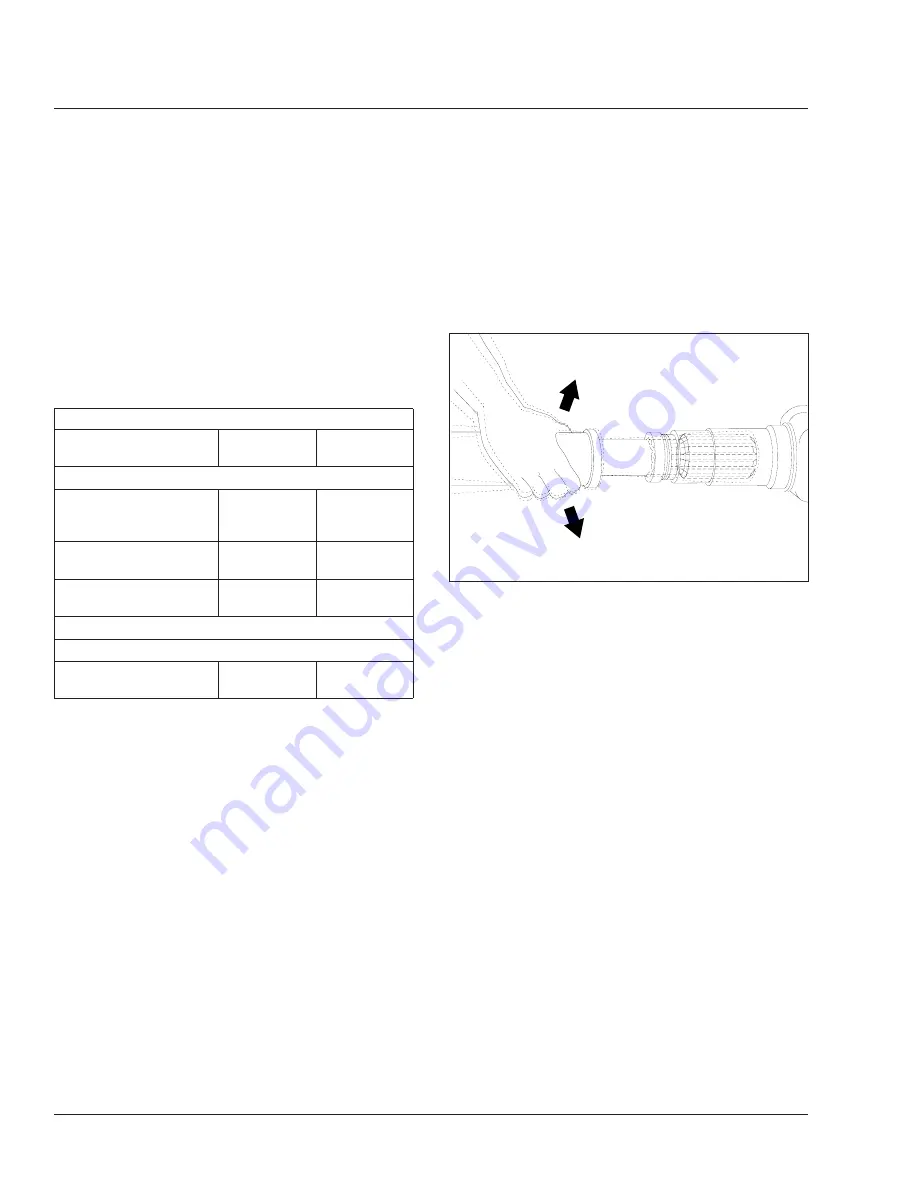
2.
Check each of the output and input end yokes
for cracks and looseness. See
, Refs. 2
and 11. Replace cracked yokes. If any end yoke
can be moved in or out on its shaft, or can be
rocked on its shaft, disconnect the driveshaft and
U-joint from the end yoke. Check the drive com-
ponent’s shaft seal for leakage or other visible
damage that may have been caused by the
loose yoke. Replace the seal if needed. Tighten
the end-yoke nut to the value in
. If the
end yoke is still loose after tightening the yoke
nut, install a new yoke and yoke nut.
End-Yoke Nut Torque Specifications
Description
Thread Size
Torque:
lbf·ft (N·m)
Transmissions
Fuller FS 4205A, 4205B,
5205B, 6305A/B, 5306A,
6306A
1-1/4–18
300–350
(405–475)
Allison AT545,542, MT &
MT643
1/2–20
*
102–121
(138–164)
Allison MD Series,
MD3060P
2–16
600–800
(815–1085)
Single Axle Input Shaft
Coupling Shaft (Midship Bearings)
Spicer SPL90, 1610,
1710
1-1/4–18
475–525
(644–712)
*
The Allison AT-545 transmission output shaft end-yoke is retained by a
1/2-20 x 1-1/2-inch bolt and a 1-1/16-inch washer. Both the bolt and the
washer must be replaced each time they are removed.
Table 1, End-Yoke Nut Torque Specifications
NOTE: If the end-yoke locknut was removed for
any reason, install a new one.
3.
Check the U-joint assemblies for wear by at-
tempting to move the driveshaft up and down,
and from side to side. If movement of the U-joint
trunnion in the bearings is greater than 0.006
inch (0.15 mm), replace the U-joint assembly.
4.
Check the midship bearing and bracket for loose-
ness and deterioration by attempting to move the
driveshaft up and down, and from side to side. If
the bearing is loose on its shaft, or rattles, re-
place it. If the bearing bracket is loose on the
frame, or the bearing mount is loose on the
bracket, tighten the mounting bolt nuts 91 lbf·ft
(123 N·m). Replace the midship bearing assem-
bly if the rubber cushion is worn or oil-soaked.
5.
Check the slip-joints for spline wear by trying to
bend the sleeve-yoke and splined shaft back and
forth. See
. If looseness is greater than
0.007 inch (0.18 mm), replace both the sleeve-
yoke and the splined shaft.
6.
Check the driveshaft tubes for dents, bends,
twists, or other damage. If any tube appears to
be damaged, remove the driveshaft and check
the runout on the tube. If the tube is not straight
(and cannot be straightened) within 0.005 inch
(0.127 mm) on the slip-joint seal surface of the
splined shaft, 0.010 inch (0.254 mm) on the tube
3 inches (76 mm) from the front and rear welds,
and 0.015 inch (0.381 mm) at the center of the
tube, replace the tube. See
If the driveshaft tube requires straightening or
replacement, balance the repaired driveshaft be-
fore installing it. See Group 41 of the
School
Bus Chassis Workshop Manual
.
7.
Check the driveshaft for missing balance
weights, and for debris build-up. Remove any
build-up. If any balance weights are missing, re-
move the driveshaft and have it balanced; see
Group 41 of the
School Bus Chassis Workshop
Manual
.
8.
For driveshafts with slip-joints, check that the
yoke plug is not loose or missing. See
Ref. 2. Replace the yoke plug if needed. If the
yoke plug is missing, the splined shaft may be
f410012a
05/27/93
Attempt to bend the sleeve yoke and splined shaft back
and forth.
Fig. 2, Slip-Joint Spline Wear Checking
Driveline
41
School Bus Chassis Maintenance Manual, April 1998
41/2