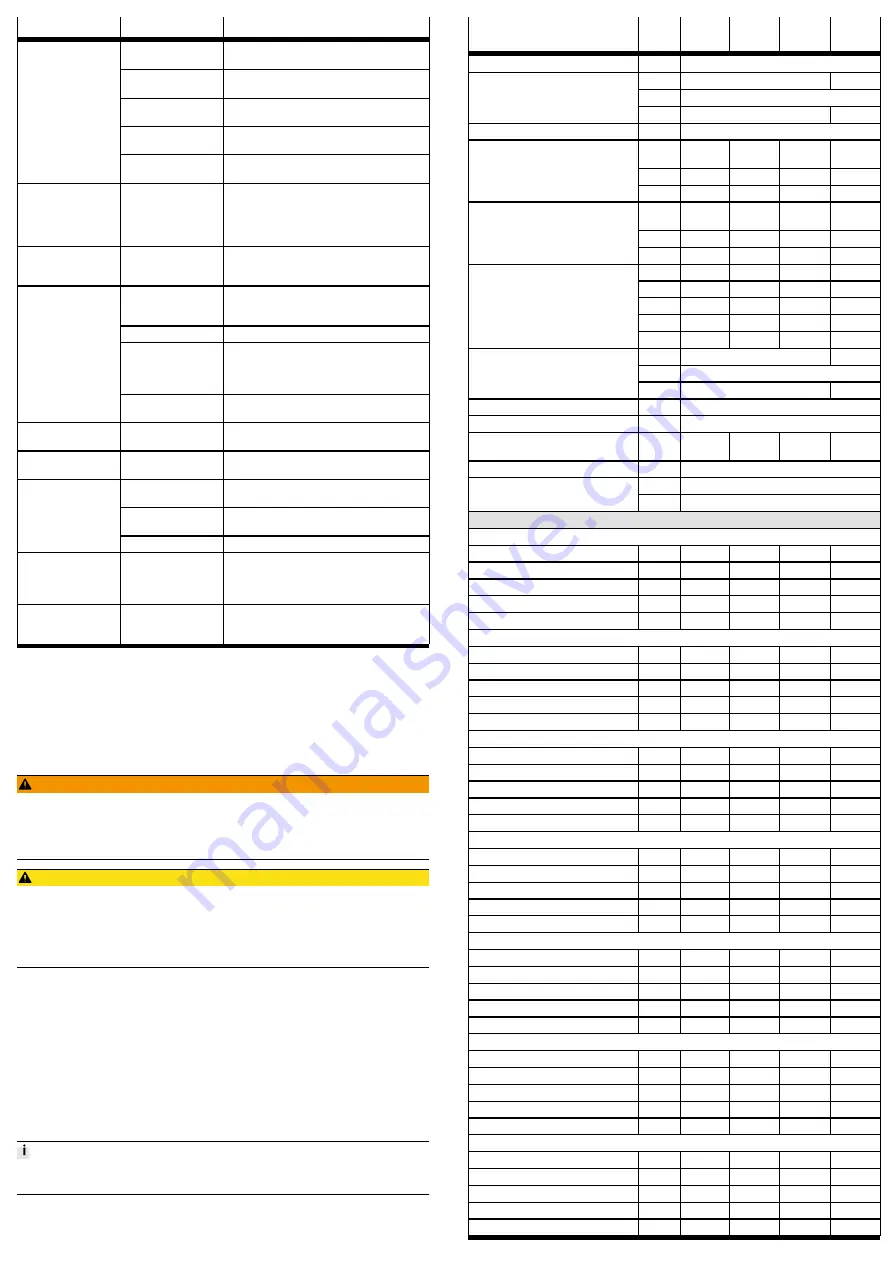
Malfunction
Possible cause
Remedy
Current controller set
tings.
Optimise controller data (e.g. velocity, accelera
tion, ...).
Resonance oscillation
of the axis.
Change the travel velocity.
Wear on bearing or
guide.
–
Contact local Festo Service.
–
Replace axis
è
Toothed belt wear.
–
Contact local Festo Service.
–
Replace axis
è
Loud running noises,
vibrations or rough
running of the axis.
Insufficient lubrication
of guide.
Lubricate the guide
è
Vibrations on the slide.
Operation at the reson
ant frequency of the
axis.
–
Change the travel velocity.
–
Change the acceleration.
–
Increase axis stiffness (e.g. shorter support
distances).
–
Change the payload geometry.
Long oscillations of the
profile.
Resonant frequency of
profile and payload too
low.
–
Increase axis stiffness (e.g. shorter support
distances).
–
Change the payload geometry.
Coupling slips.
Check the mounting of the shafthub connection
è
Instruction manual for the motor mounting
kit, www.festo.com/sp.
Loads too high.
Reduce forces and torques. Consider dynamics.
Screws too long for fix
ing the attachment
component (e.g. pay
load).
Observe the screwin depth
è
Tab. 5 Information on attachment
Slide does not move.
Toothed belt ripped.
–
Contact local Festo Service.
–
Replace axis
è
Overruns the end posi
tion.
Sensor does not
switch.
Check sensor, installation and parameterisation.
Idling torque too high.
Wear in the drive train.
–
Contact local Festo Service.
–
Replace axis
è
Toothed belt preten
sioning too low.
–
Contact local Festo Service.
–
Replace axis
è
Current controller set
tings.
Optimise controller data (e.g. velocity, accelera
tion, ...).
Toothed belt skips.
Loads too high.
Reduce travel speed.
Wave formation on the
cover strip or alumini
um abrasion on the
axis.
Wear on belt reversals.
–
Retension cover strip.
–
Replace belt reversal and cover strip
è
Oil leak between pro
file housing and cover.
Fully suctioned oil
sensor.
ELGATBRF:
–
Replace oil sensor.
–
Contact local Festo Service.
Tab. 10 Overview of fault clearance
11.2
Repair
–
Observe the information for dismantling
è
–
Send axis to Festo repair service.
–
Information about spare parts and accessories
è
12
Disassembly
WARNING!
Unexpected movement of components.
Injury due to impacts or crushing.
•
Before working on the product, switch off the control and secure it to prevent
it from being switched back on accidentally.
CAUTION!
For vertical or slanted mounting position: when power is off, moving parts can
travel or fall uncontrolled into the lower end position.
Injury due to impacts or crushing.
•
Bring moving parts of the product into a safe end position or secure them
against falling.
1. Remove electrical installations with accessories.
2. Remove motor and mounting kit.
3. Remove the mounting attachments.
4. Observe transport information
è
13
Disposal
Dispose of the product and packaging at the end of its useful life through environ
mentally friendly recycling in accordance with applicable regulations.
14
Technical data
14.1
Technical data, mechanical
To size the axis, use the PositionDrives engineering software
è
Size
70
80
120
150
Design
...
Electromechanical axis with toothed belt
G
Plainbearing guide
–
KF
Recirculating ball bearing guide
Guide
RF
Roller bearing guide
–
Mounting position
...
any
G
RF
350
800
1300
–
KF
350
800
1300
2000
Max. feed force Fx
[N]
F1
260
600
1000
–
G
RF
5
15.9
34.1
–
KF
5
15.9
34.1
73.9
Max. driving torque
[Nm]
F1
3.7
11.9
26.2
–
G
0.5
1
3
–
KF
0.6
1
2.8
4
KFF1
0.8
1.5
4.5
–
RF
0.7
1.4
3
–
Max. idling driving torque at
v = 0.2 m/s and with cover
strip
[Nm]
RFF1
1
1.9
5.7
–
G
5
–
KF
5
Max. speed
[m/s]
RF
10
–
Max. acceleration
[m/s
2
]
...
50
Repetition accuracy
[mm]
...
±
0.08
Feed constant
[mm/re
v]
...
90
125
165
232
Ambient temperature
[°C]
...
10 … +60
IP40
Degree of protection
P0
IP00
Max. permissible forces and torques on the slide
ELGATB...G
Fy
[N]
...
80
200
380
–
Fz
[N]
...
400
800
1600
–
Mx
[Nm]
...
5
10
20
–
My
[Nm]
...
30
60
120
–
Mz
[Nm]
...
10
20
40
–
ELGATB...KF, ELGATB...KFF1
Fy
[N]
...
1500
2500
5500
11000
Fz
[N]
...
1850
3050
6890
11000
Mx
[N]
...
16
36
104
167
My
[N]
...
132
228
680
1150
Mz
[N]
...
132
228
680
1150
ELGATB...RF, ELGATB...RFS
Fy
[N]
...
500
800
2000
–
Fz
[N]
...
500
800
2000
–
Mx
[Nm]
...
11
30
100
–
My
[Nm]
...
20
90
320
–
Mz
[Nm]
...
20
90
320
–
ELGATB...RFL
Fy
[N]
...
500
800
2000
–
Fz
[N]
...
500
800
2000
–
Mx
[Nm]
...
11
30
100
–
My
[Nm]
...
40
180
640
–
Mz
[Nm]
...
40
180
640
–
ELGATB...RFXS
Fy
[N]
...
–
800
2000
–
Fz
[N]
...
–
800
2000
–
Mx
[Nm]
...
–
30
100
–
My
[Nm]
...
–
40
150
–
Mz
[Nm]
...
–
40
150
–
ELGATB...RFF1, ELGATB...RFSF1
Fy
[N]
...
400
640
1600
–
Fz
[N]
...
400
640
1600
–
Mx
[Nm]
...
8.8
24
80
–
My
[Nm]
...
16
72
256
–
Mz
[Nm]
...
16
72
256
–
ELGATB...RFF1L
Fy
[N]
...
400
640
1600
–
Fz
[N]
...
400
640
1600
–
Mx
[Nm]
...
8.8
24
80
–
My
[Nm]
...
32
144
512
–
Mz
[Nm]
...
32
144
512
–