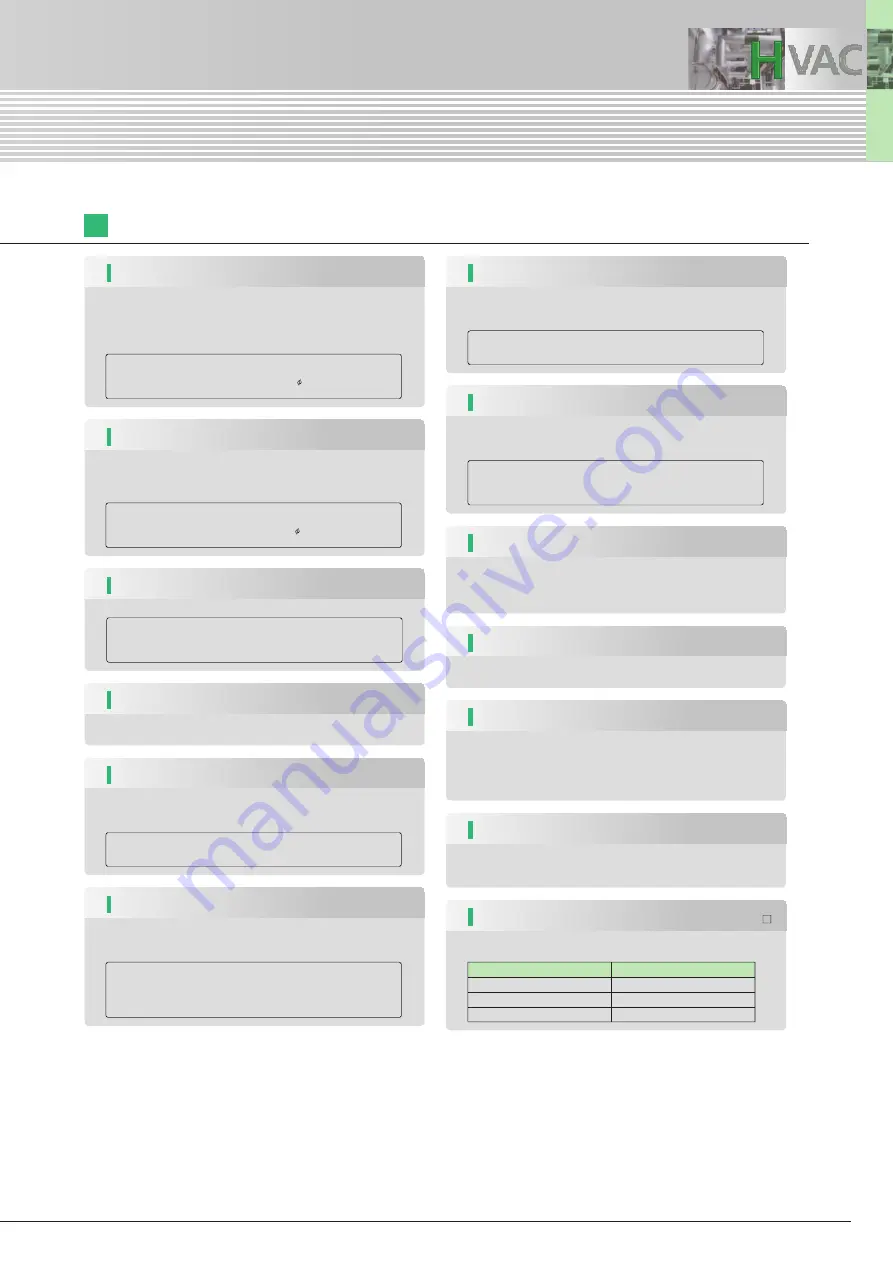
22
23
Options
Relay output interface card
(OPC-RY)
This is an optional card that converts the transistor output at
terminals Y1 to Y4 on the inverter body to relay output (1c). Each
card has two relay outputs, and four relay outputs are available by
installing two cards.
Relay output:
Signal type:
Contact point capacity:
2 circuits built-in
1c
AC250V, 0.3A cos =0.
DC48V, 0.5A (Resistance load)
No. of connection nodes:
MAC ID:
Insulation:
Communications rate:
Network consumed power:
max. 64 units (including the master unit)
0~63
500V DC (photocoupler insulation)
500kbps/250kbps/125kbps
max. 80mA, 24V DC
Optional type
CB-5S
CB-3S
CB-1S
Length (m)
5
3
1
Relay output interface card
(OPC-RY2)
This optional card allows relay outputs (1a) to be added. When used
in cascaded control, this card can control the seven motors.
Relay output:
Signal type:
Contact point capacity:
7 circuits built-in
1a
AC250V, 0.3A cos =0.
DC48V, 0.5A (Resistance load)
No. of connection units:
Communications method:
Communications rate:
42 units
CC-Link Ver1.10 and Ver2.0
156kbps~
Analog input interface card
(OPC-AIO)
This card allows analog input and output to be used.
Analog input:
Analog output:
1 analog voltage input point (0~±10V)
1 analog current input point (4~20mA)
1 analog voltage output point (0~±10V)
1 analog current output point (4~20mA)
Analog current output interface card
(OPC-AO)
This card allows two analog current output (4 to 20mA) points to be used.
The card cannot be used together with OPC-G1-AIO.
CC-Link communications card
(OPC-CCL)
By connecting this card with the CC-Link master unit, the communications
rate up to 10Mbps can be supported and the transmission distance is
covered up to 1200 m in total.
DeviceNet communications card
(OPC-DEV)
This card enables operation instruction and frequency command to be
set from the DeviceNet master, allowing operation conditions to be
monitored and all the function codes to be changed and checked.
PROFIBUS DP communications card
(OPC-PDP2)
This card enables operation instruction and frequency command to be
set from the PROFIBUS DP master, allowing operation conditions to be
monitored and all the function codes to be changed and checked.
Communications rate:
Transmission distance:
Connection connector:
9.6kbps~12Mbps
~1,200m
2×6-pole terminal block
CANopen communications card
(OPC-COP)
This card enables operation instruction and frequency command to
be set from the CANopen master (such as PC and PLC), allowing all
the function codes to be set and checked.
No. of connection nodes:
Communications rate:
Transmission distance:
127 units
20k, 50k, 125k, 250k, 500k,
800k, 1Mbps
~2,500m
Extension cable for remote operation
(CB-
S)
This cable is used in connection between the inverter body and the
keypad.
LonWorks communications card
(OPC-LNW)
This card allows peripheral equipment (including a master unit) that
is connected via LonWorks to be connected with the inverter,
enabling operation instruction and frequency command to be set
from the master unit.
Battery
(OPK-BP)
Used for the real time clock activated while the inverter power is off.
The real time clock can be operated even when no power is supplied
inverter at electric power interruption.
Ethernet communications card
(OPC-ETH)
Pt100 temperature sensor input card
(OPC-PT)
This is an interface card for connecting FRENIC-HVAC with
peripherals (such as a master) via Ethernet.
This card can connect FRENIC-HVAC with a mountable two-channel
resistance temperature detector (hereinafter-called RTD) to convert
temperature values into digital values.
The following five types of mountable RTU are supported: JPt100,
Pt100, Ni100, Pt1000, and Ni1000.
*1 Install a recommended molded case circuit breaker (MCCB) or residual-current-operated protective device (RCD)/earth
leakage circuit breaker (ELCB) (with overcurrent protection function) in the primary circuit of the inverter to protect wiring.
Ensure that the circuit breaker capacity is equivalent to or lower than the recommended capacity.
*2 Install a magnetic contactor (MC) for each inverter to separate the inverter from the power supply, apart from the MCCB
or RCD/ELCB, when necessary.
Connect a surge absorber in parallel when installing a coil such as the MC or solenoid near the inverter.
*3 To retain an alarm output signal ALM issued on inverter's programmable output terminals by the protective function or to
keep the keypad alive even if the main power has shut down, connect these terminals to the power supply lines. Even
without power supply to these terminals, the inverter can run.
*4 A grounding terminal for a motor. Use this terminal if needed.
*5 For control signal wires, use twisted or shielded-twisted wires. When using shielded-twisted wires, connect the shield of
them to the common terminals of the control circuit. To prevent malfunction due to noise, keep the control circuit wiring
away from the main circuit wiring as far as possible (recommended: 10 cm or more). Never install them in the same wire
duct. When crossing the control circuit wiring with the main circuit wiring, set them at right angles.
*6 The connection diagram shows factory default functions assigned to digital input terminals [X1] to [X7], [FWD] and [REV],
transistor output terminals [Y1] to [Y4], and relay contact output terminals [Y5A/C] and [30A/B/C].
*7 Terminals [Y1] to [Y4] (transistor outputs) support both SINK and SOURCE modes. The diagrams below show the
examples of circuit connection between the transistor output of the inverter's control circuit and a PLC.
*8 Slide switches on the control printed circuit board (control PCB). Use these switches to customize the inverter operations.
For details, refer to the FRENIC-HVAC Instruction Manual (INR-SI47-1610-E), Chapter 2, Section 2.3.2 "Setting up the
slide switches."
*9 When the Enable function is not to be used, short-circuit terminals [EN1] and [PLC] and terminals [EN2] and [PLC] using
jumper wires. For opening and closing the hardware circuit between terminals [EN1] and [PLC] and between [EN2] and
[PLC], use safety components such as safety relays and safety switches. Be sure to use shielded wires exclusive to
terminals [EN1] and [PLC] and terminals [EN2] and [PLC]. (Do not put them together with any other control signal wire in
the same shielded core.)
*10 Usually there is no need to do anything for the EMC filter.
When the leakage current from the connected EMC filter causes problems with the power supply system, removing
screws from terminals [E1] and [E2] could improve the problem. Note that doing so loses the effect of the EMC filter so
that the inverter is no longer compliant with the EMC standards. To remove those screws, consult your Fuji Electric
representative.
*11 Usually there is no need to do anything for these terminals. To be used when the inverter is combined with a power
regenerative PWM converter (RHC series).
*12 Main circuit switching connectors. For details, refer to the FRENIC-HVAC Instruction Manual (INR-SI47-1610-E), Chapter
2, Section 2.2.3 "Switching connectors."
(a) PLC serving as SINK
(b) PLC serving as SOURCE
SOURCE input
CO
+24VDC
[Y1]
[Y4]
to
31 to
35V
[CMY]
Current
<Control circuit>
SINK input
31 to
35V
[Y1]
[Y4]
[CMY]
CO
+24VDC
to
Current
Photocoupler
<Control circuit>
Photocoupler
Programmable
logic controller
Programmable
logic controller
Wiring Diagram
Note: When the card is mounted, the terminals Y1 to Y4 on the inverter body cannot be used.
* By using the two relay outputs on the inverter body, max. 8 units and one unit
(auxiliary pump) can be controlled.