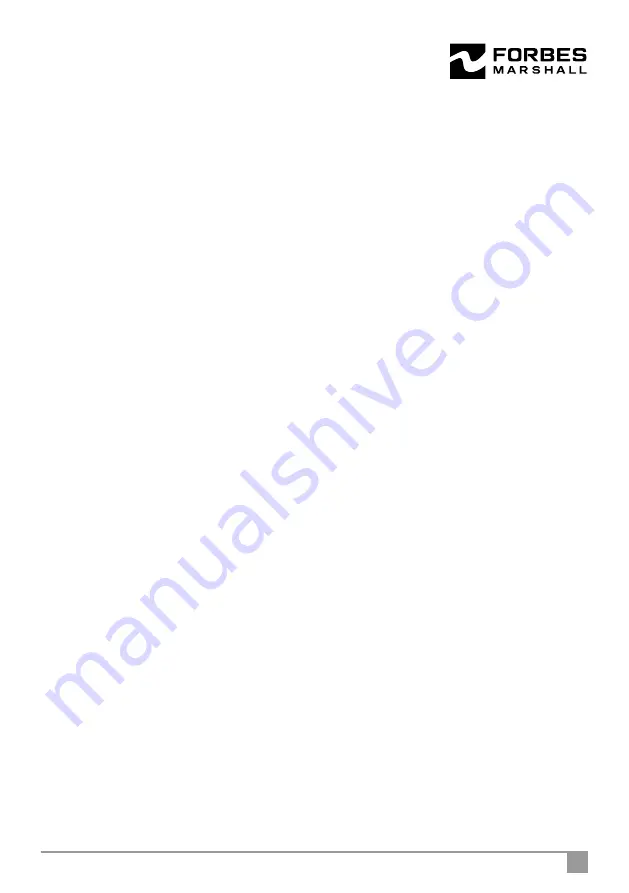
13
FMPRV41
Remove the internal balance pipe assembly. The resulting 1/8'' BSP tapping in the side of the
body should be blanked using a plug provided in the bag attached to the valve. The other
1/4'' BSP tapping in the side of the pilot valve chamber should be used to fit the external
pressure sensing pipe. This is suitable for the fitting of 13.7mm O/D pipe. If suitable pipe is
not available the compression fitting can be removed and 1/4'' nominal bore steel pipe
screwed directly to the pilot valve chamber. The pressure control pipe should be connected
in to the top of the reduced pressure main at a point where in either direction there is a
length of straight pipe uninterrupted by fittings for at least 1mor 15 pipe diameters
whichever is the greater. It should be arranged with a positive fall so that any condensate
can drain away from the FMPRV41.Where the size of the reduced pressure main makes it
difficult to maintain a fall when entering the top of the main, the pressure control pipe may
be connected in the side of the main.
5.8 Pressure gauges:
It is essential to fit a pressure gauge on the downstream side so that the valve can be properly
set. A pressure gauge on the upstream side can also be useful.
5.9 Continuous Duty:
For continuous duty applications where a constant steam supply is essential then a parallel
stand- by pressure reducing valve station is recommended to allow for planned
maintenance see fig 6. Alternatively a by-pass line can be used (see fig 7). It is important that
the by-pass should have a similar capacity to the Forbes Marshall Pilot Operated Pressure
Reducing Valve which is achieved by choosing an appropriately sized valve or by using a
reduced orifice in the line.
The hand wheel should be pad locked to prevent unauthorised use, and when in use should
be under constant manual supervision.
The by-pass may be arranged above or to the side of the main assembly but never below it.
5.10 Safety valve:
A safety valve should be fitted to protect the down steam equipment from excessive
pressure. It should be set to lift below the safe working pressure of the downstream
equipment and will normally be sized to pass the full capacity of the pressure reducing valve.
The safety valve set pressure should take account of its re seat characteristics and the 'No-
load' pressure setting of the pressure reducing valve. For example, the typical blowdown
value (re seat differential) for a DIN type safety valve is 10% of the set pressure. The
minimum possible safety valve set pressure must there for equal the no-load set pressure of
the reducing valve plus the blowdown value of the safety valve plus a small margin of atleast
0.1bar. If the safety valve lifts and the working pressure is too close then it will not be able to
close properly and will simmer, create a leak which is often wrongly diagnosed as a result of a
leaking reducing valve.
Discharge pipe work should be taken to a safe place.