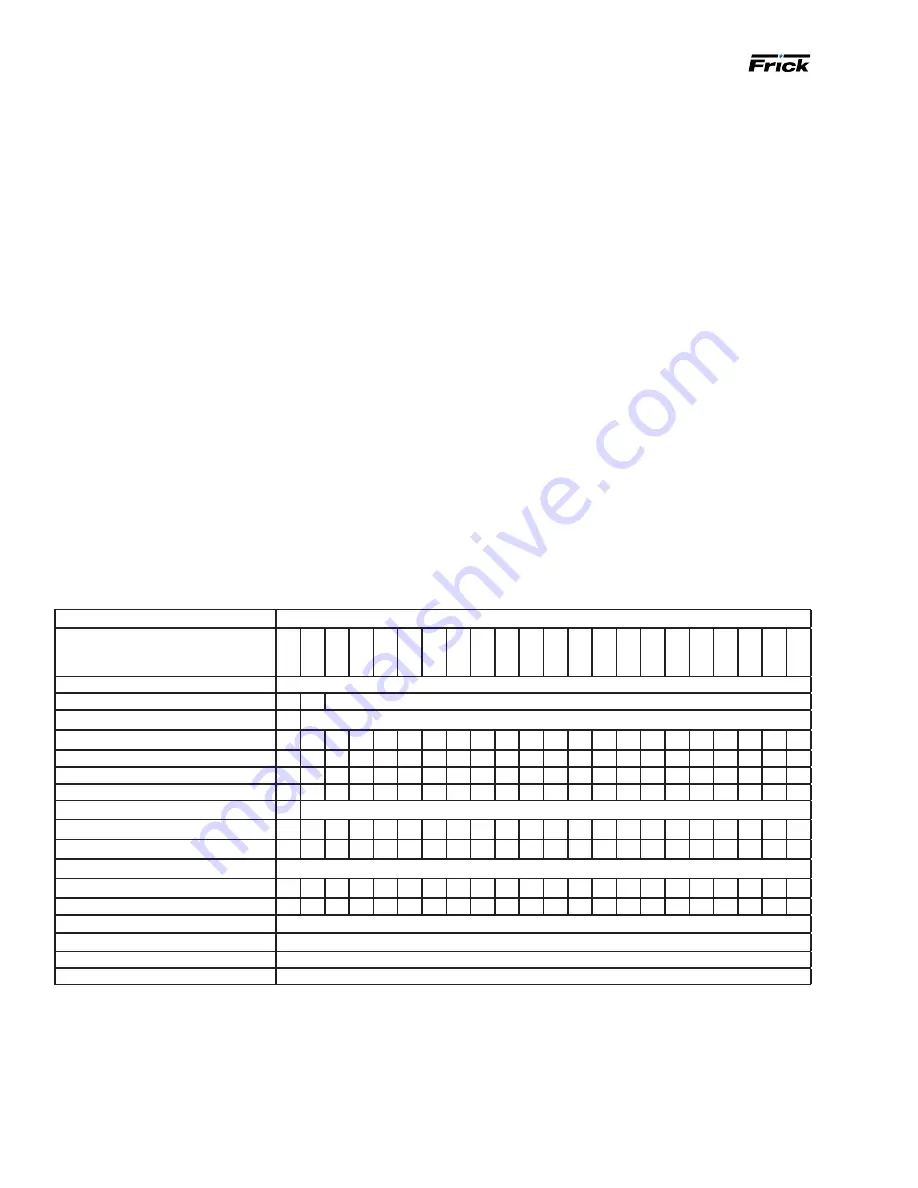
070.610-IOM (JUL 21)
Page 40
RWF II Rotary Screw Compressor Units
Maintenance
evidence of drag or contact in pump and increase
clearance where necessary
6. Rapid Wear.
a. Examination of a pump that has gradually lost its
ability to deliver capacity or pressure would show a
smooth wear pattern on all parts. Rapid wear shows
up as heavy grooving, galling, twisting, breaking, or
similar severe signs of trouble.
Preventive maintenance
Performing a few preventive maintenance procedures will
extend the life of your pump and reduce the cost per gal
-
lon pumped.
1. Lubrication
- Grease all zerks after every 500 hours of
operation or after 60 days, whichever occurs first. If ser
-
vice is severe, grease more often. Do it gently with a hand
gun. Use #2 ball bearing grease for normal applications.
For hot or cold applications, use appropriate grease.
2. Packing adjustment
- Occasional packing adjust
-
ment may be required to keep leakage to a slight weep; if
impossible to reduce leakage by gentle tightening, replace
packing or use different type. See Technical Service
Manual on particular model series for details on repacking.
3. End clearance adjustment
- After long service the
running clearance between the end of the rotor teeth and
Maintenance schedule
Follow this schedule to ensure trouble-free operation of the compressor unit.
Table 12: Maintenance schedule
c. Check alignment.
d. May have a bent shaft or rotor tooth. Straighten or
replace.
e. May be a foreign object trying to get into the pump
through the suction port.
4. Pump not up to capacity
a. Starving or cavitating - increase suction pipe size or
reduce length.
b. Strainer partially clogged - clean.
c. Air leak in suction piping or along pump shaft.
d. Running too slowly - is motor the correct speed and
is it wired up correctly
e. Relief valve set too low or stuck open.
f. Pump worn out.
g. Tighten end clearance.
h. Head position incorrect.
5. Pump takes too much power.
a. Running too fast - is correct motor speed, reducer
ratio, sheave size, etc. being used.
b. Liquid more viscous than unit sized to handle - heat
the liquid, increase the pipe size, slow the pump down,
or get a bigger motor.
c. Discharge pressure higher than calculated - check
with pressure gauge. Increase size or reduce length
of pipe, reduce speed (capacity), or get bigger motor.
d. Pump misaligned.
e. Extra clearance on pumping elements may not be
suffi cient for operating conditions. Check parts for
a. Check bolts, shim packs, center inserts, keys, and all bolt torques.
b. Check and torque all terminals in the processor and starter panel per the specification posted in the enclosure.
c. Check calibration of slide valve, slide stop, pressures and temperatures. Calibration should be conducted with NIST certified devices.
d. Verify tightness of bolts on suction and discharge flanges. See
for torque requirements.
e. Vibration measurement must be carried out continuously to obtain optimum preventive control on bearings. If not continuously controlled,
then every 6 months, more frequently if levels increase. See additional notes in
f. Units with variable speed drives - check for excess vibration and skip frequencies anytime unit operating conditions change.
g. The filter may need to be changed more frequently based on differential pressure or as directed by oil analysis.
h Refer to
070.210-IB
for foot mounting alignment.
Frequency or hours of operation (maximum)
Task description
200
1000
5000
8000
10
,000
15
,000
20
,000
25
,000
30
,000
35
,000
40
,000
45
,000
50
,000
55
,000
60
,000
65
,000
70
,000
75
,000
80
,000
85
,000
90
,000
95
,000
Change oil
As directed by oil analysis
Oil analysis
n
Every 6 months
Replace oil filters
(g)
n
As directed by oil analysis
Clean oil strainers
n
n
n
n
n
n
n
n
n
n
n
Clean liquid strainers
n
n
n
n
n
n
n
n
n
n
n
Replace coalescers
n
n
n
Check and clean suction strainer
n
n
n
n
n
n
n
n
n
n
n
Check coupling
(a)
n
Annually regardless of operating hours
Check alignment
(h)
n
n
n
n
n
n
n
n
n
n
n
Suction and discharge flange bolts
(d)
n n n n n n n n n n n n n n n n n n n n n n
Vfd units check skip freq.
(f)
Check annually
Check electrical connections
(b)
n
n
n n n n n n n n n n n n n n n n n n
Check sensor calibration
(c)
n n n
n n n n n n n n n n n n n n n n n n
Test high pressure cut-out
Test annually
Vibration analysis
(e)
Every 6 months, more frequently if levels increase
Motor grease
See motor grease section. Follow motor manufacturers recommendation.
Replace shaft seal
When leak rate exceeds 7 to 8 drops a minute