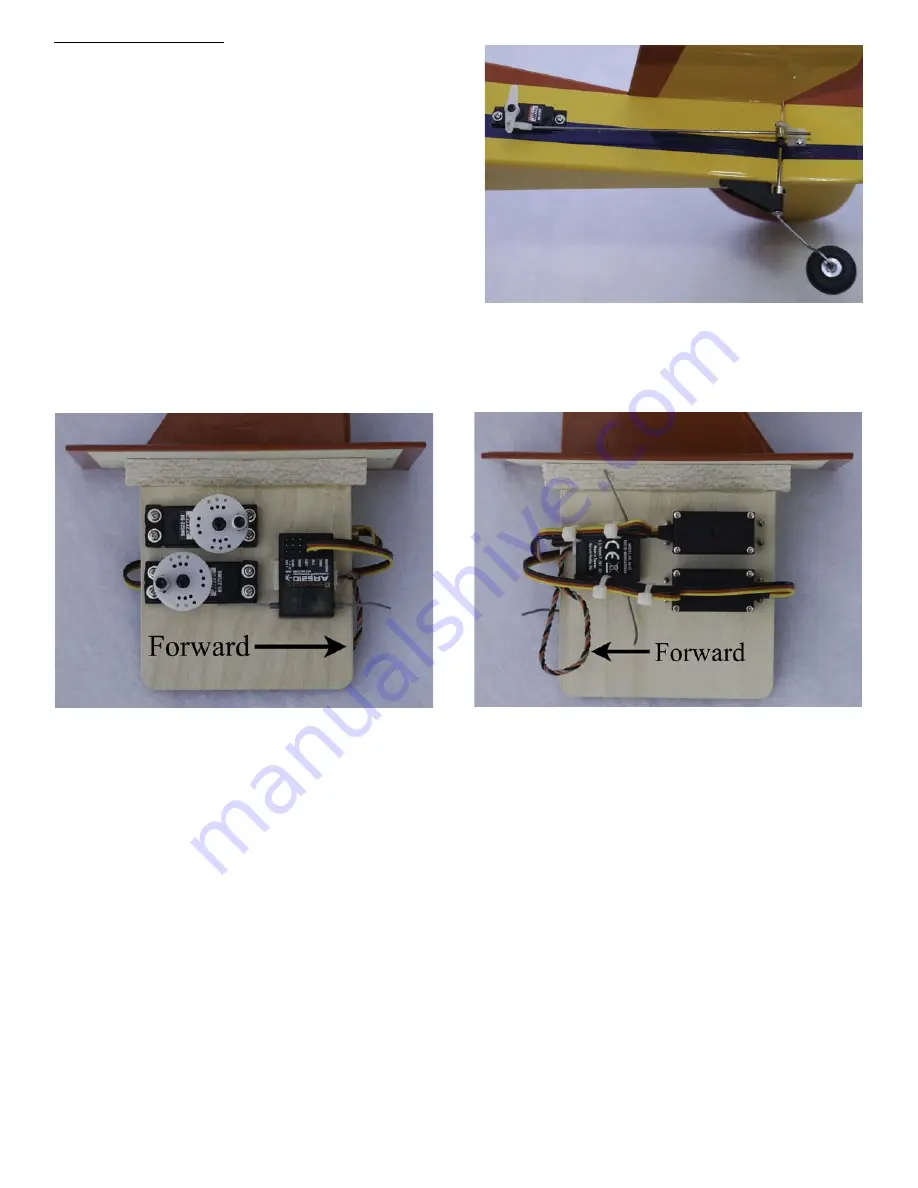
Radio Installation:
39)
The rudder servo and connecting hardware is installed
next. The servo mount is cut to fit a Hitec HS-85 servo.
Simply install the rubber grommets and brass eyelets
supplied with the servo and secure with the screws
included with the servo. The plywood mount is already
pilot drilled for the screws. Install the EZ connector on
the rudder horn making sure the set screw points DOWN.
Bend a 1/4” leg on one end of the 1/16” wire rudder
pushrod. Insert the bent end into the outer hole of the
rudder servo arm and secure with the Du-Bro nylon
keeper. Insert the other end of the rudder pushrod through
the EZ connector on the rudder horn. With the servo
centered at neutral and the rudder also secured in the
neutral position, drill holes for the rudder horn making sure the center line of the EZ connector is directly over
the rudder hinge line. Secure the rudder horn to the rudder. Travel adjustments will be covered in a later step.
Figure 1
Figure 2
40)
The pylon assembly is semi-self contained. There are only two connections external to the pylon assembly,
the rudder servo and the ESC. The servo cutouts in the pylon core are sized and located for the recommended
Hitec HS-225mg servos. If you decide to use servos other than HS-225mg's, you will need to make sure the
linkage geometry is correct to prevent binding. The upper servo is for roll control and the lower servo is for
pitch control. Simply install the rubber grommets and brass eyelets and then using the screws supplied with the
servos, attach the servos to the pylon as shown in Figure 1 above. The holes are already pilot drilled for the
screws. The prototype used a Spektrum AR6210 receiver. Both the main and remote receivers are attached
using double sided foam tape squares. Ensure both receivers are high enough on the pylon to clear the lower
pylon support in the fuselage. Form loops in the excess servo lead wires are secure with small ty-wraps. Figures
1 and 2 above show how the prototype was done. Use the large round servo wheel that come with the servos.
The smaller straight servo arms could possibly flex under flight loads. You will need to remove the servo wheel
from the servo to install the EZ connectors. Use the center hole in the group of 3 servo wheel holes as shown in
figure 1. The EZ connector shaft measures .092” so the holes in the servo wheel need to be reamed to fit the
connector. Either a #42 or 3/32” drill bit will work. Insert the connector into the servo wheel and secure with the
locking washer. An easy way to drive the washer onto the connector shaft is to use a small 1/4” drive “deep”
socket
and carefully hammer the lock washer onto the shaft. Go slow and carefully because this is a 'one time'
try. The lock washer is not re-usable. Do not hammer the washer down so tight that the EZ connector will not
rotate.
16