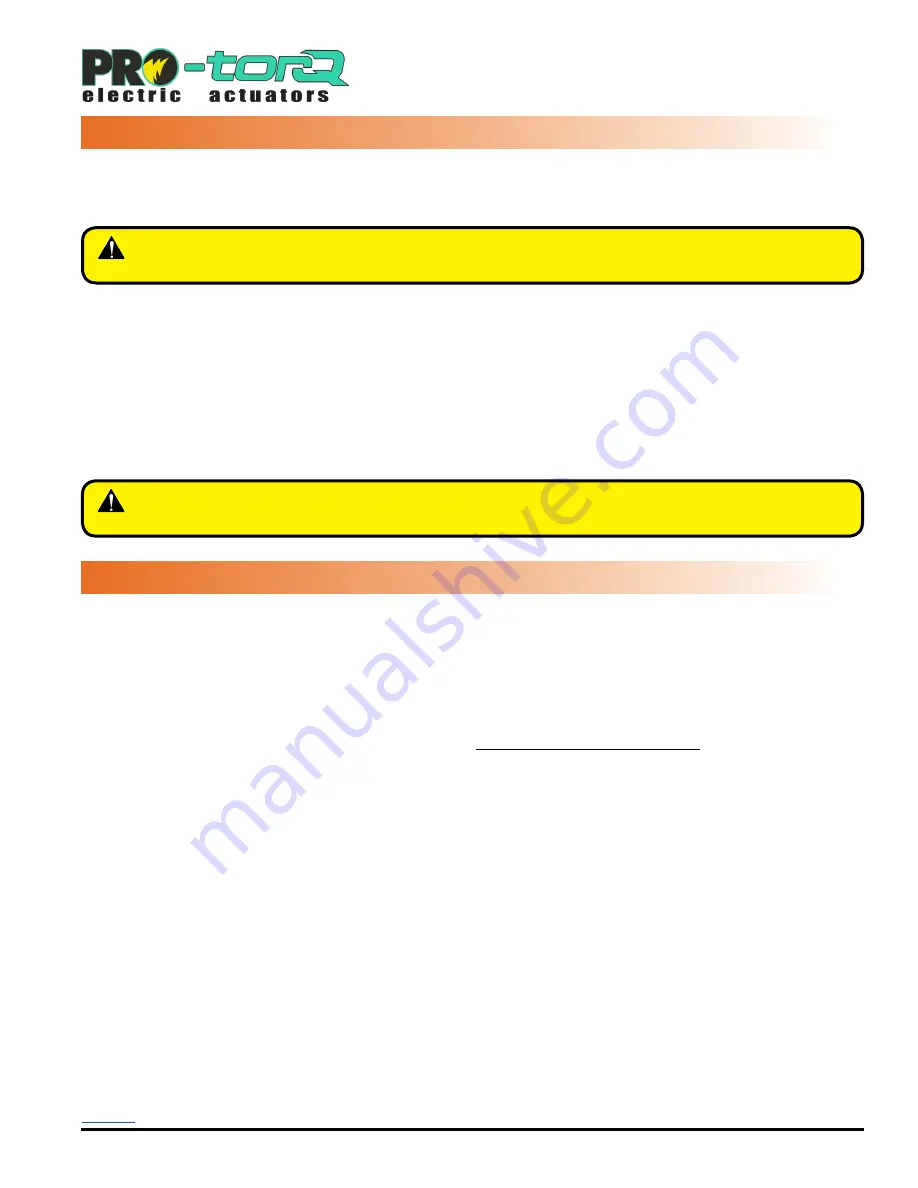
The end stop travel (cams) of this actuator have been factory set and tested to respond between 0° and 90°
degrees rotation . If NO changes to end stops are required, this unit is ready to be put into service immediately
using this procedure . IF changes to the cam positions are required, refer to pages 8 ~ 10 before proceeding .
WARNING –
Serious Damage to the actuator will result if the motor is allowed to drive the gear train
into the mechanical stop! Remove power from this device BEFORE making any travel adjustments.
WARNING –
Follow these directions carefully and in order. Actuator damage due to improper testing
and commissioning will NOT be covered under warranty.
Calibration Procedure - On/Off Control
1. Apply correct power according to the actuator model, referring to wiring diagrams.
2. Position the actuator to its full CCW (Open) and/or CW (Closed) positions and adjust the cams as necessary.
3. After making cam adjustments on either or both ends of travel, it is advisable to move off cam slightly, and then
repeat the drive command to assure the cam settings are correct.
4. Be sure the cam setscrews are snug (overtightening during calibration will make it diffi cult to make minor
incremental adjustments).
5. Unit is now calibrated and is ready to be put into service. No other calibration is necessary.
Commissioning Procedure - On/Off Control
1. Utilize the handwheel or override shaft to rotate the actuator and damper, valve or other connected device through
its full travel from full CW to full CCW and back again to check for any possible interference. Do NOT utilize any
mechanical advantage devices to rotate the handwheel (pipes, wrenches, extension bars, etc.).
2. Manually position the actuator to its mid-stroke position.
3. Apply correct power to the unit.
4. Measure correct power and polarity on terminals 1 & 2 AT THE MAIN TERMINAL BLOCK.
5. Command the fi eld device to generate a CCW signal. The actuator rotates in a CCW direction (as viewed from above).
6. Measure terminals 2 and 6 (Run CCW) for correct voltage (matching that measured in step 4).
7. Actuator will stop when it reaches it’s full CCW position.
8. With fi eld command signal still present, measure terminals 2 and 5 and read voltage to match that measured in
step 4.
9. Read continuity between terminals C & D to show the CCW Aux switch is closed.
10. Command the fi eld device to generate a CW signal. The actuator rotates in a CW direction (as viewed from above).
11. Measure terminals 2 and 4 (Run CW) for correct voltage (matching that measured in step 4).
12. Actuator will stop when it reaches it’s full CW position.
13. With fi eld command signal still present, measure terminals 2 and 3 and read voltage to match that measured in
step 4.
14. Read continuity between terminals A & B to show the CW Aux switch is closed.
15. Generate a mid-position signal at the fi eld device to move the actuator off its full CW trip position.
16. Return Field control to automatic mode.
17. Actuator is now commissioned and operational.
ON/OFF ONLY
CALIBRATION
COMMISSIONING
USE ONLY FLO-TITE GENUINE REPLACEMENT PARTS
ELo Rev C ECR 044V
Page 1
1
of 28
www.flotite.com