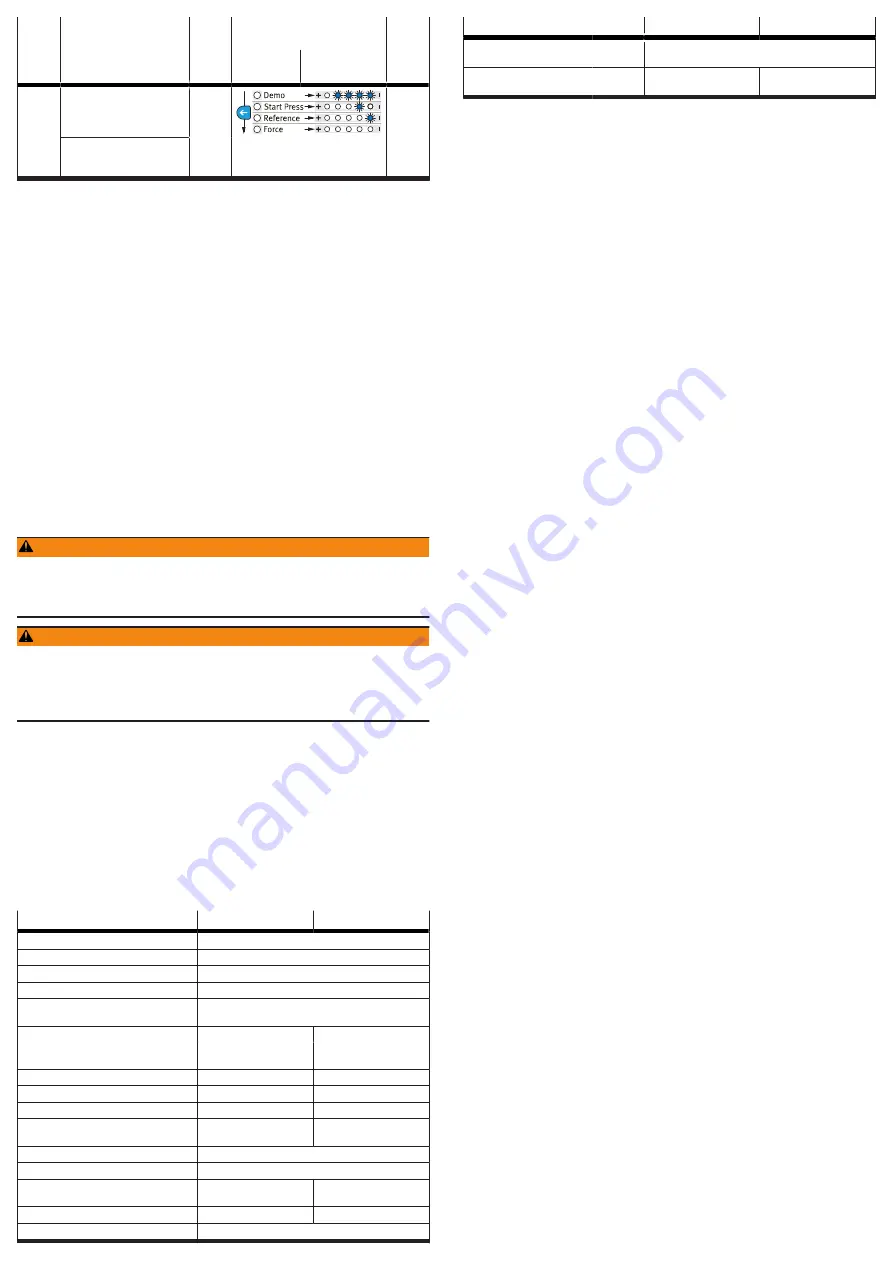
Error
code
Description
LED
LED displays
Event
code
hex
(dec)
C/Q
Menu
Parameter
(IO-
Link)
0x012F
(303)
IO-Link connection inter-
rupted
IO-Link connection inter-
rupted
z
Remedy
–
Check power supply
–
Check IO-Link master
1) Additional information
è
Instruction manual for integrated drive EMCS-ST
2) This error can only be acknowledged by a restart.
Tab. 7: "Information, warnings and errors" diagnostic messages
10.1
Repair
The product can be repaired or maintained.
–
Spare parts and accessories
–
Replace with an identical product
11
Replacement
Replace drive system
1. Save the application parameters to the IO-Link master
è
"Integrated drive
EMCS" instruction manual
2. Dismantle the defective drive system
3. Mount the new drive system
4. Connect the drive system
5. Commission the drive system
6. Update the firmware
è
"Integrated drive EMCS" instruction
manual
7. Check the current status of the application data
è
"Integrated drive EMCS"
instruction manual
Replace drive or integrated drive EMCS
è
"Integrated drive EMCS" instruction
12
Disassembly
WARNING
Unexpected movement of components.
Injury due to impacts or crushing.
• Before working on the product, switch off the control and secure it to prevent it
from being switched back on accidentally.
WARNING
Risk of Injury due to Unexpected Movement of Components
For vertical or slanted mounting position: when power is off, moving parts can
travel or fall uncontrolled into the lower end position.
• Bring moving parts of the product into a safe end position or secure them
against falling.
Disassemble drive system
1. Allow the product to cool down to room temperature.
2. Disconnect electrical installations.
3. Remove the mounted attachment component.
4. Remove the attached accessories.
5. Remove the mounting attachments.
6. Observe transport information
Remove drive or integrated drive EMCS
è
"Integrated drive EMCS" instruction
13
Technical data
Additional information
Size
45
60
Mounting position
horizontal
Ambient temperature
[°C]
0 … +50
Storage temperature
[°C]
–20 … +60
Degree of protection
IP40
CE marking
è
Declaration of Conformity
in accordance with EU EMC Directive
in accordance with EU RoHS Directive
Max. payload
–
horizontal mounting posi-
tion
[kg]
2.5
4.0
Max. velocity
1)
[mm/s]
1200
2)
1300
3)
Velocity "Speed Press"
[mm/s]
24
26
Max. feed force
4)5)
[N]
75
65
Max. force on external stops
during referencing
6)
[N]
84
142
Acceleration/deceleration
[m/s
2
]
6
Duty cycle
[%]
100 (+30 … +50 °C: – 2% per kelvin)
Distance between stop and
end position
7)8)
[mm]
3
2
Repetition accuracy
[mm]
±0.1
±0.1
Nominal voltage
[V DC]
24
Size
45
60
Logic current consumption
(logic, pin 1)
[mA]
DIO operation: 100 ... 300
IO-Link operation: 100 ... 150
Load current consumption
(power, pin 1)
[A]
5.3
5.3
1) Maximum value for Speed In/Speed Out at level 10
2) Can only be achieved from a stroke of 300 mm.
3) Can only be achieved from a stroke of 500 mm.
4) Maximum value for Force at level 10
5) Force is controlled and evaluated by closed-loop control of the motor current. Depending on the mecha-
nism of the drive, a linear force can be determined from the level of current measured. The target is set as
a percentage of the rated motor current and may deviate from the actual force on the axis. At the lower
force levels the frictional force of the drive system may be greater than the set feed force and result in the
drive system coming to a standstill.
6) The force acts on the stop for
£
100 ms
7) Distance (MechIn – LimIn or MechOut – LimOut)
8) The specified value can deviate due to the elasticity of the toothed belt.
Tab. 8: Technical data ELGS-TB