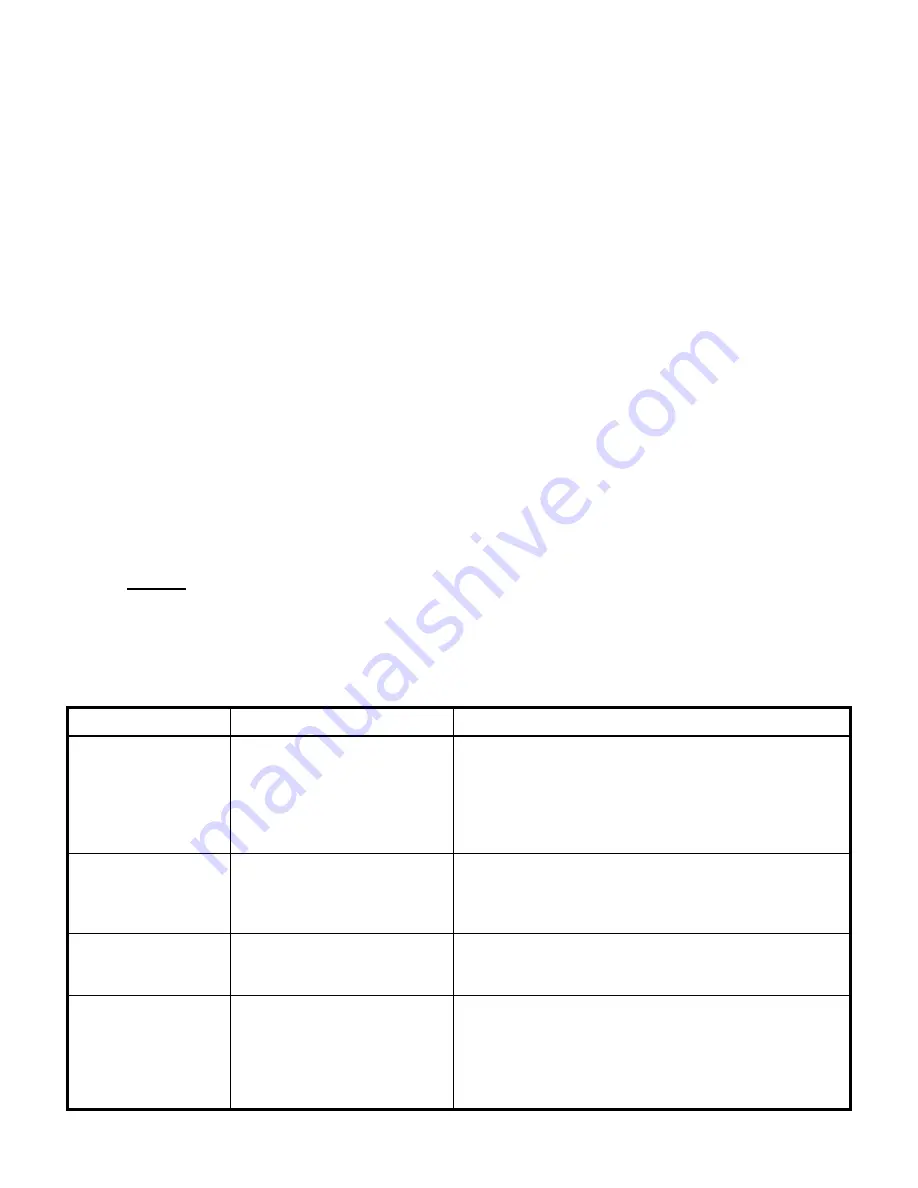
fuel safe container. Operate fuel pump until fuel exits fuel line. Attach fuel line back to the fuel rail after priming
fuel pump. After tightening connection, verify leak-free operation while checking fuel rail pressure. If fuel
pressure is not high enough, repeat priming procedure to ensure that fuel pump is receiving fuel from tank.
Turn on fuel pump (typically by bypassing fuel pump relay) without engine operating. ECU or engine
management computer may be controlling the relay. The ECU may only operate pump for a few seconds each
time ignition switch is set to on. The pump will have to operate several seconds (30+) to prime and drive air out
of the fuel system. Reattach fuel rail line. Start fuel system and inspect for leaks. Inspect vehicle for any leaks.
Turn off fuel system and repair any leaks that may be present before continuing.
7. When adjusting pressure, be sure that fuel pump is operating to monitor pressure. Fuelab recommends to use
a “baseline” pressure reference when adjusting the pressure (adjusting the pressure with engine off or pressure
reference line or vacuum line unhooked). The vehicle’s engine may not produce consistent vacuum during idle
to have repeatable readings.
8. After final adjustment of fuel pressure, tighten jam nut. Road test vehicle, and retest pressure upon return to
ensure accurate adjustment. After installation of this fuel pump, verify flow capacity to ensure safe levels of
flow, particularly with reduced levels of pump speed. Having insufficient flow capacity can result in an engine
lean-out condition that can cause severe engine damage. Collecting a given amount of fuel (as measured by
weight or volume) over a measured amount of time can be used to determine capacity. Collect fuel flow from
the return line to measure the amount of fuel capacity at a given operating pressure. A 20+ ampere capacity
battery charger may be used to simulate the charging system of the vehicle while engine is off. If using an
adjustable fuel pressure regulator, for boosted applications, simulate boost by raising the fuel pressure by the
amount of expected maximum boost pressure. Performing these tests will give greater accuracy for capacity
tests.
Fuel System Maintenance Notes:
Periodic inspections and general maintenance are required for longevity and reliability of the fuel system. This
action directly affects the fuel pump's performance and reliability. Included with that are periodic inspection and/or
filter element replacement. The straining filter (upstream of pump) should be checked and cleaned at least every
30,000 miles (more often for off-road operating conditions). Replace or clean downstream filters (after pump) every
year or 15,000 miles (more often for off-road operating conditions). Dirty fuel filters can block flow and adversely
effect fuel system performance as well as can directly damage the fuel pump.
Special alert for E85 or Methanol
Users:
DO NOT
use cellulose (paper) based filter elements! Water can contaminate the fuel and break down the
element, creating debris that can damage injectors and fuel pump. E85 and other oxygenated fuels can absorb
water. Long term storage of this fuel within the fuel tank of vehicle is not recommended and can contribute to
rusting of the fuel pump's tool steel components. Draining the fuel tank and replacement with small amount of
Gasoline or Kerosene (along with operating the fuel system for a small period of time) is recommended for long
term storage of the vehicle.
Troubleshooting Notes:
Problem (Symptom)
Possible Causes
Possible Solutions
Not operating or slight
"clicking" sound when
turned on.
Faulty fuel pump relay.
Faulty, dirty, or corroded
terminals or improperly sized
wire.
Debris from tank or plumbing
lodged inside pump.
Check voltage to controller, at power terminals. If
voltage is steady and consistent (within 1/2 Volt of
battery) then contact Fuelab for assistance or repair. If
voltage is inconsistent as described, repair or replace
electrical components as required.
Not building up fuel
pressure.
Incorrect fuel system initial
priming procedure.
Pump operating in reverse
direction (see above).
Repeat procedure for proper priming. If condition
continues, check all plumbing upstream (on inlet side) of
fuel pump.
Leakage of fuel at
inlet or outlet fuel
ports.
Improper type of fitting used. If leakage occurs at fitting, be sure that the proper fitting
style is used (AN o-ring seal type ONLY!). Pipe threaded
style fittings are NOT to be used.
Loss of fuel pressure
or erratic pressure
pulsation after several
minutes of operation.
Cavitation (vapor lock) due
to overheating or restricted
inlet.
Look for sources of heat such as exhaust or fuel rail
mountings that could be conducting too much heat.
Check for inlet restrictions such as improperly vented
tank, or debris blocking inlet straining filter. Contact
Fuelab, as pump may be damaged due to improper
operating condition for repair or consultation.
110020275-1, Rev C Sheet 5 of 6