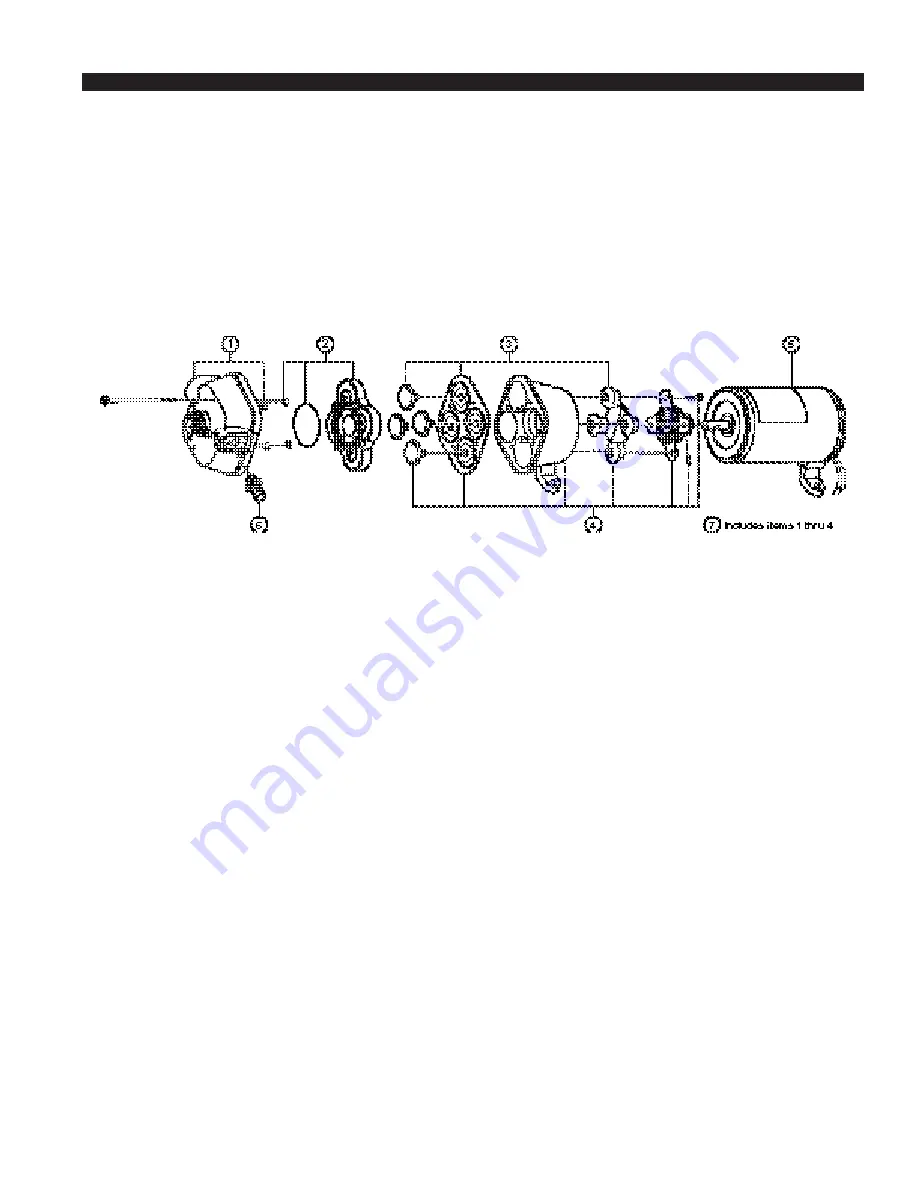
DISASSEMBLE
Upper Housing
1. Loosen but do not remove four pump head screws and
carefully remove upper housing assembly (1)
2. Inspect check valve (2) for debris
3. Reassemble new upper housing (1)
Check Valve Assembly
Follow step 1
3. Replace check valve (2)
4. Reassemble upper housing (1)
Lower Housing, Diaphragm, Motor
Follow step 1, then slide rubber foot from mounting track.
3. Rotate kmw housing (4) so mounting notch opening on lower
housing exposes set screw which holds bearing housing to
shaft
4. Loosen this set screw by inserting wrench 1/8” Allen wrench
into mounting notch opening. Then, slide lower housing (4) off
motor shaft.
Diaphragm Cont’d
5. Loosen four cam piston screws with Philfips head screw
driver and pull apart cam from inner pistons. (Pistons should
always be replaced when a new diaphragm is installed.)
Motor Cont’d
5. Replace Motor (5)
REASSEMBLE
Motor
1. Reassemble lower housing assembly (4) to motor. (Follow
steps 4 to 10.)
Diaphragm
2. Lower housing is assembled with:
• Flat side of diaphragm and outer pistons facing motor
• Hex stem of inner pistons must be aligned into hex holes in
outer pistons (4).
• Outer pistons must be aligned with alignment slots on cam
assembly making sure screw holes align in cam assembly,
otherwise diaphragm will leak
3. Tighten cam piston screws partially, center piston in
diaphragm, Dien tighten screws securely (18 in. lbs. torque)
Lower Housing
4. Reassemble lower housing assembly (4) to motor.
5. Retighten set screw securely. Set screw head must be
positioned facing motor covering seam (indentation).
(Positioning of this screw is critical to avoid misalignment and
subsequent diaphragm damage.)
Upper Housing, Check Valve
6. Reassemble upper housing (1)
7. Properly seat O-Ring in check valve assembly (2) and check
if ferrules and screen are in place on upper housing (1)
8. Install check valve (2) into upper housing (1) and push in.
9. Assemble on to lower housing (4), align 4 screws on to motor
by rotating lower housing (4) if necessary to align feet
10. Tighten screws evenly to 30 in. lbs. torque.
TROUBLESHOOTING
WARNING:
BEFORE SERVICING PUMP, TURN OFF PUMP AND DRAIN WATER FROM SYSTEM!!
Failure to Prime -
Motor operates, but no pump discharge
• Restricted intake or discharge line
• Air leak in intake line
• Debris in pump
• Punctured pump diaphragm (pump leaks)
• Crack in pump housing
Motor falls to turn on
• Blown fuse
• Loose wiring connection
• Pump circuit has no power
• Defective motor
Low Flow and Pressure
• Air leak at pump intake
• Accumulation of debris inside pump and plumbing
• Worn pump bearing (excessive noise)
• Punctured pump diaphragm (pump leaks)
• Defective motor
Pulsating Flow
• Restricted pump delivery. Check discharge lines, fittings and
valves for clogging or undersizing.
Quite often when a pump is worn or defective the one failed component has overburdened others. To avoid frequent aggravating
repairs, Flojet offers service kit assemblies making repairs as quick and easy as possible.