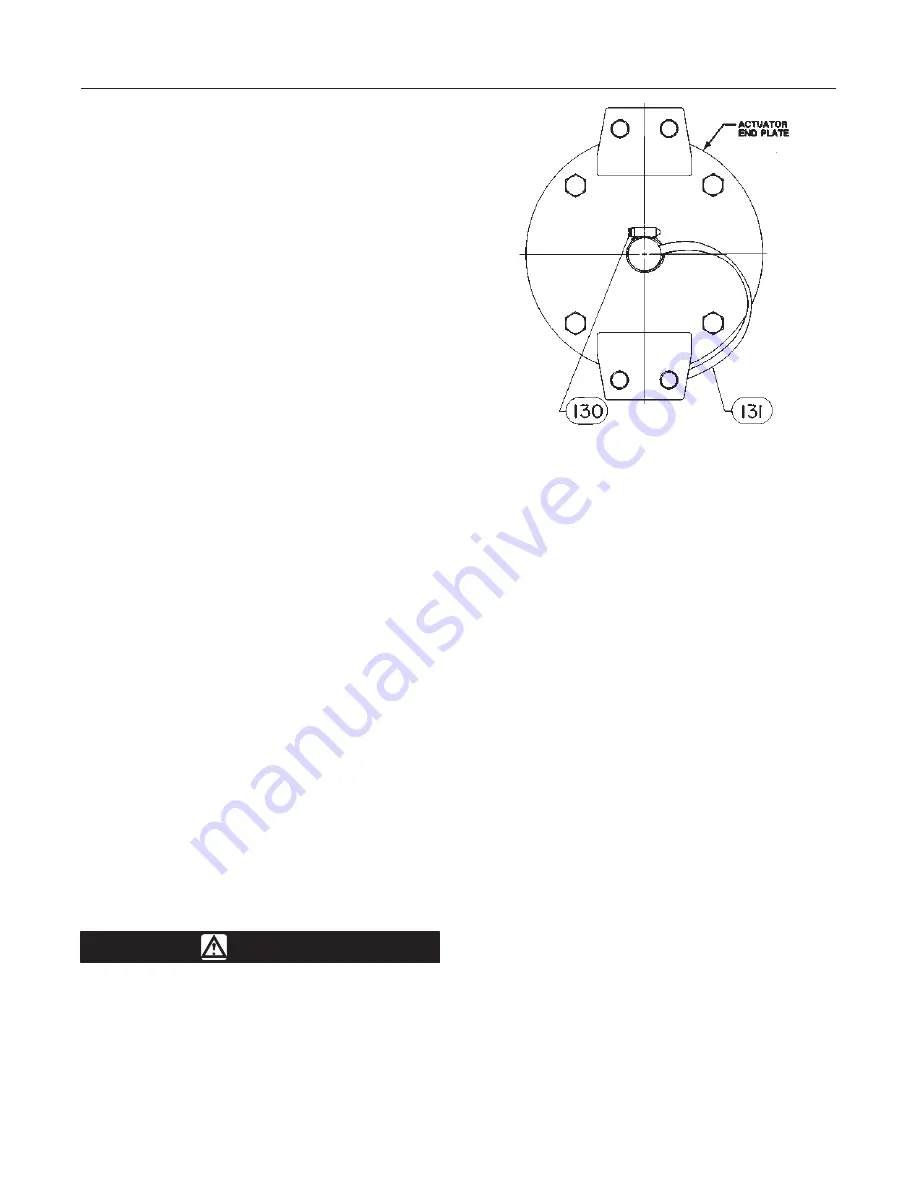
Type 9500
4
O-rings on the liner faces. Leakage through the
flange connections and damage to the liner could
result if the partial O-ring faces are not properly
supported.
The 6 to 10-inch sizes must not be used with slip-on
flanges unless flange adaptors are used to support the
liner. When using slip-on flanges with other sizes, be
certain the valve is carefully centered to ensure that the
partial O-ring faces are in full contact with the adjacent
flanges.
c. When a flange adpater is necessary, a flange
gasket must be installed between the line flange
and the flange adapter. Do not use a flange gasket
between the valve and the flange adapter. Addition-
al gasketing material at this location could damage
the liner.
d. The valve disk must be in the closed position
when the valve is being inserted into the pipeline. If
the valve disk is not closed, it could be damaged
against the mating piping or flanges.
6. Insert the valve into the pipeline. Insert four flange
studs or bolts through the flanges to support the valve.
7. Center the valve carefully on the flanges by mea-
suring equal distances at the top and bottom and
equal distances at the sides.
8. Insert the remaining flange studs or bolts. Tighten
the studs or bolts evenly. Normal flange bolt torques
may be used because liner compression is limited by
metal-to-metal contact between flanges and the valve
body.
9. Rotate the valve disk manually to be certain the
disk clears the adjacent piping or flanges as it opens.
If necessary, disconnect the power actuator-valve link-
age, but do not disturb the adjustment of the turn-
buckle or adjustable linkage. If the disk hits the flange,
loosen flange bolting temporarily while re-centering the
valve. If the problem cannot be corrected in this man-
ner, it will be necessary to use line flanges with larger
inside diameters adjacent to the valve.
10. For hazardous atmosphere or oxygen service
valves, read the following Warning, and provide the
bonding strap assembly mentioned below if the valve
is used in an explosive atmosphere.
WARNING
The valve drive shaft is not necessarily
grounded to the pipeline when installed.
Personal injury or property damage
could result, if the process fluid or the
atmosphere around the valve is flam-
mable, from an explosion caused by a
Figure 4. Grounding Assembly
37A6528-A/DOC
discharge of static electricity from the
valve components. If the valve is
installed in a hazardous area, electrical-
ly bond the drive shaft to the valve.
Note
The packing is composed of all conduc-
tive packing rings (graphite ribbon
packing) or partially conductive packing
rings (carbon-filled PTFE female adaptor
with PTFE V-ring packing or graphite-
composition packing ring with PTFE/
composition packing) to electrically
bond the shaft to the valve for hazard-
ous area service. For oxygen service ap-
plications, provide alternate shaft-to-
valve body bonding according to the
following step.
11. Attach the bonding strap assembly (key 131, fig-
ure 4) to the shaft with the clamp (key 130, figure 4).
12. Connect the other end of the bonding strap as-
sembly to the valve flange cap screws.
Adjustments
Hub Seals
Key number locations are shown in figure 7.
Thrust sleeve assemblies (key 6) seal the disk hubs.
In time, especially with frequent valve disk rotation,
these seals may require adjustment.