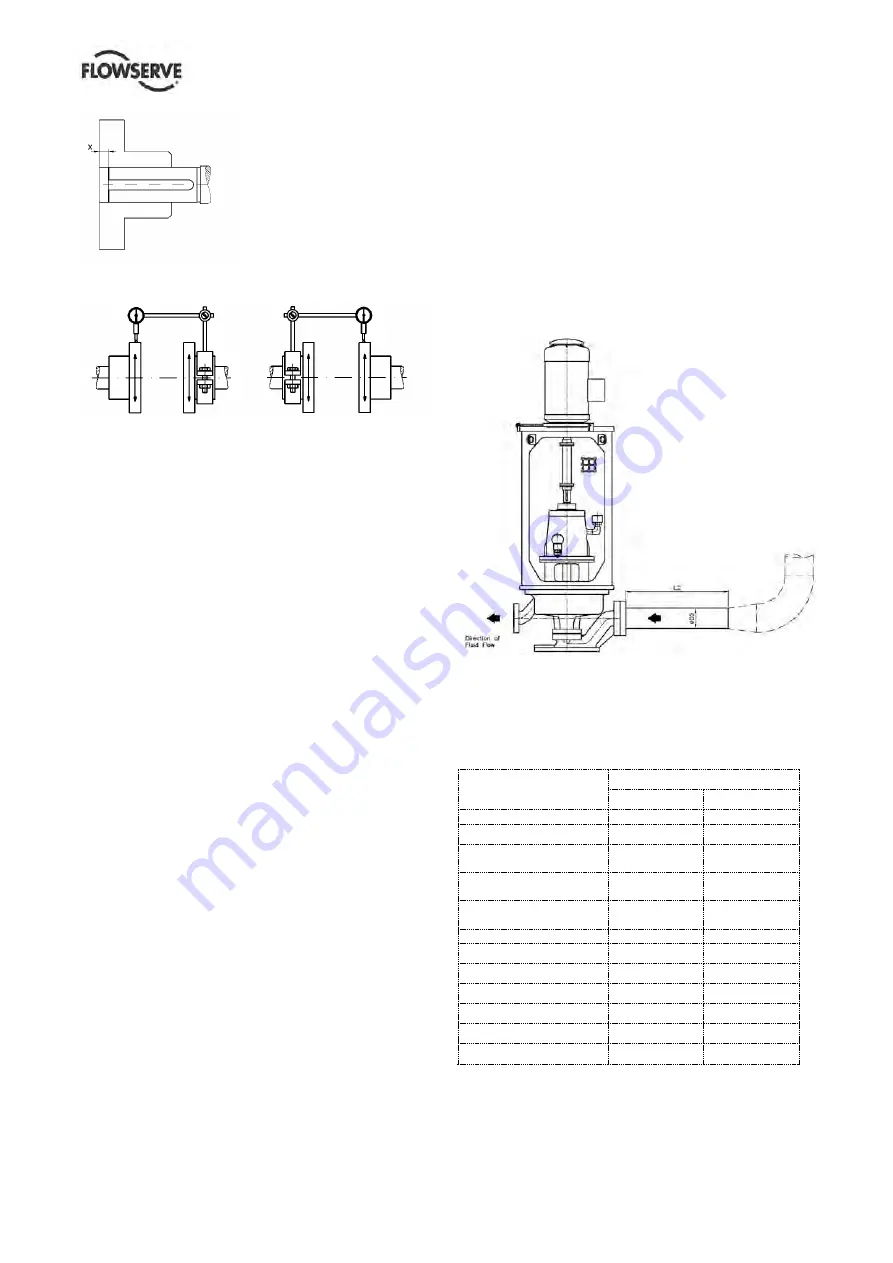
HWMA2 USER INSTRUCTIONS ENGLISH - 06/16
Page 15 of 39
How the alignment of the coupling should be done
you can see on the sketches and explanations below!
a)
b)
a) Fix the dial gauge on the driven shaft and check
the concentricity by turning of both hubs; correct it if
necessary.
b) Fix the dial gauge on the driving shaft and check
the concentricity by turning of both hubs; correct it if
necessary.
If the pump is handling hot liquid, the alignment must
be rechecked in warm condition of the unit.
4.5 Piping
4.5.1 General
Protective covers are fitted to the pipe connections to
prevent foreign particles entering during
transportation and installation. Ensure that these
covers are removed from the pump before connecting
any pipes.
Maximum forces and moments allowed on the pump
flanges vary with the pump size and type. To
minimize these forces and moments which may
cause misalignment, hot bearings, worn couplings,
vibration and a possible failure of the pump, the
following points shall be strictly followed:
a) Prevent excessive external pipe load.
b) Do not connect piping by applying external force
(use of wrenches, crane,...). Piping shall be
aligned without residual stress.
c) Do not mount expansion joints so that their force,
due to internal pressure, acts on the pump flange.
Fitting an isolator and non-return valves can allow
easier maintenance. Never throttle pump on suction
side and never place a valve directly on the pump
inlet nozzle.
A non-return valve shall be located in the discharge
pipework to protect the pump from excessive back
pressure and hence reverse rotation when the unit is
stopped.
Piping and fittings shall be flushed before use. To
avoid damages of the pump install a Y-strainer or a
strainer of 40 mesh.
Piping for corrosive liquids shall be arranged to allow
pump flushing before removal of a unit.
4.5.2 Inlet Piping Requirements *
Inlet flow disturbances, such as swirl, unbalance in
the distribution of velocities and pressures, and
sudden variations in velocity can be harmful to the
hydraulic performance of a pump, its mechanical
behavior, and its reliability.
The minimum required straight pipe length (L2)
before pump suction inlet is specified in Table 01.
The straight pipe section is to be the same diameter
as that of the pump suction nozzle.
Table 01
Fitting*
Number of pipe diameters (ØD2)
Long radius ** Short radius **
90° elbow
4
5
Reducing elbow with
<30% area reduction
3
4
Reducing elbow with 30
to <50% area reduction
2
3
Reducing elbow with
>50% area reduction
0
1
Reducers
Concentric
Eccentric
-) 1 pipe size reduction
0 (<10°)
0 (<20°)
-) 2 pipe size reductions
0 (<20°)
1 (<30°)
-) 3 pipe size reductions
1 (<20°)
2 (<30°)
-) 4 pipe size reductions
2 (<20°)
3 (<40°)
-) 5 pipe size reductions
3 (<30°)
4 (<40°)
* excerpt from ANSI/HI 9.6.6-2009
** according to ASME B16.9-2003