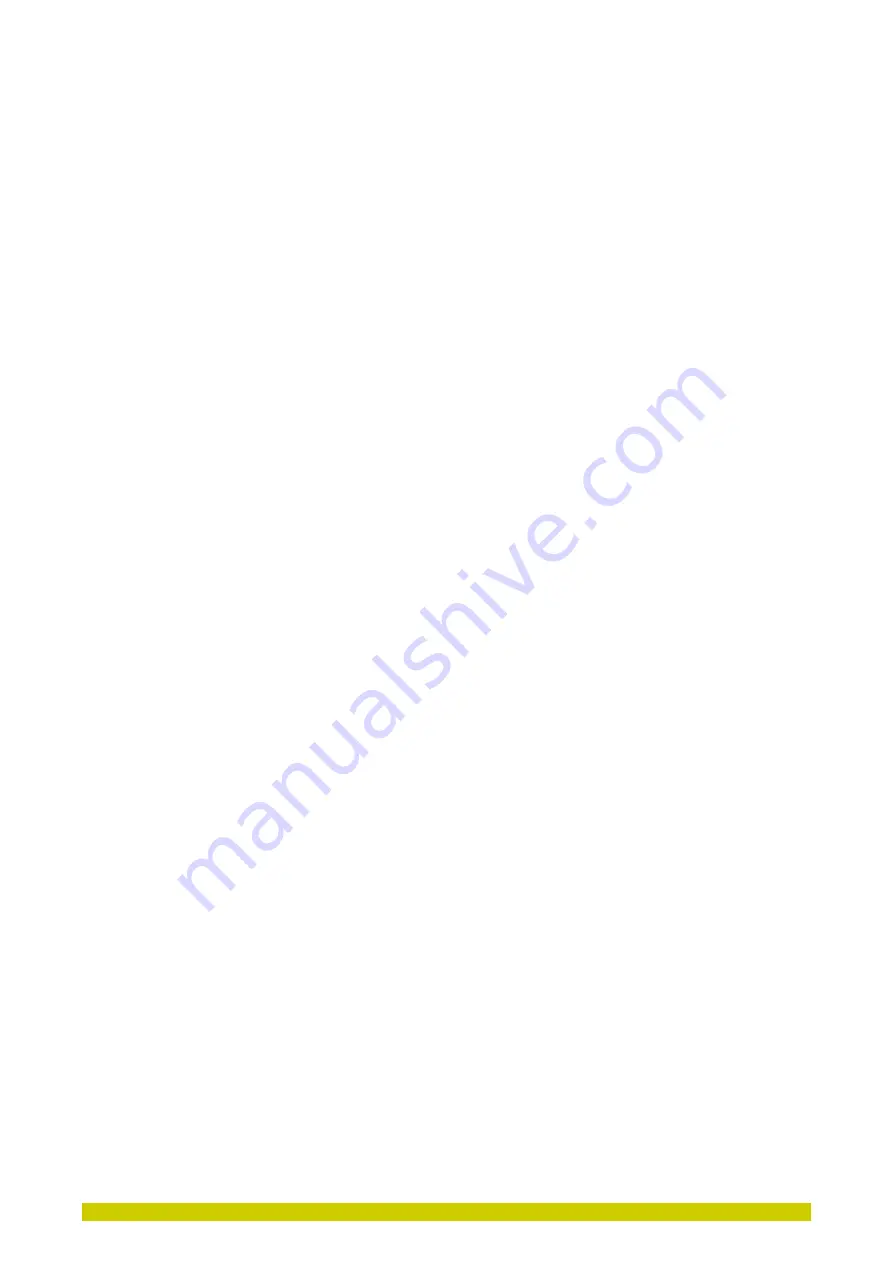
Chemicar Europe NV - Baarbeek 2 - 2070 Zwijndrecht - België/Belgium
4
STARTING UP
Before starting-up the tool ensure that
• The packaging is complete and does not show signs of having been damaged during storage or
transport;
• The tool is complete; check that the number and type of components comply with that reported in
this instruction booklet;
• The power supply and socket outlet can support the load reported in the table and that indicated
on the tool identification plate reproduced.
ASSEMBLING THE TOOL
•
Position the handle (7) on the gearbox such that the holes foe mounting the screws(9) are aligned
with those on the gearbox.
MOUNTING THE BACKING PLATE
•
Pace the backing plate (10) with the screw (4) in the centre (fig.1);
•
Slightly turn the backing plate (10) until it is fixed to the screw as in fig 2;
•
Tighten the screw using the supplied Allen wrench (5) (fig.4).
• Do not tighten the backing plate screw if it is in the wrong position;
• To remove, follow the same procedure in reverse order; assemble the buffer pad on the Velcro
surface of the pad.
ASSEMBLING THE BUFFING PAD
•
Press the buffing pad to attach it to the disc pad.
BEFORE STARTING THE TOOL
Ensure that:
• The power supply conforms with the characteristics of the tool;
• The power supply cable and plug are in perfect condition;
•
The ON/OFF switch works properly though with the power supply disconnected;
• All the parts of the tool have been assembled in the proper manner and that there are no signs of
damage;
• The ventilation slots are not obstructed.
STARTING AND STOPPING
•
Starting: push the lever of the switch (2) towards the body of the tool; if the tool is to be locked
in the ON position, press button (13) at the same time and keep it pressed while releasing lever
(2), thus locking the switch.
• Stopping: release the lever of the switch or, if locked in position. Push the lever to release the
lock button.
TEST RUN
Start the tool and check that there are no unusual vibrations, or no mismatching of the buffing pad.
Otherwise switch-off the tool immediately and eliminate the fault.
ELECTRONIC RPM REGULATION
The rpm can be adjusted by rotating the wheel (3). The choice of speed depends on the characteristics of
the buffers and the material to be worked.
REPLACING THE BUFFING PAD
Pull the used pad off and apply the new one, pressing it onto the disc pad.
MAINTENANCE
All maintenance operations are carried out with the power supply disconnected.
At the end of each work session, or when required, remove any dust from the body of the tool using a
jet of compressed air, paying particular attention to the motor ventilations slots. No other maintenance
operations must be undertaken by the user.
Maintenance and cleaning of the inner parts, like brushes, ball bearings, gears etc. or others, must be
carried out only by an authorised customer service workshop.