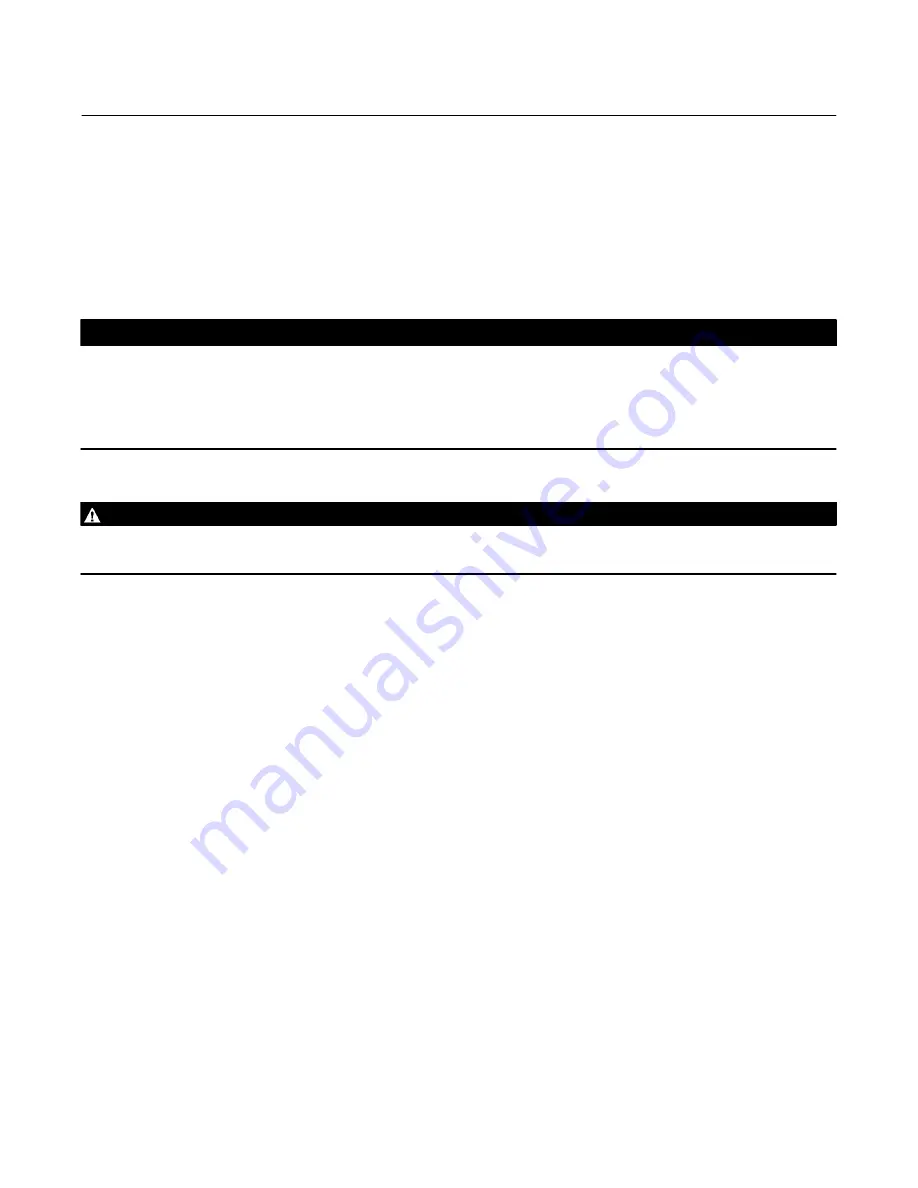
Instruction Manual
D100392X012
EH Valves NPS 8 through 14
June 2017
14
5. After lapping, again disassemble as necessary, clean the seating surfaces, reassemble, and test for shutoff. Repeat
the lapping procedure if necessary.
Trim Replacement
After all trim maintenance has been completed, reassemble the valve by following the numbered steps below. Be
certain that all gasketed surfaces are clean. Key numbers referenced in this procedure are shown in figure 12 for the
EHD valve and in figure 14 for the EHT valve.
CAUTION
Thoroughly clean the seat ring (key 6), the seat ring cap screws (key 7), and the cap screw threads in the valve body with a
good‐quality degreaser. Unless the valve is to be used for oxygen service, thoroughly lubricate the cap screw threads and
the underside of the cap screw heads with one of the lubricants (or equivalent) shown in table 7.
Failure to lubricate as described may cause galling and improper seat ring gasket or O‐ring (key 12) loading which may
result in leakage.
WARNING
If the control valve is to be used for oxygen service, use the lubrication procedure above, but substitute a lubricant that has
been approved for oxygen service. Use of unapproved lubricants creates a fire or explosion hazard.
1. Install either the seat ring gasket or the O‐ring (key 12). Place the O‐ring in the O‐ring groove in the seat ring before
installing the seat ring in the valve body. Install the seat ring (key 6) and secure it with the seat ring cap screws (key
7). Torque the hex socket head cap screws in a criss‐cross pattern with no more than 20 N
S
m (15 lbf
S
ft) of torque.
When all are tightened to 20 N
S
m (15 lbf
S
ft), increase the torque 20 N
S
m (15 lbf
S
ft) without exceeding the torque
2. Install one of the cage gaskets (key 11) between the valve body and cage (key 2), and install the cage.
3. If the cage used has multiple sizes of windows, attempt to orient the largest window toward the valve body web (a
shelf‐like projection of the casting into the flow cavity). As an alternate reference, orient the largest window toward
the process outlet for a flow‐down and toward the process inlet for a flow‐up valve.
4. Inspect the valve plug stem threads for any sharp edges that might cut the packing. Use a whetstone or emery cloth
to smooth the threads if necessary.
5. To install the piston rings or seal ring (key 8), proceed as appropriate:
For an EHD valve,
if installing a new piston ring, the replacement piston ring will arrive in one piece. Use a vise with
smooth or taped jaws to break this replacement piston ring into halves. Place the new ring in the vise so that the jaws
compress the ring into an oval. Slowly compress the ring until the ring snaps on both sides. If one side snaps first, do
not try to tear or cut the other side. Instead, keep compressing until the other side snaps.
Remove any protective tape or covering from the valve plug and stem assembly, and set it on a protective surface.
Then place the piston ring in the piston ring groove with the fractured ends matched.
For an EHT valve,
install the seal ring (key 8) onto the valve plug (key 3). Install the ring with the open side facing the
seat ring end of the valve plug for a flow‐down application (view B of figure 14) or with the open side facing the valve
stem end of the valve plug for a flow‐up application. Slide the backup ring (key 9) onto the valve plug. Secure with the
retaining ring (key 10). For an EHT valve with a Whisper Trim Level D cage, install the piston ring (key 30, figure 14)
using the procedure given in the EHD instructions immediately preceding this paragraph.