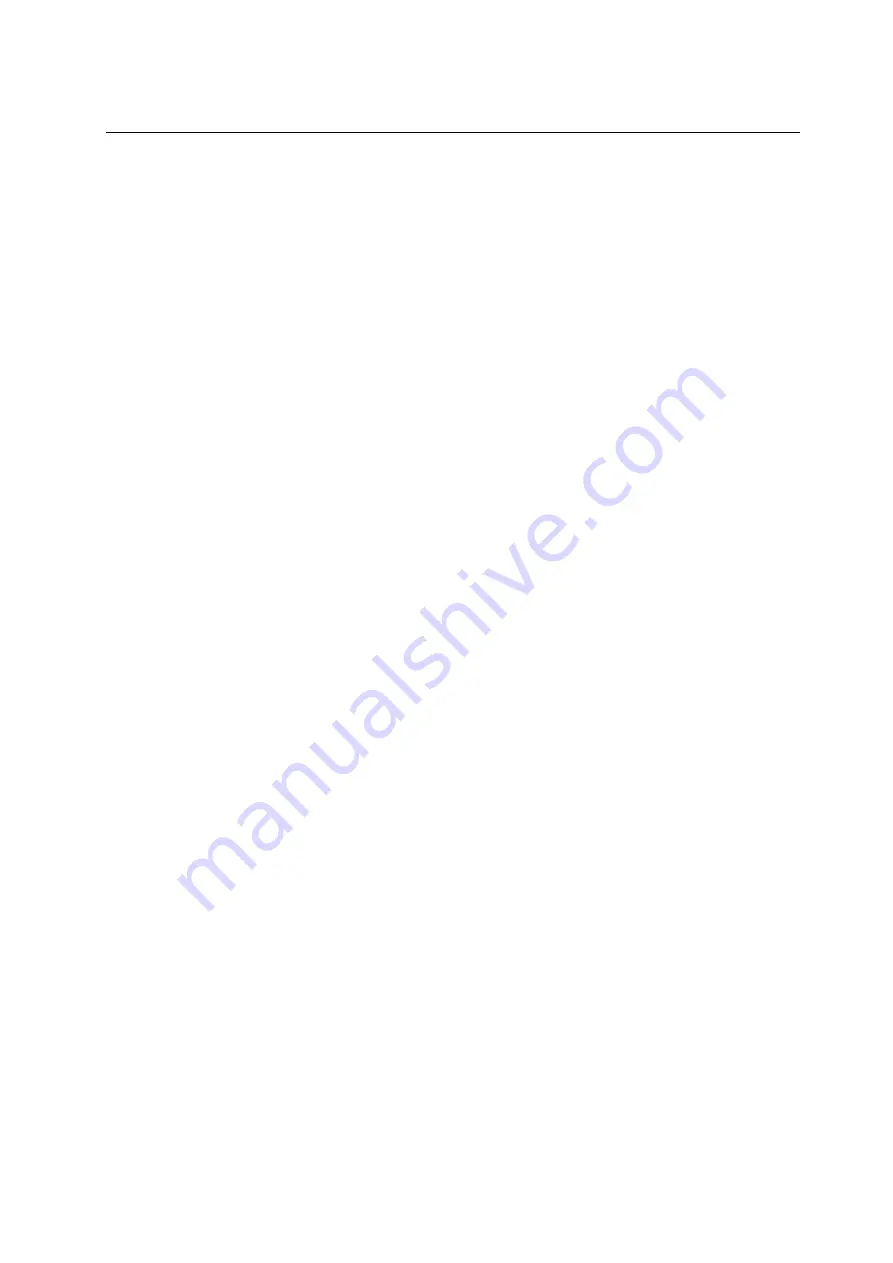
13
Tools Formech FM660
Tools for vacuum forming should always be solidly constructed as the operating air pressure reaches
approximately 100 kg over an area 100mm x 100mm (one ton per square foot)
All tools should be mounted on a baseboard. They cannot have undercuts and must be produced with
slightly angular sides ('draft angle') to aid release. Vent holes are needed to allow the air to be
evacuated from pockets and sharp angles on the tool. Providing these holes are kept small they will not
leave marks on the surface of the finished moulding.
Tools made from wood or medium density fibreboard (MDF) are easily constructed and can give short
runs of good quality mouldings at a low cost. (See note below)
The use of close-grained wood will avoid grain patterns appearing on the mouldings.
Plaster of Paris may be used for one-offs but the plaster must be allowed to properly dry out.
(See note below)
Metal tools have the advantages of carrying fine detail and being more resistant to both distortion and
surface damage. Metal tools should be pre-heated before use. A cool metal mould will absorb some of
the heat from the plastic sheet before it can take up the full definition.
Resin tools combine most of the advantages of metal moulds with relative ease of manufacture.
Various resinous materials are commercially available especially for vacuum forming tool production.
NOTE
: Porous mould materials such as wood and plaster should be properly sealed to prevent the
vacuum pump from sucking out any moisture or sawdust, loose plaster etc. The vacuum circuit may
quickly become choked with dust or slurry if moulds are not properly sealed.
Repairs to the vacuum circuit can be costly. A drain filter option is available and strongly
recommended if forming plaster moulds. The vacuum filter is not designed to prevent moisture
getting into the vacuum pump.
As the plastic cools after forming it will contract, gripping the tool tightly. If the tool has been made with
sloping sides and has a good surface finish it will release more easily. Where the draft angle must be
kept to a minimum a release agent may be used to assist release.
Sealed moulds will usually release more easily. Silicon based release agents may be used on more
difficult moulds. Silicon based release agents are rapidly absorbed by porous (unsealed) moulds,
rendering them ineffective.
The use of talc as a release agent is not recommended. It may clog the vacuum circuit.