-set to “00”.)
Auto Restart
Indoor Room Temperature Sensor Switching Function (Wired
remote controller only)
• If setting value is “00”, room temperature is controlled by the
indoor unit temperature sensor.
• If setting value is “01”, room temperature is controlled by either
indoor unit temperature sensor or remote control unit sensor.
[When using the wireless remote controller]
SWITCHING REMOTE CONTROL UNIT
SIGNAL CODES
• Con
fi
rm the setting of the remote control unit signal code and
the printed circuit board setting.
If these are not con
fi
rmed, the remote control unit cannot be
used to operate for the air conditioner.
Setting Record
• Record any changes to the settings in the following table.
Jumper wire
Remote control unit
signal code
JM1
JM2
Connect
Connect
A (Primary setting)
Disconnect
Connect
b
Connect
Disconnect
c
Disconnect
Disconnect
d
Setting Description
Function Number
Setting Value
Yes
40
00
No
01
Setting Description
Function Number
Setting Value
Standard
31
00
Lower control
01
Slightly warmer control
02
Warmer control
03
Setting Description
Function Number
Setting Value
Standard
30
00
Lower control
01
Setting Description
Function Number
Setting Value
Normal
21
00
High static pressure 1
01
High static pressure 2
02
High static pressure 3
03
Setting Description
Function Number
Setting Value
No
42
00
Yes
01
After completing the FUNCTION SETTING, be sure to turn off
the power and turn it on again.
9374318148_B2back.indd 1
9374318148_B2back.indd 1
8/23/06 4:43:04 PM
8/23/06 4:43:04 PM
Содержание AO*A12LACL series
Страница 4: ...1 SPECIFICATIONS R410A DUCT type INVERTER ...
Страница 12: ...2 DIMENSIONS R410A DUCT type INVERTER ...
Страница 17: ...3 REFRIGERANT SYSTEM DIAGRAM R410A DUCT type INVERTER ...
Страница 22: ...4 CIRCUIT DIAGRAM R410A DUCT type INVERTER ...
Страница 23: ...04 01 4 CIRCUIT DIAGRAM MODEL AR A12 14 18LATN ...
Страница 24: ...04 02 MODEL AR A24 36 45LATN COIL ...
Страница 25: ...04 03 MODEL AO A12 14 18 24LACL ...
Страница 26: ...04 04 MODEL AO A36 45LATL ...
Страница 27: ...5 DESCRIPTION OF EACH CONTROL OPERATION R410A DUCT type INVERTER ...
Страница 50: ...6 REFRIGERANT CAUTION R410A R410A INVERTER DUCT type ...
Страница 59: ...7 TROUBLE SHOOTING R410A DUCT type INVERTER ...
Страница 98: ...8 APPENDING DATA R410A INVERTER DUCT type ...
Страница 114: ...9 INSTALLATION MANUAL R410A DUCT type INVERTER ...
Страница 133: ...1116 Suenaga Takatsu ku Kawasaki 213 8502 Japan June 2007 Printed in Japan ...