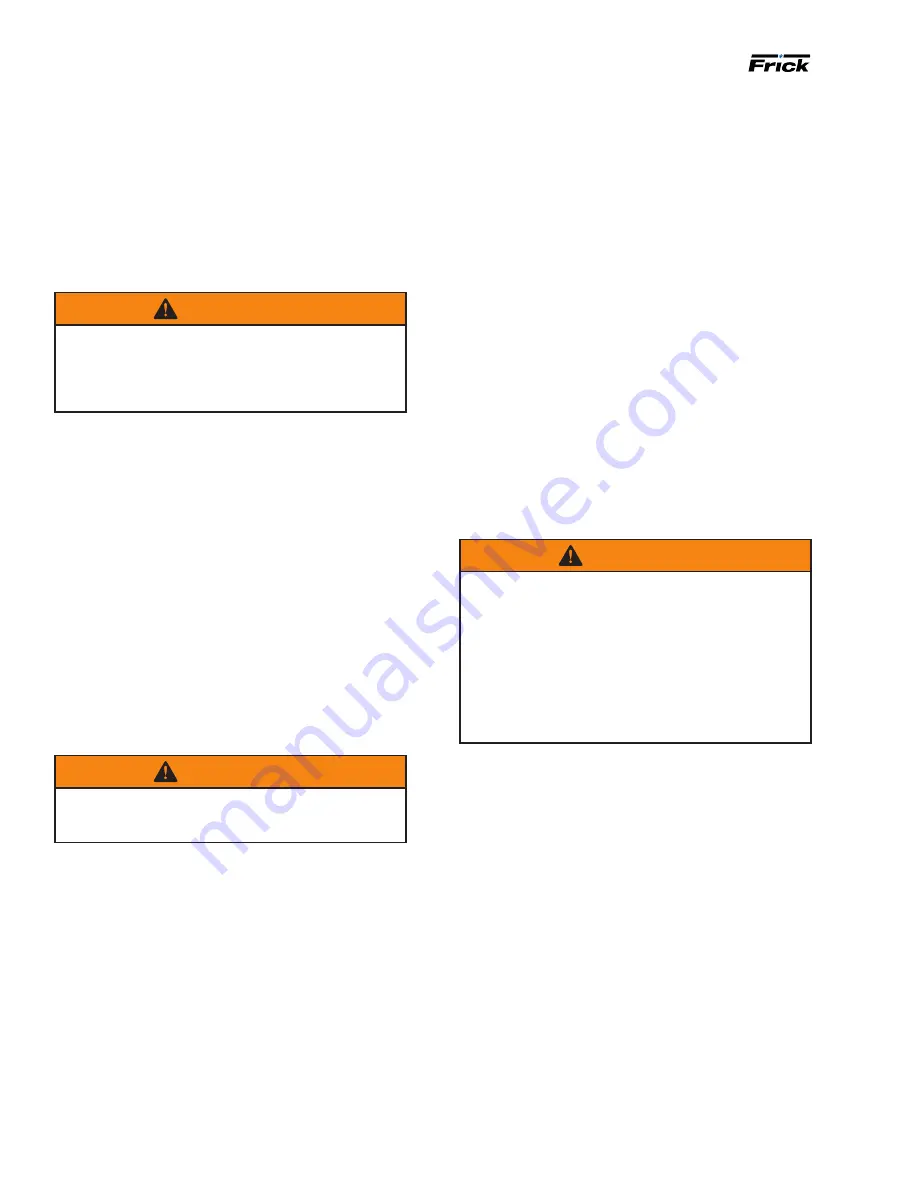
070.610-IOM (JUL 21)
Page 32
RWF II Rotary Screw Compressor Units
Operation
The second method is used for compressors with Liquid
Injection Oil Cooling. Because the discharge temperature is
controlled by the Liquid Injection Thermal Expansion Valve
you will not be able adjust for the correct oil flow by using
the discharge temperature. Before the initial startup of the
compressor, close the main oil injection hand expansion
valve completely. Open the valve back up and count the
turns that it takes to fully open the valve. After the initial
startup, close the valve until it is two turns open. The
valve may need to be closed further to reduce excessive
noise and vibration. However, do not fully close the valve.
WARNING
Failure to properly adjust this valve can lead to
excessive noise and vibration of the compressor and
package, premature failure of the bearings, liquid
loading of the rotors, liquid starvation of the rotors
and catastrophic failure of the compressor.
2.
For proper and safe operation, the compressor must be
run at the proper speed and discharge pressure. Exceeding
design conditions creates a potential hazard.
3.
Rotate and lubricate motor bearings according to
manufacturer’s recommendations
before
initial start-up as
required.
4.
After running the unit for approximately three hours,
adjust liquid injection oil cooling if applicable. If unit has
water cooled oil cooling, adjust
water control valve to
cooler.
5.
The compressor slide valve and slide stop linear trans-
mitters should be calibrated.
6.
Perform baseline vibration analysis. Required!
7.
For VFD applications, skip frequencies must be identified
and entered.
VFD skip frequencies
WARNING
Failure to enter skip frequencies could cause cata-
strophic compressor failure or severe compressor
damage and result in serious injury or death.
Criteria for identifying elevated energy on VFD
packages and establishing skip frequencies
With the RWF II running loaded at full speed, the entire
package must be physically checked for elevated energy,
including any corresponding extremities such as valves, liquid
injection piping, brackets, tubing, oil cooler and oil piping.
The
VFD speed is to be decreased by 100 rpm increments
and the entire package physically checked for elevated ener
-
gy at each stage until the minimum speed range is reached.
As the high energy hot spots are identified, they are to be
checked with a vibration meter and any readings that meet
or exceed one inch per second must have that frequency
range skipped in the microprocessor for the VFD, eliminating
the ability of the package to operate within that
frequency
range. Each identified range needs to have the skip set to as
narrow a frequency band as possible, only making it wider
until full range is accommodated. Also refer to
070.902-IB
for acceptable package vibration readings.
Review skip frequencies as shown in the
Normal start-up procedure
1.
Confirm system conditions permit starting the compres-
sor.
2.
Press the
[RUN]
key.
3.
Allow the compressor to start-up and stabilize. Press
the
[AUTO]
key immediately below the V ratio label
on the operating display screen. Press the
[AUTO]
key
im mediately below the SV POS label on the operating
display. The compres sor is now operating in the automa tic
mode.
4.
Observe the compressor unit for mechanical tightness
of the external piping, bolts and valves. Ensure that the
machine is clean from oil and refrigerant leaks. If any of
these occur, shut down the compressor and correct the
problem as necessary using good safety precautions.
5. Ensure manway bolts remain finger tight after the
compressor unit is in operation, as the manway bolts
will loosen as a result of pressurization.
WARNING
Overtightening components could result in a fire,
serious injury or property damage.
Do not apply the manway bolt torque specified for
an unpressurized unit while the unit is pressurized.
Applying this torque when the manway is pressur-
ized can overstress the manway gasket. Overstressing
the gasket can lead to gasket failure and/or a system
leak.
Trained technicians are required for servicing.
Restarting the compressor unit after a control
power interruption (plant power failure)
1.
Check variable setpoints.
2.
Follow normal start-up procedure.