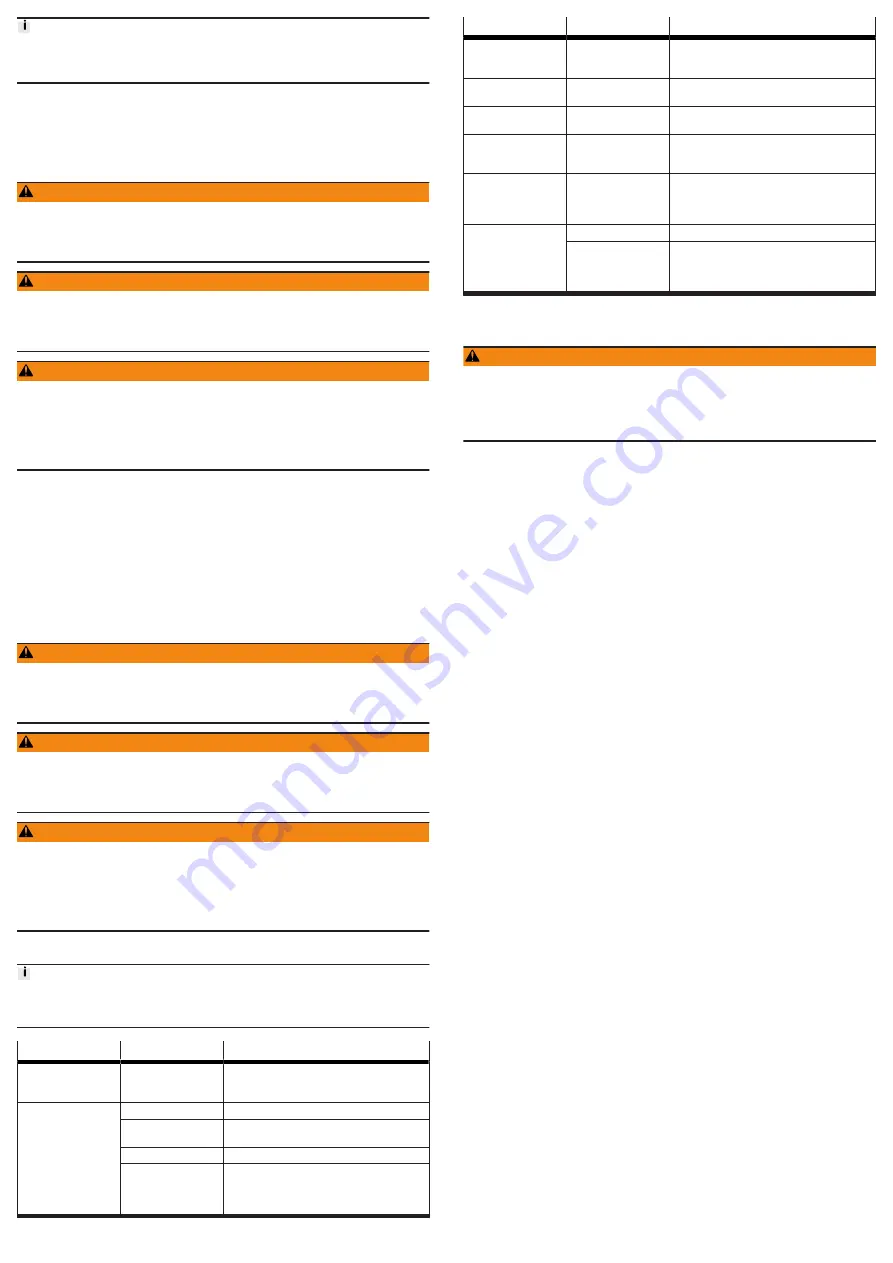
Axial and radial forces on the motor shaft.
Excessive axial and radial forces on the motor shaft can damage the motor.
• Comply with maximum permissible shaft loads
•
Check the function and holding torque of the holding brake at regular inter-
vals.
If the holding torque is reduced, close the holding brake briefly at low speed,
e.g. 3 s at 100 rpm.
10
Maintenance
WARNING
Risk of injury due to electric shock.
• Switch off power supply prior to assembly and installation work; ensure that it
is off and secure it against being switched back on.
Cancelling the enable signal is not sufficient.
WARNING
Risk of injury due to unexpected movement of components.
• Bring moving parts of the connected mechanical system into a secure position
(e.g. for vertical installation, move the slide into the lower end position).
• Only then should you disconnect the motor from the mechanical system.
WARNING
Danger of burns from hot housing surfaces.
Metallic housing parts can reach high temperatures during operation.
Contact with metal housing parts can cause burn injuries.
• Do not touch metallic housing parts.
• After the power supply is switched off, let the device cool down to room
temperature.
10.1
Replace the rotary shaft seal
For variants with rotary shaft seal EMMT-AS-...-...R-...:
•
Rotary shaft seal EASS must be replaced after 5,000 operating hours at the
latest
è
Instructions for rotary shaft seal,
10.2
Cleaning
Before cleaning, the product must be cooled down to below 40°C.
Clean the outside of the product with a soft cloth as required. Cleaning agents
include all non-abrasive media.
11
Malfunctions
WARNING
Risk of injury due to electric shock.
• Switch off power supply prior to assembly and installation work; ensure that it
is off and secure it against being switched back on.
Cancelling the enable signal is not sufficient.
WARNING
Risk of injury due to unexpected movement of components.
• Bring moving parts of the connected mechanical system into a secure position
(e.g. for vertical installation, move the slide into the lower end position).
• Only then should you disconnect the motor from the mechanical system.
WARNING
Danger of burns from hot housing surfaces.
Metallic housing parts can reach high temperatures during operation.
Contact with metal housing parts can cause burn injuries.
• Do not touch metallic housing parts.
• After the power supply is switched off, let the device cool down to room
temperature.
11.1
Fault clearance
Servo motor and absolute encoder
• Motor must not be opened.
• Repairs may only be carried out by the Festo repair service.
Malfunction
Possible cause
Remedy
Loud rotation noises of
the motor shaft.
Coupling distance too
short.
Observe permissible coupling distances
è
Instruction manual for motor mounting kit,
Motor shaft does not
turn.
Excessive load.
Reduce load.
Servo drive has not yet
been enabled.
Check signals.
Holding brake closed.
Release holding brake.
Min. operating voltage
for opening the
holding brake is not
reached.
–
Comply with permissible cable length and
cable cross section
–
Contact local Festo Service.
Malfunction
Possible cause
Remedy
Torque of the motor
shaft is not transmitted
to the drive system.
Coupling slips.
Check the mounting of the shaft-hub connection
è
Instruction manual for the motor mounting
Motor shaft vibrates.
Current controller set-
tings.
Optimise controller data, e.g. velocity, accelera-
tion, ...
Motor shaft rotates in
the wrong direction.
Wiring fault.
Check and correct wiring.
Holding torque of the
holding brake is not
reached.
Insufficient condi-
tioning of the brake
disc.
Briefly close the holding brake several times at
low speed, e.g. 3 s at 100 rpm.
Holding torque of the
holding brake not
effective.
Holding brake fault,
e.g. excessive axial
force on the motor
shaft.
–
–
Observe max. permissible axial force,
e.g. mount the coupling so it is free of ten-
sion.
Encoder signals not
transmitted.
Wiring fault.
Check and correct wiring.
Encoder fault,
e.g. excessive axial
force on the motor
shaft.
–
–
Observe max. permissible axial force,
e.g. mount the coupling so it is free of ten-
sion.
Tab. 6: Overview of fault clearance
12
Demounting
WARNING
Risk of injury due to falling product
If the product is lifted incorrectly, it may fall and cut, crush or separate body parts.
• Lift the product only with suitable load-bearing equipment.
• Product weight ≥25 kg: use only lifting eye bolts as lifting aids.
• Do not use the electrical connection and the motor shaft as a lifting aid.
1. Disconnect electrical installations.
2. Remove motor.
3. Observe transport information