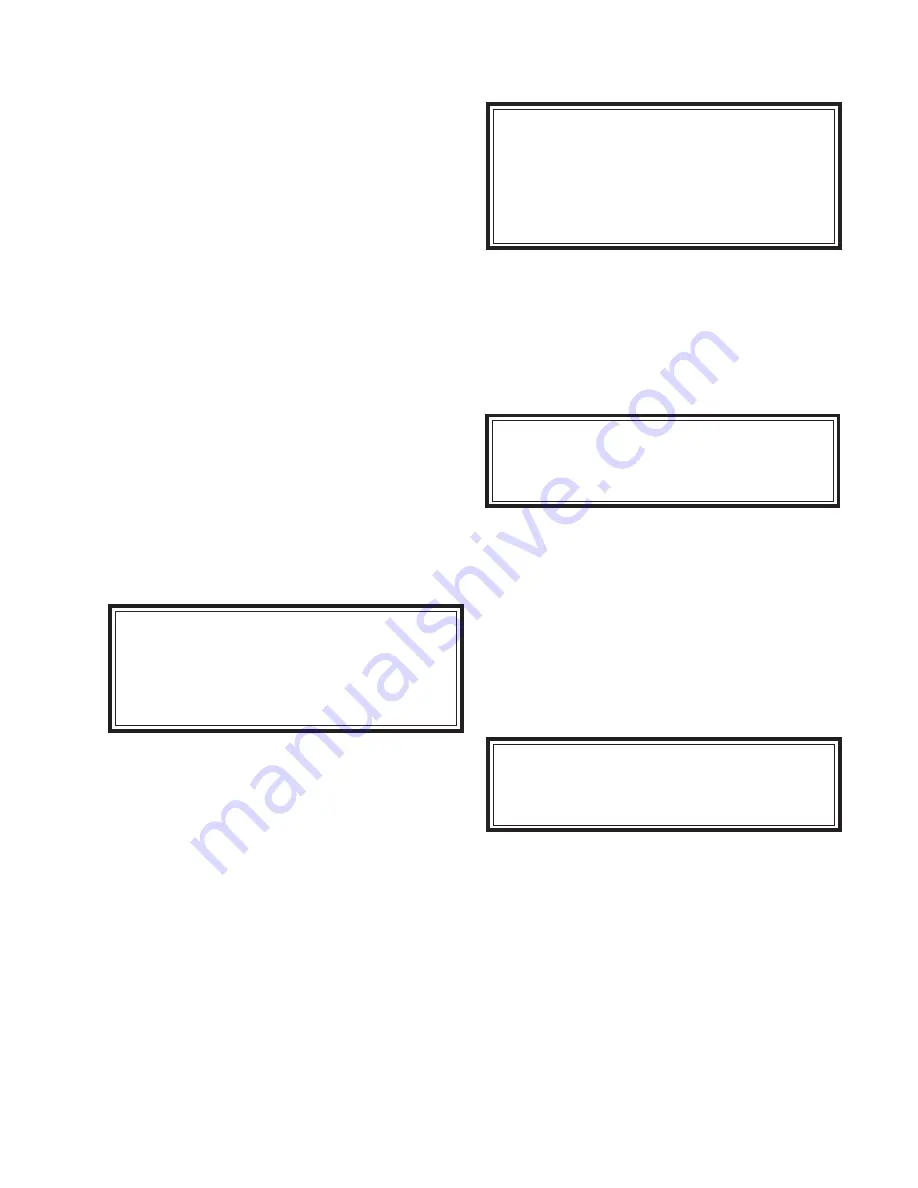
17
Charging The System
CAUTION: After charging the system with
liquid, be certain to wait at least 5 minutes
before starting the compressor to give the
refrigerant a chance to disperse throughout
the system. Otherwise, the compressor could
be damaged by attempting to pump
excessive quantities of liquid.
Preparing the Charging Cylinder:
1. Charging cylinder must have at least eight ounces
more refrigerant than required charge.
2. Plug in cylinder heater and bring pressure up to 30
pounds above gauge pressure at ambient
temperature. Maintain, but do not exceed, this 30
pound increase in gauge pressure during system
charging.
WARNING: DO NOT USE EXTERNAL HEAT
SOURCE ON CYLINDER OR EXCEED
MAXIMUM GAUGE PRESSURE ON
CHARGING SYSTEM.
To Charge System:
1. Make certain that hand shut-off valve to vacuum
pump is closed.
2. Set charging cylinder scale to pressure indicated on
cylinder pressure gauge.
3. Observe refrigerant level in sight glass. Subtract
amount to be charged into system and note shut off
point.
4. Open charging cylinder valve slowly and allow proper
charge to enter system.
5. As soon as refrigerant in sight glass has gone down
to predetermined level, close charging cylinder valve.
WARNING: DISCONNECT THE CHARGING
CYLINDER HEATER AT THIS TIME TO
PREVENT THE CYLINDER PRESSURE FROM
EXCEEDING ITS MAXIMUM LIMITS.
6. Allow system to sit for five minutes.
7. Turn on dehumidifier compressor. Run compressor
for few minutes and monitor system pressures.
5. Close hand shut-off valve to vacuum pump. Watch
compound gauge for several minutes. If reading rises,
there is leak in system, go to step 6. If no leak
is indicated, stop vacuum pump. System is now
ready for charging.
6. If leak is indicated, stop vacuum pump and
introduce small charge of refrigerant into system by
cracking valve on bottom of charging cylinder until
system is pressurized to 40 or 50 psig.
7. Leak test low-side. Close compound gauge.
Run compressor for few minutes and leak test high-
side. When leak is found, recapture refrigerant using
EPA approved recovery system, repair and go back
to step 1.
Installing Evacuation and Recharging Equipment
1. Disconnect dehumidifier from electrical supply.
2. Install process tube adaptor on process tube leaving
as much tube as possible.
3. Attach refrigeration service gauge manifold to
system in following order:
Low-side (compound gauge) to process tube
Center port manifold hose before hand shut-off
valve to charging cylinder.
Center port manifold hose after hand shut-off
valve to vacuum pump.
Evacuating System
To achieve the required levels of evacuation, a properly
maintained two- stage vacuum pump in good condition is
required. It is absolutely essential to maintain your
vacuum pump according to the manufacturers
instructions including required oil changes at the
recommended intervals. Vacuum pump oil should always
be changed after evacuating a contaminated system.
Vacuum pump performance should be checked
periodically with a micron gauge.
1. Make certain that charging cylinder valve, hand
shut-off valve, and manifold gauge valves are closed.
2. Start vacuum pump.
3. Open hand shut-off valve and slowly open manifold
valve, turning counterclockwise, for two full rotations.
CAUTION: If high vacuum equipment is
used, just crack manifold valve for a few
minutes, then open slowly for two full turns,
counterclockwise. This will prevent the com-
pressor oil from foaming and being drawn
into the vacuum pump.
4. Operate vacuum pump for minimum of 30 minutes
to attain minimum of 29.9 (500 micron) vacuum or
until vacuum of 500 microns is obtained..
8. When satisfied that unit is operating correctly,
clamp process tube with pinchoff tool while unit is still
running.
9. Remove process tube adaptor and solder the process
tube closed.
11.Turn on unit. After few minutes, check process
tubes for refrigerant leaks.
FINAL LEAK TEST
1. With dehumidifier turned OFF, leak test all low-side
system components.
2. Turn unit ON and run until condenser is warm. Leak
test high-side system components.