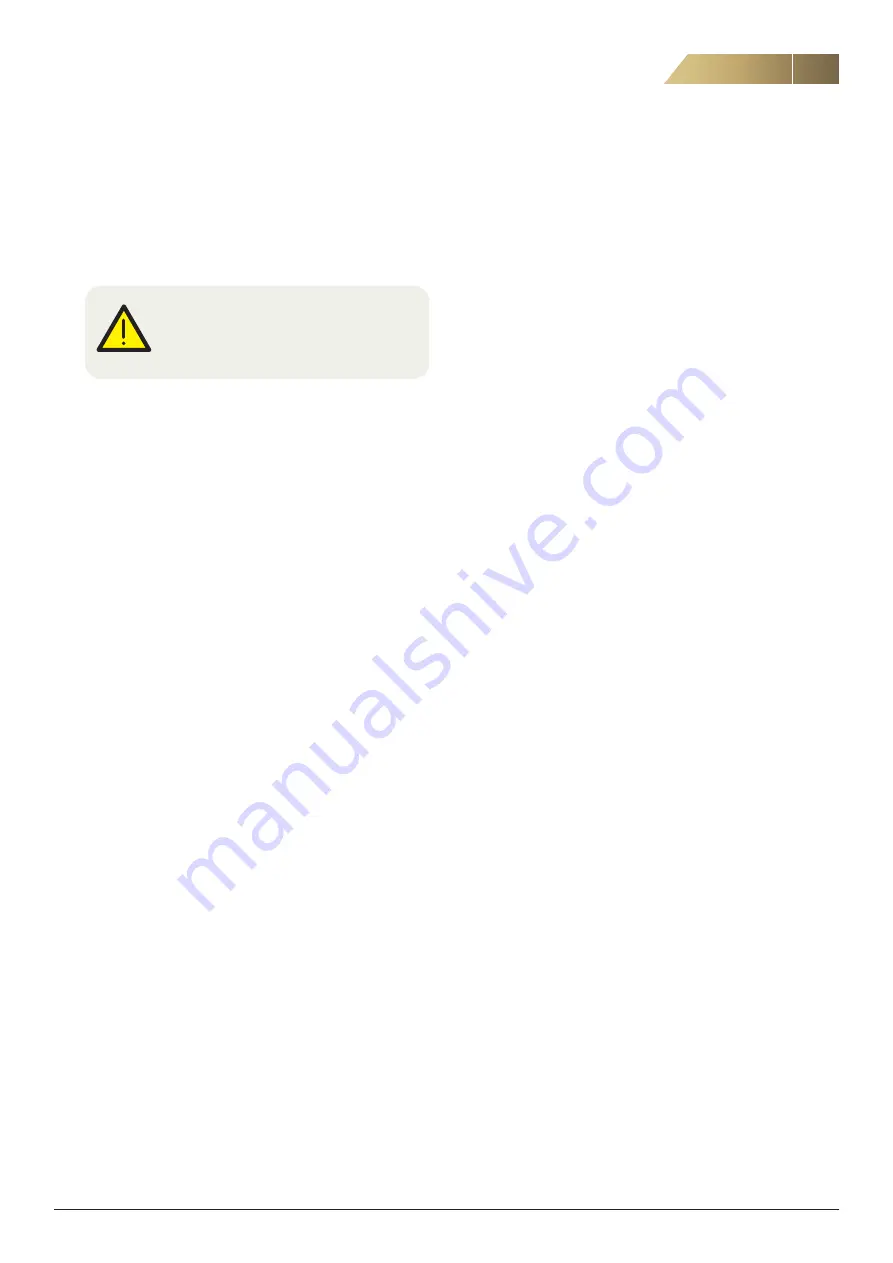
EQKC COMBI COOLER
FläktGroup
DC_8931GB 20180202_R0
We reserve the right to make changes without prior notice
Installation and maintenance instructions
13
OPERATION AND MAINTENANCE
Inspecting the sight glasses
• The cooling unit is part of the air handling unit and is installed
as a unit module
• The cooling unit operates independently and has its own
control cabinet. Start signals are provided by the air handling
unit.
• The cooling unit is intended to cool supply air in the tempera-
ture range +20 °C - +32 °C. Lowering the temperature of the
brine by 5–7 °C is possible depending on the selected air
temperature, supply air/extract air ratio and operational case.
Inspecting the sight glasses
The cooling unit’s service component has an electrical appara-
tus cabinet generally containing the following equipment:
• Main circuit breaker
• Control circuit fuse
• Motor circuit breaker
• One frost protection sensor for each circuit
• Control unit with display
The service component also contains sections of the piping
that distributes the brine (the cold water) to the supply air coil
and chilled beam circuit. The illustration below shows the
components in the service compartment, the components
included in the delivery, and the components required to allow
the entire cooling unit to be utilised fully.
INSPECTION
(Carried out by the owner/user once a week) Check (look/
listen for) the following:
1. Alarm indications
2. Abnormal noise/vibrations
3. Fluid leakage (oil, water)
4. Corrosion, wear
5. Mountings, brackets
6. Unit compartment, lighting
MAINTENANCE
(Must be carried out by a refrigeration service company or
corresponding undertaking at least once a year).
Check the following:
1. Evaporation/condensation temperature. Leakage inspection
(every 12 months) in accordance with EU requirements.
2. Hot vapour temperature.
3. Expansion valve (superheating of suction vapour).
4. Safety equipment (pressure switch trip function).
5. Cooling capacity.
6. Automation and control equipment (functional inspection)
7. Electrical equipment (post-tightening power connection).
8. Cleaning (batteries, drip trays, drains).
9. Outlet filters.
Water circuit
10. Cleanliness and effectiveness of all plate heat exchangers
(evaporators, incoming).
11. Filter.
12. Pipe connectors and welds.
13. Pipe insulation.
14. The temperature differential across the heat exchangers is
checked via the control unit. Carried out to check clean-
liness/performance across the exchanger.
IN-SERVICE INSPECTION
Inspections must take place at least once a year and be regis-
tered in accordance with EU regulations on fluorinated green-
house gases 842/2006, Article 3.
Check the following:
1. Pipes
2. Leak trace the refrigerant system
3. Vibration test
4. Corrosion inspection
5. Refrigerant filling
6. Oil leakage
7. Safety equipment
8. Joints/seals
REMOVAL
When removing, (scrapping) this type of unit all refrigerant and
compressor oil must always be taken for destruction/recovery.
TROUBLESHOOTING
NOTE! Faults must always be remedied without delay.
The service/maintenance of cooling and water systems may
only be carried out by authorised companies using certified-
personnel in accordance with European Union Regulation
303/2008 and the necessary protective equipment.
SPARE PARTS
Spare parts can be bought via local cooling suppliers. Contact
your local FläktGroup office for information regarding compo-
nents that need to be replaced.
Important!
Always study the safety instructions on Page 1
prior to carrying ! out any work.