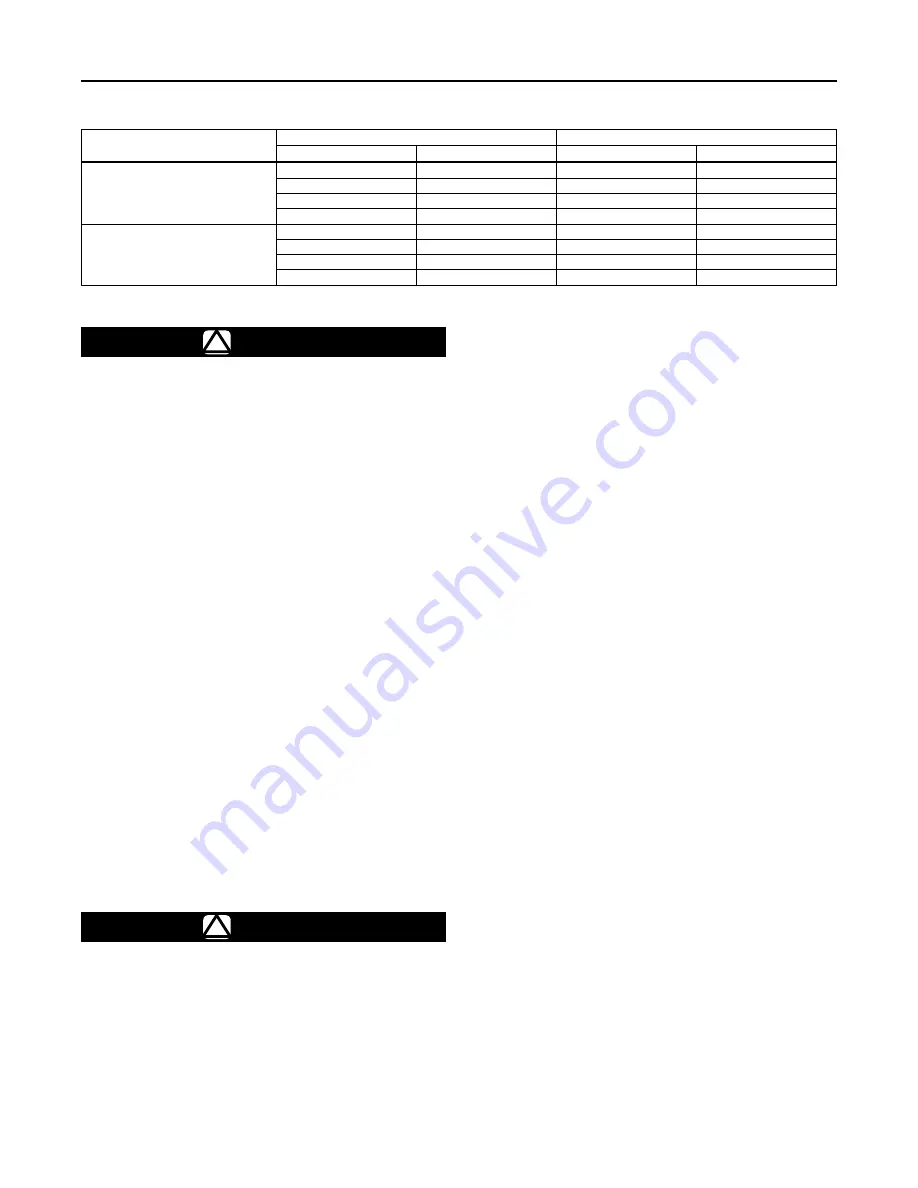
Type MR108
10
!
WARNINg
To avoid personal injury or damage of
internal parts from a pressure-loaded
actuator, carefully vent the regulator spring
case pressure prior to inlet pressure.
4. If the actuator is pressure loaded, vent the
loading pressure slowly to release pressure in the
spring case.
Note
To avoid internal damage due to
reverse pressurization of main valve
components, make certain backpressure
regulator inlet pressure is bled prior to
outlet pressure.
5. Slowly open the downstream vent valve to vent
downstream pressure.
6. Leave the downstream vent valve open to vent
inlet pressure and to release all remaining
pressure in the regulator.
7. If the regulator has the drain valve option, slowly
open valve to drain fluid inside valve body. Make
sure to close valve after fluid has been drained.
Maintenance
!
WARNINg
Personal injury, equipment damage
or leakage due to escaping fluid
may result if seals are not properly
lubricated or maintained. Due to
normal part wear or damage that
may occur from external sources, this
regulator should be inspected and
maintained periodically. The frequency
of inspection, maintenance and
replacement of parts depends upon
the severity of service conditions or
the requirements of local, state and
federal regulations.
Regulators that have been disassembled
for repair must be tested for proper
operation before being returned to
service. Only parts manufactured by
Emerson™ should be used for repairing
Fisher
®
regulators. Restart gas utilization
equipment according to normal
startup procedures.
Note
To protect against reduced performance,
ensure vents are not plugged when
conducting routine maintenance.
Annual Maintenance
The stem O-rings on the Type MR108 actuator can be
lubricated during regularly scheduled maintenance,
using the grease fitting (key 44). Stem O-rings can be
checked for damage during normal operation. If line
pressure leakage or unexpected grease extrusion from
the actuator vent (key 26) is observed during normal
operation the stem O-ring needs to be replaced.
Change Nameplate
Be certain that the nameplates are updated to
accurately indicate any field changes in equipment,
materials, service conditions or pressure settings.
Table 6.
Type MR108 Trim Weights
TyPE
BODy SIZE
TRIM WEIgHT
NPS
DN
lbs
kg
MR108 Low-Pressure Actuator
1
25
74
34
2
50
79
36
3
80
93
42
4
100
113
51
MR108 High-Pressure Actuator
1
25
63
29
2
50
69
31
3
80
83
38
4
100
102
46