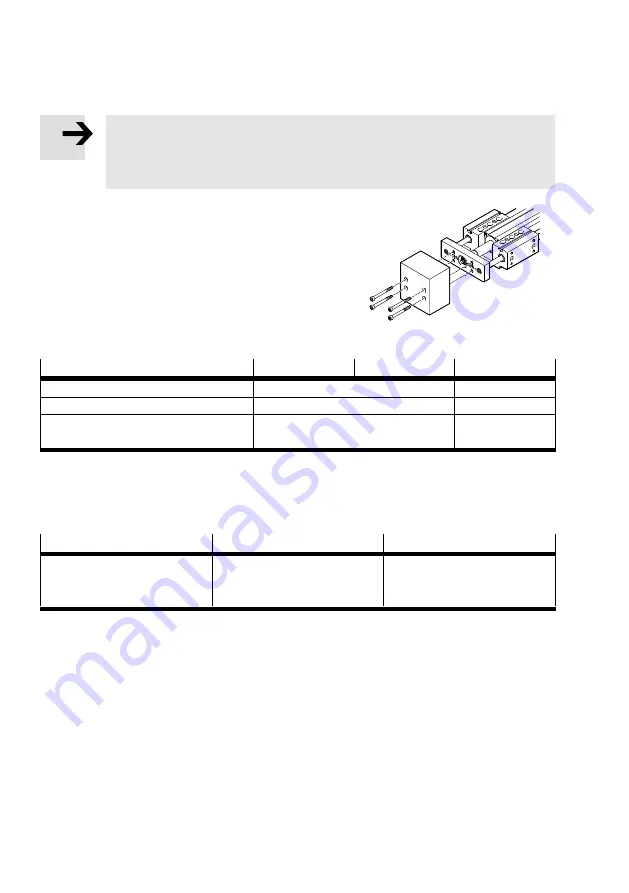
EPCO-...-KF
6
Festo – EPCO-...-KF – 1704a English
Installation of the payload
Note
If pins strike against the yoke plate, the mechanical connection can be destroyed
Push a metal plate between the yoke plate and the housing as a counterholder.
Then press the required pins into the yoke plate.
Place the centre of gravity of the payload as close as pos
sible to the centre of the yoke plate.
Attach the payload to the yoke plate in the retracted end
position.
The piston/guide rods bend, depending on the payload
(
è
Appendix, Characteristic curves).
Fig. 3
Size
16
25
40
Thread
M4 / M6
M5 / M6
Max. tightening torque
[Nm]
2.5 / 6
4 / 6
Centring holes
[mm]
5H7 /
7H8 /
9H8
7H8 /
8H7 /
9H8
Tab. 2
5
Fault clearance
Malfunction
Possible cause
Remedy
Running noises or
vibrations
Guide unit incorrectly mounted
(tension)
Align guide unit and electric
cylinder again (
è
Mounting
instructions)
Tab. 3