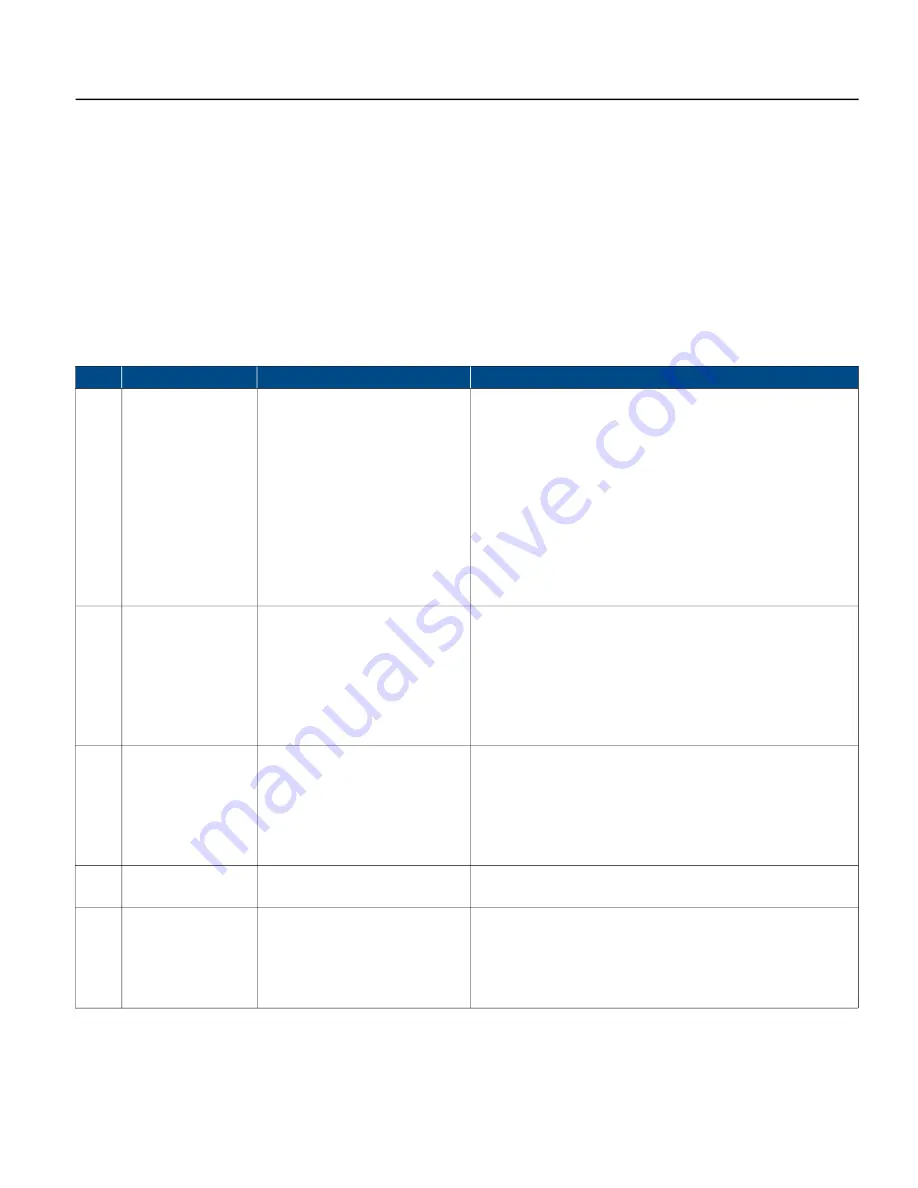
MAINTENANCE
Troubleshooting
41
Troubleshooting
System Diagnostics Fault History
The drive continuously monitors system performance and can detect a variety of abnormal conditions. In
many cases, the drive will compensate as needed to maintain continuous system operation; however, if
there is a high risk of equipment damage, the drive will stop the system and display the fault condition. If
possible, the drive will try to restart itself when the fault condition subsides. Each time a fault is detected in
the system, the drive records the fault with the date and time the fault was detected. A maximum of 100
events are recorded. Events can be viewed and retrieved with the USB device or the SubDrive Connect Plus
mobile app.
Diagnostic Fault Codes
Code
Fault
Possible Cause
Corrective Action
F1
Motor Underload
• Over-pumped well
• Broken shaft or coupling
• Blocked screen, worn pump
• Air/gas locked pump
• SubDrive not set properly for
pump end
• Underload Sensitivity setting
incorrect
• Frequency near maximum with load less than configured
underload sensitivity (SubDrive Connect Plus mobile app)
• System is drawing down to pump inlet (out of water)
• High static, light loading pump - reset Underload Sensitivity
setting (in the programming menu and mobile app) if not out
of water
• Check pump rotation, reconnect if necessary for proper
rotation
• Air/gas locked pump - if possible, set deeper in well to reduce
• Verify MAX AMPS setting (in the programming menu and
mobile app) is correct
F2
Undervoltage
• Low line voltage
• Miswired input leads
• Loose connection at breaker or
panel
• Line voltage low, less than approximately:
- 155 VAC (normal 230 operating range = 190 to 260 VAC)
- 290 VAC (normal 460 operating range = 380 to 520 VAC)
• Check incoming power connections and correct or tighten if
necessary
• Incorrect incoming voltage - check fuses, contact power
company
F3
Overcurrent or
Locked Pump
• Motor and/or pump
misalignment
• Dragging motor and/or pump
• Motor and/or pump locked
• Abrasives in pump
• Excess motor cable length
• Amperage is above MAX AMPS at 30 Hz
• Remove and repair or replace as required
• Reduce motor cable length. Adhere to Maximum Motor Cable
Length table.
F4
Incorrectly Wired
• Input and output wires are
swapped
• Check wiring, check motor size, adjust or repair as needed
F5
Open Phase
• Loose connection
• Defective motor or drop cable
• Wrong motor
• Open reading on DC test at start.
• Check drop cable and motor resistance, tighten output
connections, repair or replace as necessary.
• Use dry motor to check drive functions. If drive runs and
exhibits an underload fault, drive is good.
Содержание SUBDRIVE CONNECT PLUS
Страница 1: ...franklinwater com SUBDRIVECONNECTPLUS Owner s Manual ...
Страница 15: ...PHYSICAL INSTALLATION Drive Dimensions 15 Drive Dimensions Frame 2 Frame 3 ...
Страница 54: ...NOTES ...
Страница 55: ...NOTES ...
Страница 56: ...800 348 2420 franklinwater com For technical assistance please contact Form 226203201 Rev 000 04 2020 ...