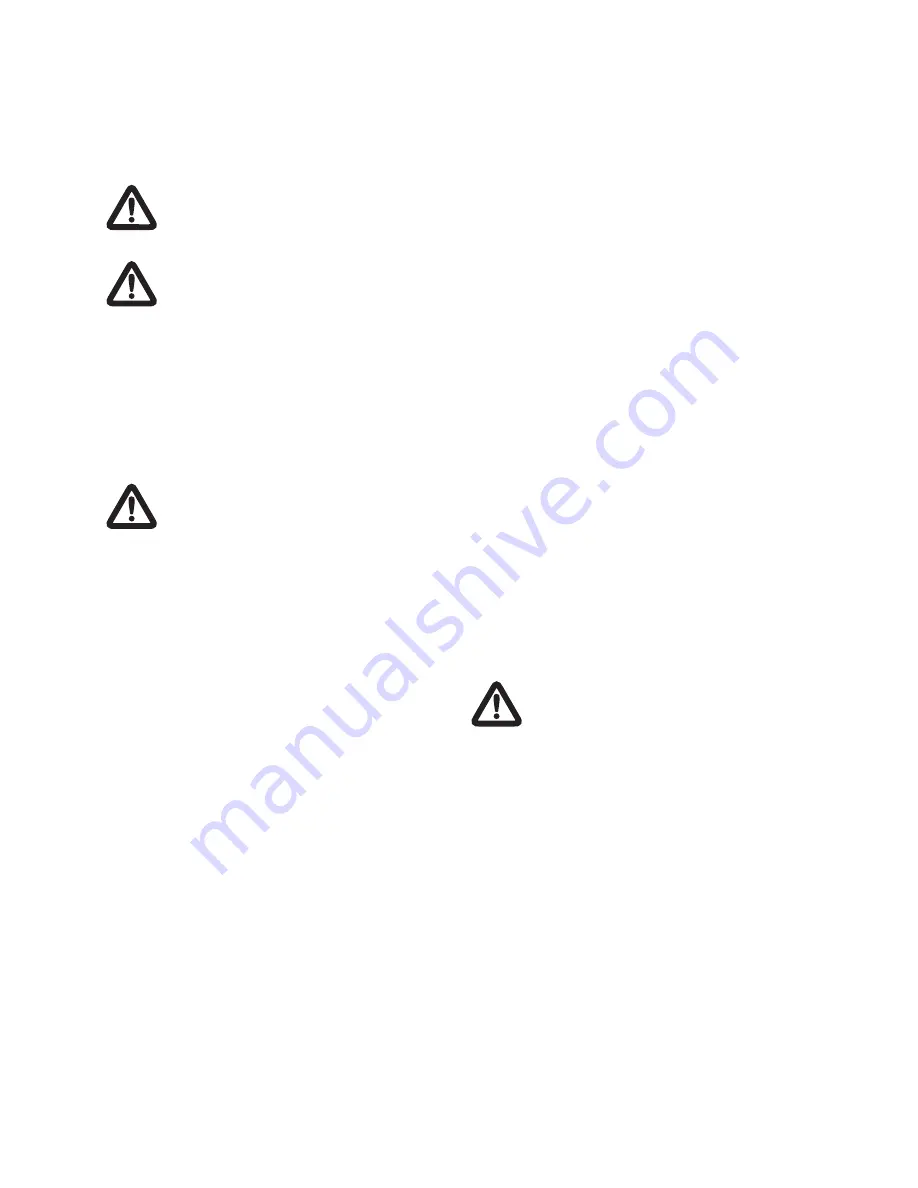
Reassemble the joint covering carter and re-tighten
the screws of the motor at the end of the above
mentioned procedure.
Wire electric cables to the motor according to the
diagram given within the cover of the terminal board.
Avoid any contact of the electric cables with
the pipes or other parts of the pump. Carefully
insulate the cables against humidity.
ALWAYS CONNECT THE GROUND.
5 COMMISSIONING
CAUTION: The pump must NOT be started without
previous filling. Dry running can damage irreparably
the mechanical seal and the bearings.
Make sure not to remain in the trajectory of
liquid output from the valve during the start of
the pump, a liquid output may occur during the
drainage, which would be dangerous for the
user in case the liquid is at high temperature
or in case of pumping of hazardous liquids.
5.1 Filling and drainage
5.1.1 Pump under pressure (see figure 1.A
and figures 3.A and B)
1- Close the gate valves on the delivery side of the
pump in order to avoid the flow in the circuit of the fluid
that is being used to fill the pump.
2- Remove the upper drainage cap (see fig. 3.A)
and unscrew slightly the by-pass valve (see fig. 3.B)
in order to let the two internal chambers of the pump
communicate and ease their filling. Do not remove
completely the by-pass valve, this is removed only and
exclusively to empty the pump. In the filling phase just
unscrew it for 3 or 4 turns.
3- Open the gate valve located on the pump suction
side in order to let the fluid come out on the pump. Make
sure that the difference in level between the pump and
the shutter is such as to assure a complete filling of
the pump.
4- When there is an homogeneous flow from the
drainage cap close it again carefully. Close the
by-pass valve.
5- Check the motor rotation direction as indicated on
the same.
6- Start the pump and check that it rotates on the
right direction.
7- Open the gate valve slowly on the discharge side
until stroke end.
Pay particular attention to point 3 in case the pump is
filled with hot or hazardous liquids, since the fluid coming
out of the upper drainage cap may hit people. Make sure
you are in a safety position during this operation. Close
the gate valve after the outcome of a constant liquid flow
from the cap before closing it again in order to avoid the
contact with the liquid.
5.1.2 Pump in suction (see figure 1.B and
figure 3.A, B and C)
1- Close the gate valve on the pump delivery side in
order to prevent the flow in the circuit of the fluid that is
being used to fill the pump and open the gate valve on
the suction side.
2- Remove the upper drainage cap (see fig. 3.A)
and unscrew slightly the by-pass valve (see fig. 3.B)
in order to let the two internal chambers of the pump
communicate and ease their filling. Do not remove
completely the by-pass valve, this is removed only and
exclusively to empty the pump. In the filling phase just
unscrew it for 3 or 4 turns.
3- Fill the pump as shown in figure 3.C until the fluid
comes out from the upper drainage cap.
4- Carefully close the cap again.
5- Check the motor rotation direction as indicated on
the same.
6- Start the pump and check that it rotates on the
right direction.
7- Open the gate valve slowly on the discharge side
until stroke end.
CAUTION: the pump must not work for more than
10 minutes with the delivery valve closed and with
pumped liquid temperature higher than 40
º
C. If the
temperature is higher, limit this time to 5 minutes.
6 MAINTENANCE
Before any intervention on the pump, make
sure that power supply has been disconnected
and that it cannot be restored accidentally
during maintenance.
The bearings of the pump and the mechanical seal do
not require maintenance. If the pump is emptied before a
long period of standstill, remove one of the joint covering
elements and grease slightly with silicone oil the shaft
between the head of the pump and the motor in order to
avoid the gluing of the mechanical seal.
Motors without greasing nipple: the bearings are life-
long greased and do not require any greasing. Motors
with greasing nipple: grease these motors with lithium
oil for high temperatures following the instructions given
on the motor cover.
In case the pump works seasonally, grease the motor
before any prolonged standstill.
To protect the pump against frost, empty it completely
removing the upper drainage cap (see fig. 3.A) and
extracting the by-pass valve (see fig. 3.B) completely
in order to let all the liquid flow outside the pump. Once
the pump has been emptied, let it without caps. When
proceeding to its commissioning again, repeat the filling
and drainage according to point 5.
3