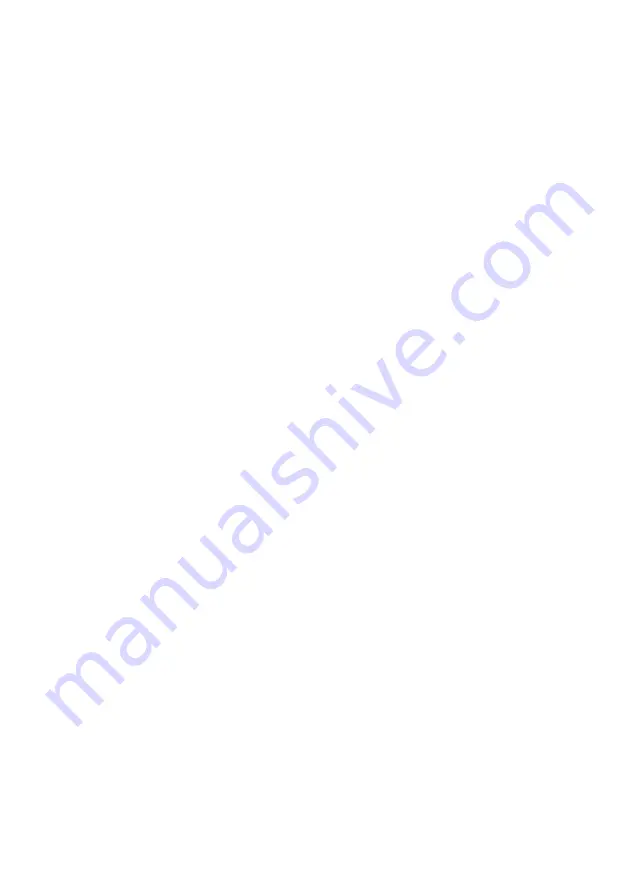
PARTS SHORTLIST
Replacement of any other parts must be carried out by a competent person such
as a GAS SAFE registered gas installer.
The part numbers of the user replaceable parts are as follows, these are available
from specialist spares stockists whose details can be found on our web site,
www.bfm-europe.com, in the ‘stockist’ section.
Fuelbed Set
B-66010
Gas valve
B-135670
ODS Pilot Assy. (NG)
B-66500
Control Knob
B-137500
Injector
B-66390
Due to our policy of continual improvement and development the exact
accuracy of illustrations and descriptions contained in this book cannot be
guaranteed.
21