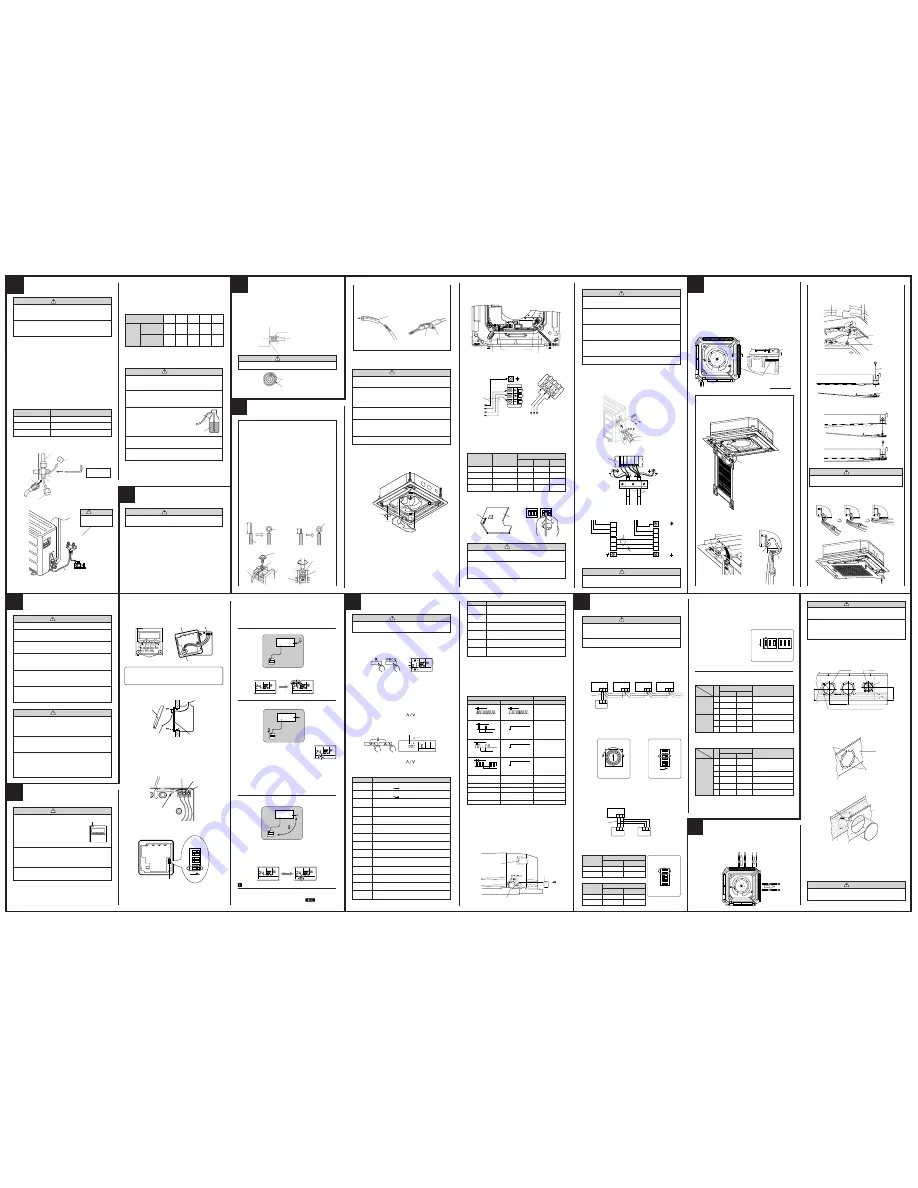
7
GRILLE INSTALLATION
BLOWER COVER INSULATION
Install the blower cover insulation only when the outlet direction is not
specified.
Two blower cover insulations are packed with the indoor unit.
Install the blower cover insulation at the diffuser position shown in Fig. 38.
At this time, use the piping position as the criteria.
Fig. 38
A-A Section view
A
A
INSTALLING THE INTAKE GRILLE
(1) Mount the grille hinge wire to the hook shaft as shown in Fig. 39.
Fig. 39
A
•
Latch the grille hinge wire to the hook shaft, and fasten.
Fig. 40 Part A detail view
Fig. 41 Part A section view
Grille hinge
wire
(2) Install the hook wire.
•
Pass the hook wire through the panel base from the rear side as
shown in Fig. 42, and fasten to the reinforced metal fitting of the
intake grille using a screw.
Fig. 42
Screw
Fig. 43 Section view
2 direction example
(Piping direction)
Blower cover
insulation
Panel
base
Drain
pan
Hook shaft
Hook wire
RFM (grille)
(3) Loosen the screw, put the loop of the hook wire over it, and tighten
the screw again.
CAUTION
Install the intake grille hook wire to the grille assem-
bly. If it falls, it may cause injuries.
(4) Bring up the intake grille by pushing it up at an angle as shown in
Figs. 44, 45, and fasten.
Fig. 44
Fig. 45
Hook wire
(1) Remove the control box cover and cover (wire) B and install the con-
nection cord.
Fig. 33
Remote controller cord
Terminal board
(Indoor unit)
Ceiling height
(m)
Normal
High ceiling 1
High ceiling 2
Low ceiling
1
–
–
–
–
2.5 - 3.0
3.0 - 3.5
More than 3.5
Less than 2.5
2
OFF
ON
OFF
ON
3
OFF
OFF
ON
ON
DIP-SW4
Gas
Liquid
5
VACUUM PROCESS
CAUTION
1
Do not purge the air with refrigerants but use a vacuum
pump to vacuum the installation! There is no extra re-
frigerant in the outdoor unit for air purging!
2
Use a vacuum pump for R410A exclusively. Using the
same vacuum pump for different refrigerants may dam-
age the vacuum pump or the unit.
1. VACUUM
(1) Remove the cap, and connect the gauge manifold and the vacuum
pump to the charging valve by the service hoses.
(2) Vacuum the indoor unit and the connecting pipes until the pressure
gauge indicates –0.1 MPa (–76 cmHg).
(3) When –0.1 MPa (–76 cmHg) is reached, operate the vacuum pump
for at least 15 minutes.
(4) Disconnect the service hoses and fit the cap to the charging valve to
the specified torque.
(5) Remove the blank caps, and fully open the spindles of the 2-way and
3-way valves with a hexagon wrench (Torque : 6 to 7 N · m (60 to 70
kgf·cm).
(6) Tighten the blank caps of the 2-way valve and 3-way valve to the
specified torque.
Table 6
Fig. 29
Connecting pipe
Blank cap
Hexagon wrench
3-way valve
Charging port
Cap
Service hose
with valve core
Outdoor unit
CAUTION
Use a clean gauge mani-
fold and charging hose
for R410A exclusively.
t
2. ADDITIONAL CHARGE
Refrigerant suitable for a piping length of 7.5 m is charged in the outdoor
unit at the factory.
When the piping is longer than 7.5 m, additional charging is necessary.
For the additional amount, see the table below.
Table 7
Between 7.5 m and 25 m, when using a connection pipe other than that
in the table, charge additional refrigerant with 40 g (1.4 oz)/1 m (3.3 ft)
(Reverse cycle model), 20 g (0.71 oz)/1 m (3.3 ft) (Cooling model) as the
criteria.
CAUTION
1
When moving and installing the air conditioner, do not
mix gas other than the specified refrigerant (R410A)
inside the refrigerant cycle.
2
When charging the refrigerant R410A, always use an
electronic balance for refrigerant charging (to meas-
ure the refrigerant by weight).
3
When charging the refrigerant, take
into account the slight change in
the composition of the gas and liq-
uid phases, and always charge from
the liquid phase side whose com-
position is stable.
4
Add refrigerant from the charging valve after the com-
pletion of the work.
5
If the units are further apart than the maximum pipe
length, correct operation can not be guaranteed.
GAS LEAKAGE INSPECTION
CAUTION
After connecting the piping, check the joints for gas leak-
age with gas leak detector.
Blank cap (2-way valve)
Blank cap (3-way valve)
Charging port cap
Tightening torque
20 to 25 N·m (200 to 250 kgf·cm)
30 to 35 N·m (300 to 350 kgf·cm)
10 to 12 N·m (100 to 120 kgf·cm)
Use a 4 mm
hexagon wrench.
Gauge manifold
Vacuum pump
Service hose
R410A
Cooling
model
7.5 m
(25 ft)
None
None
Pipe length
10 m
(33 ft)
100 g
(3.5 oz)
50 g
(1.8 oz)
15 m
(49 ft)
300 g
(10.6 oz)
150 g
(5.3 oz)
20 m
(66 ft)
500 g
(17.6 oz)
250 g
(8.8 oz)
Additional
refrigerant
Heat & Cool
(Reverse cycle)
25 m
(82 ft)
700 g
(24.7 oz)
350 g
(12.3 oz)
LO
HI
6
8
ELECTRICAL WIRING
HOW TO CONNECT WIRING TO THE TERMINALS
A. For solid core wiring (or F-cable)
(1) Cut the wire end with a wire cutter or wire-cutting pliers, then strip
the insulation to about 25 mm (15/16”) of expose the solid wire.
(2) Using a screwdriver, remove the terminal screw(s) on the terminal
board.
(3) Using pliers, bend the solid wire to form a loop suitable for the
terminal screw.
(4) Shape the loop wire properly, place it on the terminal board and
tighten securely with the terminal screw using a screwdriver.
B. For strand wiring
(1) Cut the wire end with a wire cutter or wire-cutting pliers, then strip
the insulation to about 10 mm (3/8”) of expose the strand wiring.
(2) Using a screwdriver, remove the terminal screw(s) on the terminal
board.
(3) Using a round terminal fastener or pliers, securely clamp a round
terminal to each stripped wire end.
(4) Position the round terminal wire, and replace and tighten the ter-
minal screw using a screwdriver.
Fig. 31
A. Solid wire
Str
ip 25 mm (15/16”)
Insulation
Loop
B. Strand wire
Str
ip 10 mm (3/8”)
Round
terminal
Wire
Screw with
special washer
Round terminal
Terminal
board
Wire
Screw with
special washer
Round
terminal
HOW TO FIXED CONNECTION CORD AND
POWER CORD AT THE CORD CLAMP
After passing the connection cord and power cord through the insula-
tion tube, fasten it with the cord clamp.
Fig. 32
Insulation tube
Insulation tube
Cord clamp
Use VW-1, 0.5 to 1.0 mm thick, PVC tube as the insulation tube.
1. INDOOR UNIT SIDE
WARNING
1
Before starting work, check that power is not being sup-
plied to the indoor unit and outdoor unit.
2
Match the terminal board numbers and connection cord
colors with those of the outdoor unit.
Erroneous wiring may cause burning of the electric
parts.
3
Connect the connection cord firmly to the terminal
board. Imperfect installation may cause a fire.
4
Always fasten the outside covering of the connection
cord with the cord clamp. (If the insulator is chafed,
electric leakage may occur.)
5
Always connect the ground wire.
Body
Be sure to overlap the
insulation
Coupler heat insulation
No gap
Coupler heat insulation
INSTALLING THE COUPLER
HEAT INSULATION
After checking for gas leaks, insulate by wrapping insulation around the
two parts (large and small) of the indoor unit coupling, using the coupler
heat insulation.
After installing the coupler heat insulation, wrap both ends with vinyl tape
so that there is no gap.
Fig. 30
CAUTION
Must fit tightly against body without any gap.
(2) After wiring is complete, clamp the remote controller cord and con-
nection cord with the cord clamp.
(3) Install the control box cover and cover (wire) B.
Fig. 34
Cover (wire) B
Control box cover
Cord clamp
Connection cord
(To the outdoor unit)
Fig. 35
Red
White
Black
Ceiling height setting
Set the DIP switch for the ceiling height according to the table below.
Table 8
CAUTION
1
If the setting for a low ceiling is selected, the capacity
of the air conditioner decreases slightly.
2
Do not set any switches other than those specified in
this sheet. The air conditioner may not operate correctly
if any switches other than those specified are changed.
Remote
controller
Terminal board
OUTDOOR
UNIT
Connection
cord
2. OUTDOOR UNIT SIDE
WARNING
1
Before starting work, check that power is not being
supplied to the indoor unit and outdoor unit.
2
Match the terminal board numbers and connection cord
colors with those of the indoor unit side.
Erroneous wiring may cause burning of the electric parts.
3
Connect the connection cords and the power supply
cord firmly to the terminal board. Imperfect installation
may cause a fire.
4
Always fasten the outside covering of the connection
cord and the power supply cord with cord clamps. (If
the insulator is chafed, electric leakage may occur.)
5
Always connect the ground wire.
(1) Remove the terminal cover of the outdoor unit, and insert the end of
the connection cord and the power supply cord into the terminal board.
(2) Fasten the connection cord and the power supply cord with the cord
clamp, and install the terminal cover.
Fig. 37
Power supply
Remote controller
Black
White
Red
Outdoor unit
side terminal
Indoor unit
side terminal
Power line
Control line
EARTH
N
L
3 2
(N)
1
Connection cord
Terminal board
Cord clamp
Power supply cord
Insulation tube
Connection
cord
Power supply
cord
Cord clamp
Insulation tube
L
N
3
1
3
2
(N)
2
(N)
1
3
2
1
EARTH
Terminal
cover
45 mm
45 mm
CAUTION
When routing the ground wires, leave slack as shown in
the illustrations.
9
10
POWER
WARNING
1
The rated voltage of this product is 230 V A.C. 50 Hz.
2
Before turning on verify that the voltage is within the
198 V to 264 V range.
3
Always use a special branch circuit and install a spe-
cial receptacle to supply power to the air conditioner.
4
Use a special branch circuit breaker and receptacle
matched to the capacity of the air conditioner.
(Install in accordance with standard.)
5
Perform wiring work in accordance with standards so
that the air conditioner can be operated safely and posi-
tively.
6
Install a leakage special branch circuit breaker in ac-
cordance with the related laws and regulations and elec-
tric company standards.
CAUTION
1
The power source capacity must be the sum of the air
conditioner current and the current of other electrical
appliances. When the current contracted capacity is in-
sufficient, change the contracted capacity.
2
When the voltage is low and the air conditioner is diffi-
cult to start, contact the power company the voltage
raised.
3
This air conditioner must be connected to a power
source that has an electrical impedance of 0.159
Ω
or
less or has a supply current of 100 A or greater. If the
power supply does not meet the specifications, con-
tact the power company.
ON
ON
OFF
1
2
3
4
5
6
1. INSTALLING THE REMOTE CONTROLLER
(1) Open the operation panel on the front of the remote controller, re-
move the two screws indicated in the following figure, and then re-
move the front case of the remote controller.
Fig. 46
Front case
(back side)
Rear case
Connector
Remote
controller wires
Rear case
Connector
Front case
1. Red
2. White
3. Black
Binder
3. SETTING THE DIP SWITCHES
When using a battery (memory backup)
Fig. 49
Change the DIP switch setting to use batteries. (The DIP switch is not set
to use batteries at the factory.)
Change DIP switch No. 6 from OFF to ON.
If batteries are not used, all of the settings stored in memory will be de-
leted if there is a power failure.
DIP Switch
Screws
2. ROUTING THE REMOTE CONTROLLER WIRES
(1) Install the remote controller wires to the terminals on the top of the
rear case as shown in the following figure.
(2) Fasten the wires with the binder.
(3) If the remote controller wires run through the room, use a tool to cut
away the thin area on the upper center of the front case.
Fig. 48
(Example)
11
REMOTE CONTROLLER
SETTING
CAUTION
1
In order to detect the room temperature
correctly when using the temperature
sensor of the remote controller, do not
install the remote controller in a place
where it will be exposed to direct sun-
light or directly below the air outlet of
the indoor unit.
2
When installing the remote controller and cord near a
source of electromagnetic waves, separate the remote
controller from the source of the electromagnetic waves
and use shielded cord.
3
Do not touch the remote controller PC board and PC
board parts directly with your hands.
Temperature sensor
When installing the remote controller, remove the connector from the
front case. The wires may break if the connector is not removed and
the front case hangs down.
When installing the front case, connect the connector to the front case.
(2) Install the rear case to the wall, etc. with the two tapping screws.
Refer to the following information to install the remote controller wires.
Fig. 47
SU MO TU WE TH FR SA
4. SETTING THE ROOM TEMPERATURE DETEC-
TION LOCATION
The detection location of the room temperature can be selected from the
following three examples. Choose the detection location that is best for
the installation location.
A. Indoor unit setting (factory setting)
The room temperature is detected by the indoor unit temperature sensor.
A
B. Remote controller setting
The room temperature is detected by the remote controller temperature
sensor.
B
C
Indoor unit
(1) When the THERMO SENSOR button is pressed, the lock display
flashes because the function is locked at the factory.
Fig. 50
(1) Press the THERMO SENSOR button for 5
seconds or more to unlock the function. The
thermo sensor display flashes and then dis-
appears when the function is unlocked.
(2) Press the THERMO SENSOR button. The thermo sensor display ap-
pears.
(3) Press the THERMO SENSOR button again for 5 seconds or more to
lock the function. The thermo sensor display flashes and then remains
on when the function is locked.
(4) Make sure that the function is locked.
C. Indoor unit/remote controller setting
(room temperature sensor selection)
The temperature sensor of the indoor unit or the remote controller can be
used to detect the room temperature.
12
TEST RUN
CAUTION
Supply power to the crankcase heater for at least 12 hours
before the start of operation in winter.
(1) Stop the air conditioner operation.
(2) Press the master control button and the fan control button simultane-
ously for 2 seconds or more to start the test run.
Fig. 53
Unit number (usually 0)
Error code
(3) Press the start/stop button to stop the test run.
[SELF-DIAGNOSIS]
When the error indication “E:EE” is displayed, follow the following items to
perform the self-diagnosis. “E:EE” indicates an error has occurred.
1. REMOTE CONTROLLER DISPLAY
(1) Stop the air conditioner operation.
(2) Press the set temperature buttons
simultaneously for 5 sec-
onds or more to start the self-diagnosis.
Refer to the following tables for the description of each error code.
Fig. 54
Test run display
(3) Press the set temperature buttons
simultaneously for 5 sec-
onds or more to stop the self-diagnosis.
Table 9
Ex. Self-diagnosis
Error code
Error contents
Communication error
(indoor unit
remote controller)
Communication error
(indoor unit
outdoor unit)
Room temperature sensor open
Room temperature sensor short-circuited
Indoor heat exchanger temperature sensor open
Indoor heat exchanger temperature sensor short-
circuited
Outdoor heat exchanger temperature sensor open
Outdoor heat exchanger temperature sensor short-
circuited
Power source connection error
Float switch operated
Outdoor temperature sensor open
Outdoor temperature sensor short-circuited
Discharge pipe temperature sensor open
Discharge pipe temperature sensor short-circuited
00
01
02
03
04
05
06
07
08
09
0A
0b
0c
0d
Indoor unit No.
0
Indoor unit No.
1
Indoor unit No.
2
Indoor unit No.
3
Remote
controller
wire
Remote
controller
(2) Rotary switch setting (indoor unit)
Set the unit number of each indoor unit using the rotary switch on the
indoor unit circuit board.
The rotary switch is normally set to 0.
(3) DIP switch setting (remote controller)
Change DIP switch No. 3 on the remote controller from OFF to ON.
Indoor unit
Rotary Switch
Remote controller
DIP Switch
2. DUAL REMOTE CONTROLLERS (OPTIONAL)
Two separate remote controllers can be used to operate the indoor units.
(1) Wiring method (indoor unit to remote controller)
Fig. 59
(2) DIP switch setting (remote controller)
Set the remote controller DIP switch Nos. 1 and 2 according to the
following table.
Number of
remote
controllers
Master unit
1 (Normal)
2 (Dual)
ON
OFF
OFF
OFF
DIP-SW No. 1 DIP-SW No. 2
Remote controller
DIP Switch
Number of
remote
controllers
Slave unit
1 (Normal)
2 (Dual)
–
ON
–
ON
DIP-SW No. 1 DIP-SW No. 2
SW3
Table 11
Table 12
Fig. 60
2. OUTDOOR UNIT LEDS
Heat & Cool model (reverse cycle) only
When a malfunction occurs in the outdoor unit, the LEDs on the circuit
board light to indicate the error. Refer to the following table for the descrip-
tion of each error according to the LEDs.
Table 10
When the fault is cleared, the LED lamp goes off.
However, for discharge pipe temperature abnormal and high pressure
abnormal, the LED lamp lights continuously for 24 hours, as long as the
power is not turned off.
Quick flash continued
Quick flash continued
Model abnormal or
EEPROM abnormal
1 quick flash repeated
Lighting continued
Power source
connection error
2 quick flash repeated
Lighting continued
Discharge tempera-
ture sensor error
3 quick flash repeated
Lighting continued
Outdoor heat
exchanger tempera-
ture sensor error
4 quick flash repeated Lighting continued
Outdoor temperature
sensor error
5 quick flash repeated Lighting continued
Communication signal error
6 quick flash repeated Lighting continued
Indoor unit error
7 quick flash repeated Lighting continued
Discharge temperature
abnormal
8 quick flash repeated Lighting continued
High pressure abnormal
Error display
LED1
LED2
Error contents
Error code
Error contents
Outdoor high pressure abnormal
Discharge pipe temperature abnormal
Model abnormal
Indoor fan abnormal
Outdoor signal abnormal
Outdoor EEPROM abnormal
0E
0F
11
12
13
14
0.1 sec.
OFF
ON
0.1 sec.
OFF
ON
0.5 sec.
2 sec.
OFF
ON
OFF
ON
0.5 sec.
2 sec.
OFF
ON
OFF
ON
0.5 sec.
2 sec.
OFF
ON
OFF
ON
1 2 3
1 2 3
1 2 3
ON
OFF
1
2
3
4
5
6
ON
1 2 3
1 2 3
1 2 3
1 2 3
1 2 3
ON
OFF
1
2
3
4
5
6
NO.
SW state
Detail
OFF
ON
1
✽
Dual remote controller
2
✽
setting
3
One unit
✽
Multiple unit
Group control setting
4
Heat & Cool model Cooling only model
Model setting
5
Invalidity
Validity
✽
Auto changeover setting
6
Invalidity
✽
Validity
Memory backup setting
NO.
SW state
Detail
OFF
ON
1
Invalidity
Validity
✽
Auto restart setting
2
—
—
✽
Temperature correction
3
—
—
✽
setting for heating
1
—
—
Remote controller setting
2
—
✽
—
Air flow setting
3
—
✽
—
DIP-Switch 1
●
Indoor unit
Table 13
●
Remote controller
Table 14
[DIP-SWITCH SETTING]
DIP-Switch 4
DIP-Switch
✽
: Factory setting
OPENING THE DUCT
CONNECTION HOLE
Fig. 62
Distribution duct
Distribution duct
Fresh air
CAUTION
1
When performing hole opening work, be careful not to
damage the drain pan.
2
When connecting the distribution duct, to make the air
flow easily, block the outlet port with the blower cover
insulation as shown by the hatched lines in Fig. 62. For
the blocking direction, refer to Fig. 38.
1. DIMENSION
Screw position and connection hole which are fresh air duct and distribu-
tion duct.
Fig. 63
P. D 120
160
4
5
°
4
5
°
ø100
ø70
113
334.2
P. D 88
97
Unit: mm
12-ø3.3 self tapping screw holes (for 4 mm)
2. DISTRIBUTION DUCT AND FRESH AIR DUCT
HOLE PROCESSING
Use the distribution duct hole and fresh air duct hole by removing the
insulation material as shown below.
Fig. 64
Cut
Cut
Cabinet
•
Cut off the part (Cabinet) indicated by the arrow in the Fig. 64 with
nippers, needle nose pliers, etc.
Fig. 65
PART NO. 9365388044
Fig. 51
NOTES
If the function to change the temperature sensor is used as shown in
examples A and B (other than example C), be sure to lock the detection
location. If the function is locked, the lock display
will flash when
the THERMO SENSOR button is pressed.
(1) Press the THERMO SENSOR button for 5 seconds or more to unlock
the function. The thermo sensor display flashes and then disappears
when the function is unlocked.
(2) Press the THERMO SENSOR button to select the temperature sen-
sor of the indoor unit or the remote controller.
Fig. 52
1. GROUP CONTROL SYSTEM
A number of indoor units can be operated at the same time using a single
remote controller.
(1) Wiring method (indoor unit to remote controller)
Fig. 56
Cabinet
Knife
Insulation
(Inner box)
14
1
2
3
O
F
F
SW 4
1
2
3
O
F
F
SW 1
Indoor unit PC board
Dip switch
(SW4)
Indoor unit
PC board
Fig. 36
DAY OFF
DELETE
SET
ENERGY
SAVE
THERMO
SENSOR
SET BACK
DAY
CLOCK ADJUST
3. AUTO RESTART
•
When the air conditioner power was temporarily turned off by a power
failure etc., it restarts automatically after the power recovers.
(Operated by setting before the power failure)
The auto restart function can be
canceled.
(1) DIP switch setting (indoor unit)
Change the DIP switch (SW1-1)
on the indoor unit circuit board
from ON to OFF. The auto restart
function will be canceled.
Indoor unit
O
F
F
1
2
3
OFF
SW1
O
F
F
1
2
3
SW4
DIP Switch
Fig. 61
3. CHECKING DRAINAGE
To check the drain, remove the water cover and fill with 2 to 3
r
of water as
shown in Fig. 55.
The drain pump operates when operating in the cooling mode.
Fig. 55
Water cover
Drain pipe
Watering pot
13
SPECIAL INSTALLATION
METHODS
CAUTION
1
When setting the rotary switch and DIP switches, do
not touch any other parts on the circuit board directly
with your bare hands.
2
Be sure to turn off the main power.
Indoor unit
Indoor unit
Remote
controller
wire
Fig. 57
Fig. 58
Indoor unit
Master
unit
Slave
unit
•
Open the holes and cut the insulation with a knife.
* Be careful not to damage the internal parts.
* Be careful not to cut yourself on the cutout in the metal plate.
* Please remove the insulation (inner box) left over after cutting.
•
Connect the distribution duct.
* When mounting the duct, block the gap so that there is no cold air leakage.
* Insulate the duct and cut connection.
CAUTION
The air conditioner cannot take in fresh air by itself. When
connecting a fresh air duct, always use a duct fan.
Remote
controller