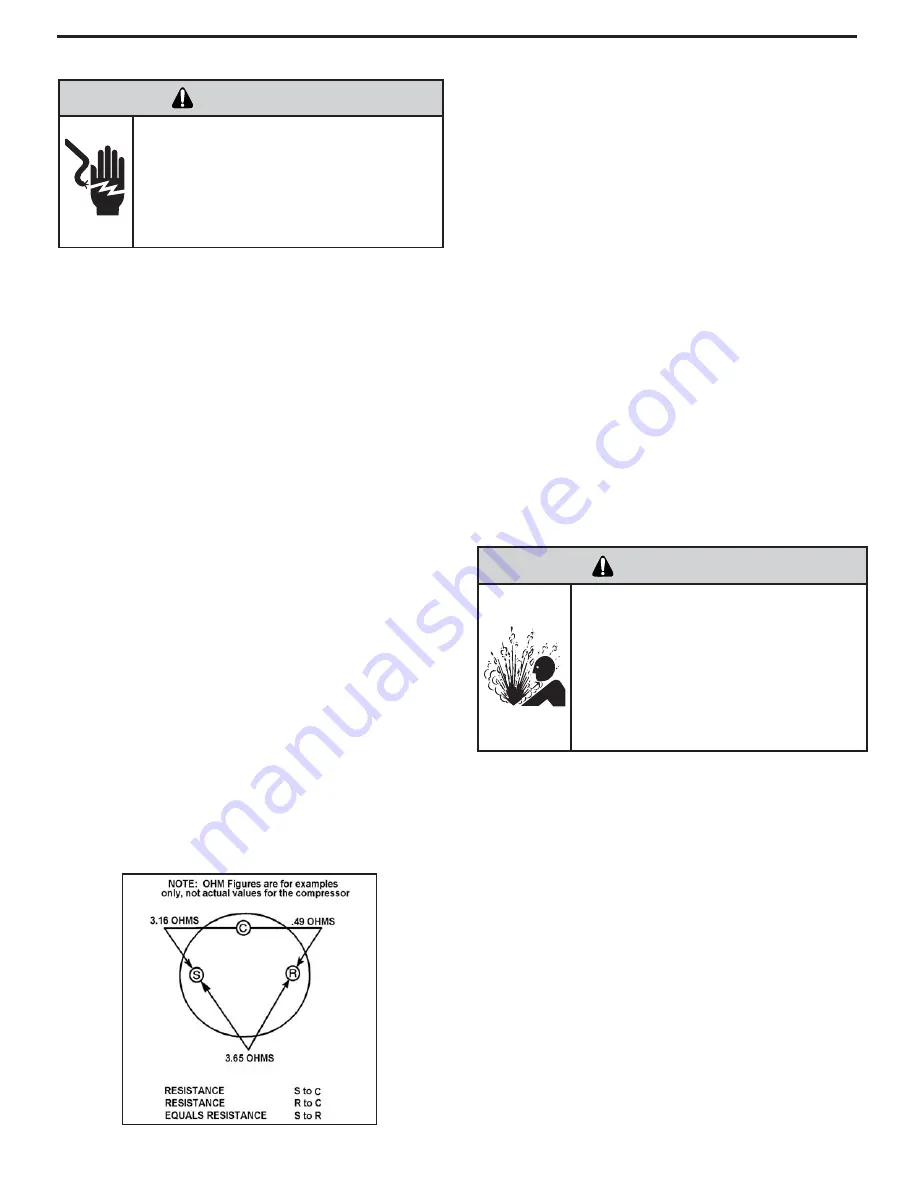
47
Single Phase Resistance Test
t
e
s
d
n
a
s
l
a
n
i
m
r
e
t
r
o
s
s
e
r
p
m
o
c
e
h
t
m
o
r
f
s
d
a
e
l
e
h
t
e
v
o
m
e
R
the ohmmeter on the lowest scale (R x 1).
n
o
m
m
o
c
s
l
a
n
i
m
r
e
t
m
o
r
f
r
e
t
e
m
m
h
o
e
h
t
f
o
s
d
a
e
l
e
h
t
h
c
u
o
T
r
e
t
e
m
m
h
o
e
h
t
f
o
s
d
a
e
l
e
h
t
h
c
u
o
t
,t
x
e
N
.
)
”
S
“
o
t
”
C
“
(
t
r
a
t
s
o
t
from terminals common to run (“C” to “R”).
Add values “C” to “S” and “C” to “R” together and
.
)
”
R
“
o
t
”
S
“
(
s
l
a
n
i
m
r
e
t
n
u
r
o
t
t
r
a
t
s
m
o
r
f
e
c
n
a
t
s
i
s
e
r
k
c
e
h
c
Resistance “S” to “R” should equal the total of “C” to “S”
and “C” to “R.”
In a single phase PSC compressor motor, the highest
o
t
”
S
“
(
s
n
o
it
c
e
n
n
o
c
n
u
r
e
h
t
o
t
t
r
a
t
s
e
h
t
m
o
r
f
e
b
l
li
w
e
u
l
a
v
e
h
t
o
t
t
r
a
t
s
e
h
t
m
o
r
f
s
i
e
c
n
a
t
s
i
s
e
r
t
s
e
h
g
i
h
t
x
e
n
e
h
T
.
)
”
R
“
common connections (“S” to “C”). The lowest resistance
is from the run to common. (“C” to “R”) Before replacing a
compressor, check to be sure it is defective.
GROUND TEST
Use an ohmmeter set on its highest scale. Touch one
lead to the compressor body (clean point of contact as
a good connection is a must) and the other probe in turn
to each compressor terminal. If a reading is obtained the
compressor is grounded and must be replaced.
Check the complete electrical system to the compressor
and compressor internal electrical system, check to be
certain that compressor is not out on internal overload.
Complete evaluation of the system must be made
whenever you suspect the compressor is defective. If
the compressor has been operating for sometime, a
careful
examination must be made to determine why the
compressor failed.
Many compressor failures are caused by the following
conditions:
1. Improper air
fl
ow over the evaporator.
2. Overcharged refrigerant system causing liquid to be
returned to the compressor.
3. Restricted refrigerant system.
4. Lack of lubrication.
5. Liquid refrigerant returning to compressor causing oil
to be washed out of bearings.
6. Noncondensables such as air and moisture in
the system. Moisture is extremely destructive to a
refrigerant system.
7. Capacitor (see page 34).
CHECKING COMPRESSOR EFFICIENCY
The reason for compressor inef
fi
ciency is normally due
to broken or damaged suction and/or discharge valves,
reducing the ability of the compressor to pump refrigerant
gas.
This condition can be checked as follows:
1. Install a piercing valve on the suction and discharge or
liquid process tube.
2. Attach gauges to the high and low sides of the system.
3. Start the system and run a “cooling or heating perfor
-
mance test.” If test shows:
A.
Below
normal high side pressure
B.
Above
normal low side pressure
C.
Low
temperature difference across coil
The compressor valves are faulty - replace the
compressor.
ELECTRIC SHOCK HAZARD
WARNING
Turn off electric power before service or
installation. Extreme care must be used, if it
becomes necessary to work on equipment
with power applied.
Failure to do so could result in serious injury or
death.
Sealed Refrigeration System contains refrigerant
and oil under high pressure.
Proper safety procedures must be followed,
and proper protective clothing must be worn
when working with refrigerants.
Failure to follow these procedures could
result in serious injury or death.
WARNING
HIGH PRESSURE HAZARD