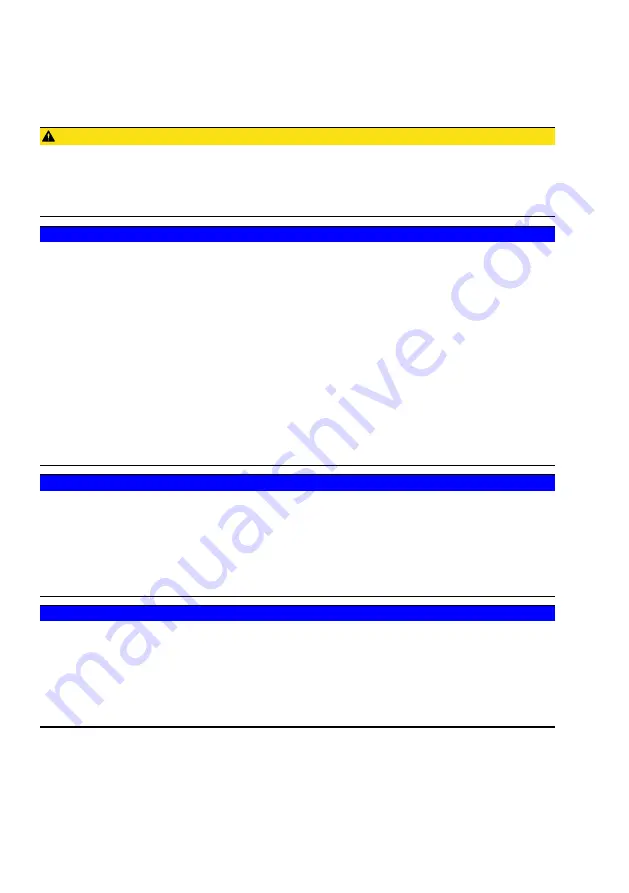
8
Commissioning
CAUTION!
Risk of injury due to unexpected movement of components.
•
Protect the positioning range from unwanted intervention.
•
Keep foreign objects out of the positioning range.
•
Perform commissioning at low speed.
NOTICE!
Incorrect set values for the braking ramp in STOP statuses
(e.g. EMERGENCY OFF, Quick Stop) result in an overloading of the spindle axis and can destroy it or
drastically reduce its service life.
•
Check the settings for all braking ramps in the controller or the higher-order control system (decel-
eration values and jerk).
•
Adjust delay values (braking delay, delay times) in such a way that the maximum driving torque,
acceleration or maximum feed force is not exceeded. In the process, take the following into con-
sideration:
–
Travel speed
–
Moving mass
–
Mounting position
•
When designing the spindle axis, use the Festo engineering software "PositioningDrives"
è
NOTICE!
Block-shaped acceleration profiles (without jerk limitation) cause high peaks in the drive force that
can lead to an overloading of the drive. Due to overshooting effects, positions outside of the permiss-
ible range may also occur. A jerk-limited acceleration specification reduces vibrations in the entire sys-
tem and has a positive effect on stress in the mechanical system.
•
Check the controller settings and adapt if necessary (e.g. jerk limitation, smoothing of the acceler-
ation profile).
NOTICE!
Axes of the same design may demonstrate different running noises depending on the respective com-
ponent. The following factors may also influence this issue:
•
Parameterisation
•
Operating mode
•
Type of mounting
•
Installation situation (e.g. rigidity of the foundation, vibration behaviour, resonance frequencies)
Commissioning
12
Festo — EGSC-BS-KF — 2018-11c