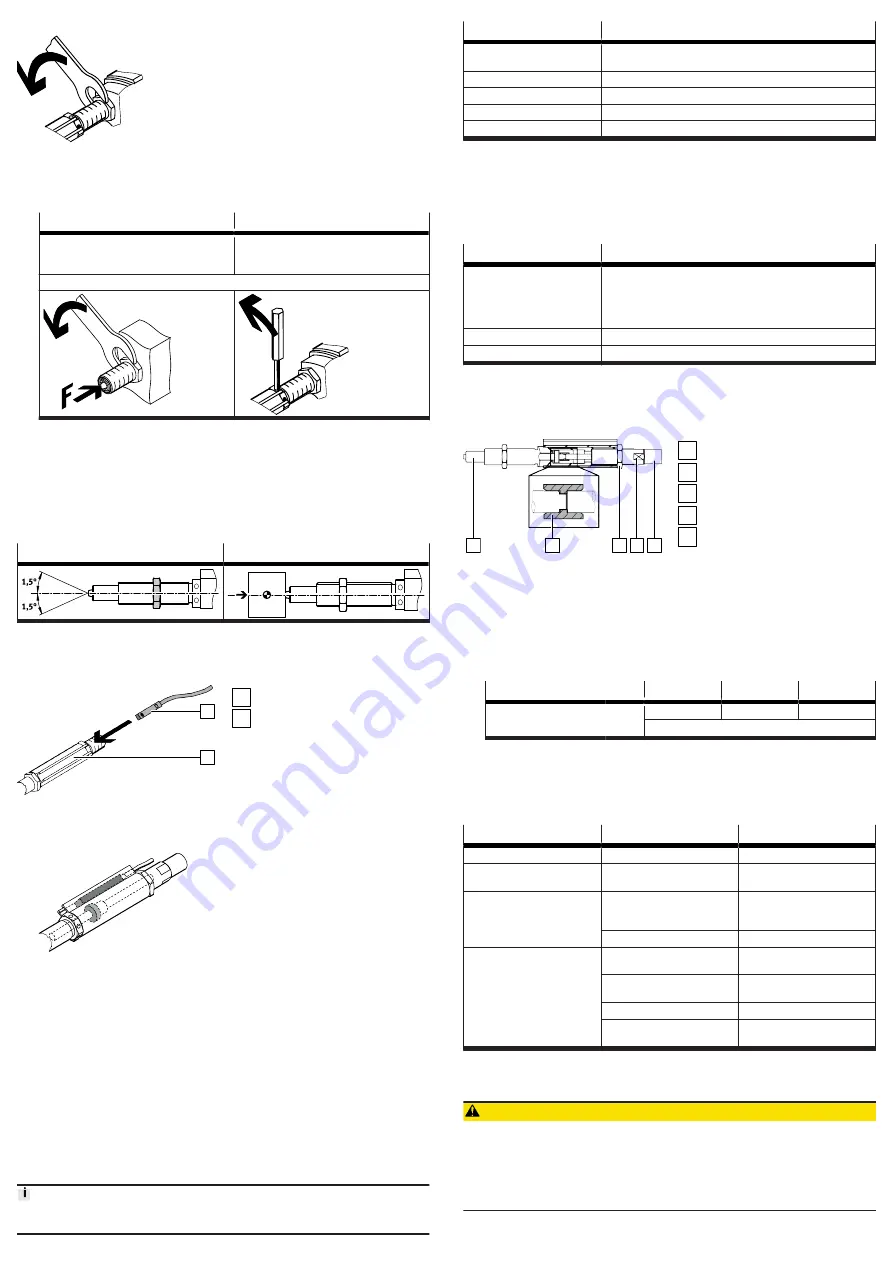
Adjusting product
Fig. 3: Loosen lock nut
1. Position the mass to be cushioned at the intended end position.
2. Loosen the lock nut on the side of the cross-hole nut.
3. Adjust the position of the stop element in accordance with the mounting.
When mounting in drilled hole
When mounting in thread
Turn the loaded lock nut in the desired direc-
tion. If necessary, hold the stop element
against the cross-hole nut.
Turn the cross-hole nut in the desired direc-
tion.
One revolution corresponds to approx. 1 mm stroke change.
4. Fix the position of the stop element. At the same time, tighten the lock nut on
the side of the cross-hole nut.
5.1
Mounting
5.2
Aligning product
–
Observe the axial direction of force of the moving mass to the axis of the shock
absorber.
–
The mass must contact the piston rod over a wide area.
Force direction, max. deviation
Alignment of the mass
Tab. 5: Permissible axial force direction and alignment of the moving mass
5.3
Mounting accessories
Mounting optional proximity switch
4
12
Fig. 4: Mounting proximity switches
4
Slot for proximity switch
12
Proximity switch (optional)
•
Place the proximity switch in the slot and fasten it in accordance with the end
position of the shock absorber.
6
Commissioning
6.1
Executing test run
1. Start the test run at the drive at reduced velocity.
2. If necessary, readjust the position of the stop element.
3. Gradually increase the velocity of the drive to the operating value in steps.
Ä
If set correctly, the end position is reached without a hard stop.
With hard stop:
–
Reduce the impact velocity if necessary.
–
Check function and design of the stop element.
6.2
Notes on operation
Energy absorption
•
Only use the shock absorber within the permissible range of 25% to 100% of
the maximum energy absorption
Recommendation: use the shock absorber within the optimum range from
50% to 80% of the maximum energy absorption.
Energy absorption
Note
0 … 25%
Unfavourable; fluid leakage at the shock absorber may be
increased
25 … 50%
Permitted
50 … 80%
Optimal
80 … 100%
Permitted
>
100%
Impermissible
Tab. 6: Energy absorption of the shock absorber
Cushioning effect
The viscosity of the hydraulic fluid declines over its operating life due to the
generated friction heat. This can reduce the cushioning effect.
7
Maintenance
Maintenance interval
Maintenance work
Every 2 million load changes
Check shock absorber:
–
sealing, no fluid leakage
–
Cushioning distance s
In case of leakage, hard stop or cushioning distance too short:
replace shock absorber.
Every 5 million load changes
Replace rubber buffer.
Every 10 million load changes
Replace shock absorber.
Tab. 7: Maintenance schedule
The hydraulic fluid in the shock absorber cannot be topped up or changed.
The shock absorber cannot be repaired.
7.1
Replacing shock absorber
1
2
3
11
6
Fig. 5: Replacing shock absorber
1
Shock absorber
2
Spanner flat
3
Nut for securing the shock absorber
6
Stop plunger
11
Connecting clip
1. Release the load on the stop plunger
6
.
2. Loosen the nut
3
on the shock absorber.
3. Unscrew the shock absorber, if necessary with a tool on the spanner flat.
4. If the connecting clip
aA
was removed with the shock absorber, press the
connecting clip on the new shock absorber.
5. Screw in the new shock absorber to the stop.
6. Tighten the nut
3
to the tightening torque.
Size
5
7
8
Nut
3
Tightening torque
[Nm]
2
3
5
Tolerance ± 20%
7. Actuate the stop plunger slowly until it reaches the end position and then
release the load.
Ä
The connecting clip clicks into place.
8
Fault clearance
Malfunction
Possible cause
Remedy
Leakage/fluid leakage
Shock absorber faulty
Replace shock absorber.
Noisy impact at the start of the
stroke
Rubber buffer worn
Replace rubber buffer
(YSRWJ-7/8 only).
Hard stop in the end position
Stop element overloaded
Reduce impact velocity or
check the layout of the stop
element.
Shock absorber faulty
Replace shock absorber.
Malfunction during position
sensing
Incorrect position of proximity
switches
Correct position of proximity
switches.
Incorrect proximity switch type
used
Only use proximity switches
type SME/SMT-8-...-B.
Proximity switch defective
Replace proximity switch.
Ferritic parts in the vicinity of
the proximity switch
Use parts made from non-mag-
netic materials.
Tab. 8: Fault clearance
9
Dismantling and disposal
CAUTION
The product contains pressurised hydraulic fluid that can escape in an uncon-
trolled manner if the housing is damaged.
The hydraulic fluid can injure people's eyes and skin and damage the environ-
ment.
• Have the product disposed of by a qualified waste disposal company.
• Do not destroy the product in order to drain the hydraulic fluid.