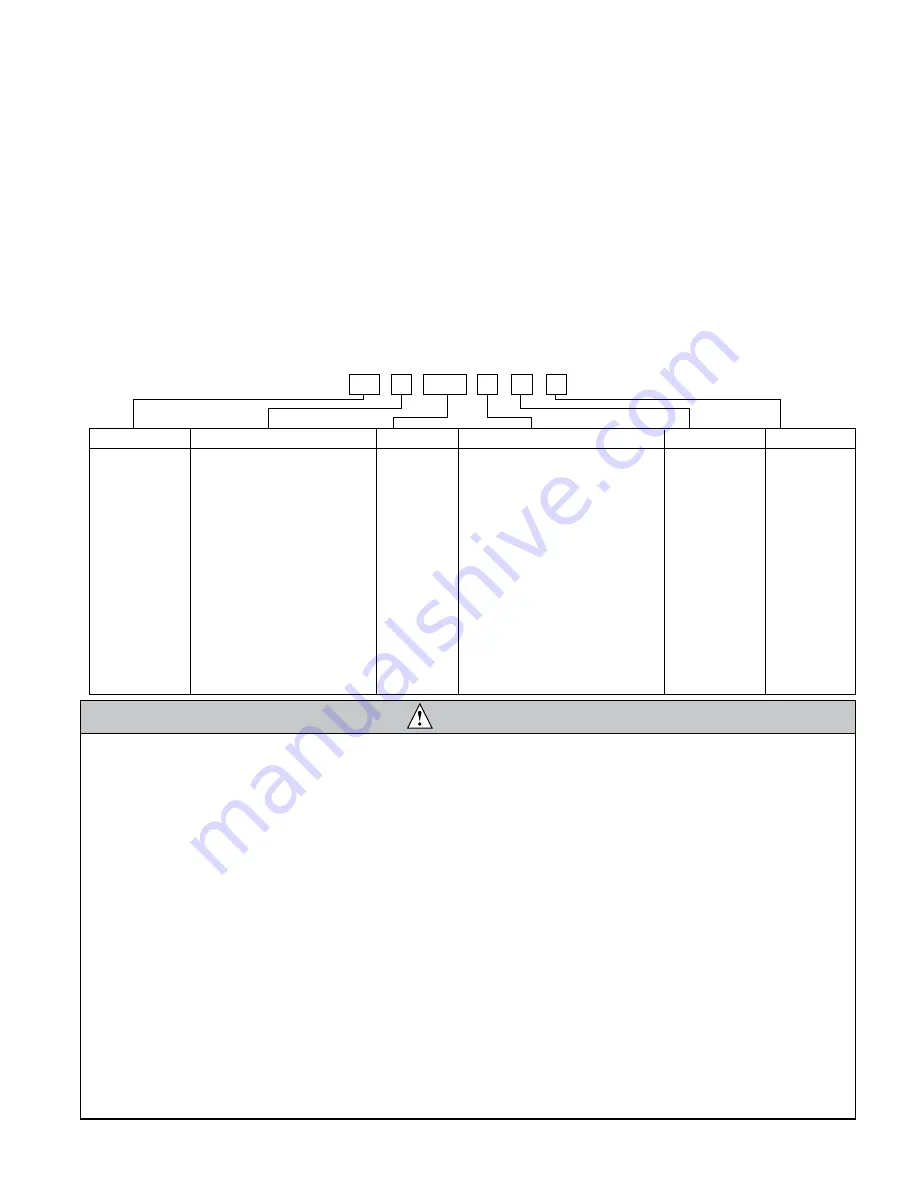
HCE710A, HME710A
3
Welcome to Follett
Follett equipment enjoys a well-deserved reputation for excellent performance, long-term reliability and outstanding
after-the-sale support. To ensure that this equipment delivers the same degree of service, we ask that you review
the installation manual (provided as a separate document) before beginning to install the unit. Our instructions are
designed to help you achieve a trouble-free installation. Should you have any questions or require technical help at
any time, please call our technical service group at (877) 612-5086 or +1 (610) 252-7301.
Before you begin
After uncrating and removing all packing material, inspect the equipment for concealed shipping damage. If
damage is found, notify the shipper immediately and contact Follett LLC so that we can help in the filing of a claim,
if necessary.
Check your paperwork to determine which model you have. Follett model numbers are designed to provide
information about the type and capacity of Follett equipment. Following is an explanation of the different model
numbers in the series.
CAUTION
§
Installation and service must be performed in accordance with all federal, state and local laws. It is the responsibility of the technician to
ensure that these requirements are met.
§
To reduce risk of shock, disconnect power before servicing.
§
A qualified person shall provide a readily accessible disconnect device incorporated into the fixed wiring.
§
This appliance should be permanently connected by a qualified person in accordance with applicable codes.
§
Connect to potable water supply only.
§
Follett recommends a Follett water filter system be installed in the ice machine inlet water line (standard capacity #00130229, high capacity
#00978957, carbonless high capacity #01050442).
§
Prior to operation clean the dispenser in accordance with instructions found in this manual.
§
This appliance is designed for commercial use.
§
Warranty does not cover exterior or outside installations.
§
WARNING! To avoid a hazard due to instability of the appliance, it must be fixed in accordance with the instructions.
§
Do not tilt unit further than 30° off vertical during uncrating or installation.
§
Dispenser bin area contains mechanical, moving parts. Keep hands and arms clear of this area at all times. If access to this area is
required, power to unit must be disconnected first.
§
This appliance is not suitable for installation in an area where a water jet could be used.
§
This appliance must not be cleaned by a water jet.
§
User maintence should not be done by children.
§
Do not block air intake or exhaust.
§
If the supply cord is damaged, it must be replaced by the manufacturer, its service agent or similarly qualified persons in order to avoid a
hazard.
§
This appliance can be used by children aged 8 years and above and persons with reduced physical, sensory, or mental capabilities, or
lack of experience and knowledge if they have been given supervision or instruction concerning use of the appliance in a safe way and
understand the hazards involved. Children should be supervised to ensure that they do not play with the appliance.
§
Ice is slippery. Maintain counters and floors around dispenser in a clean and ice-free condition.
§
Ice is food. Follow recommended cleaning instructions to maintain cleanliness of delivered ice.
Configuration
Application
S RIDE™
(RIDE remote
ice delivery
equipment)
T Top-mount
425 up to
425 lbs
(193 kg)
710 up to
675 lbs
(306 kg)
1010 up to
1061 lbs
(482 kg)
1410 up to
1466 lbs
(665 kg)
1810 up to
1790 lbs
(812 kg)
2110 up to
2039 lbs
(925 kg)
V Vision™
H Harmony™
B Ice storage bin
J Drop-in
M Ice Manager
diverter valve
system
P Cornelius Profile
PR150
Condenser
Series
Voltage
Icemaker
C 208-230/60/1 (icemaking head)
Self-contained only.
D 115/60/1 (icemaking head)
Self-contained and remote. If remote
unit, high side is 208-230/60/1.
E 230/50/1 (icemaking head)
Self-contained only.
F 115/60/1 (icemaking head)
Remote only. High side is
208-230/60/3.
MC Maestro™
Chewblet
®
(425 Series)
HC Horizon
Chewblet
(710, 1010,
1410, 1810,
2110 Series)
HM Horizon
Micro Chewblet
HC
1810
D
S
V
A
A Air-cooled, self-contained
W Water-cooled, self-contained
R Air-cooled, remote condensing unit
N Air-cooled, no condensing unit for
connection to parallel rack system
Chewblet
®
Ice Machine Model Number Configurations