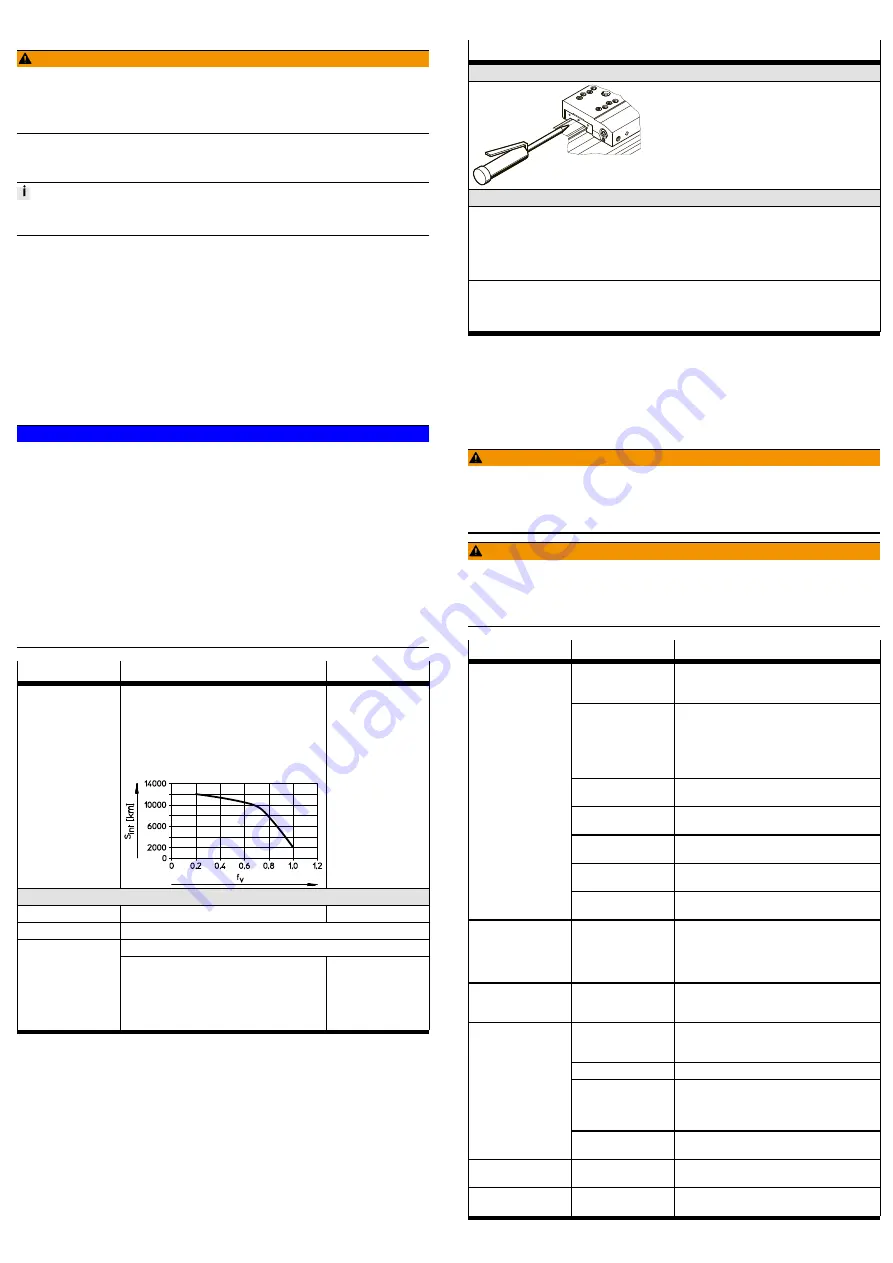
10
Maintenance
10.1
Safety
WARNING!
Unexpected movement of components.
Injury due to impacts or crushing.
•
Before working on the product, switch off the control and secure it to prevent
it from being switched back on accidentally.
10.2
Check axis components
Check toothed belt wear
The pretension of the toothed belt is designed for the entire service life.
Tensioning of the toothed belt is not permitted.
1. EGCTB, EGCHD...TB:
–
Initial check: after 5000 km.
–
Periodic check: every 1000 km.
2. If there is visible wear on the toothed belt: Send the axis to Festo or contact
è
www.festo.comFesto Service.
10.3
Cleaning
1. Clean the product with a soft cloth. Do not use aggressive cleaning agents.
2. If necessary, clean the guide rail with a soft lintfree cloth without detergent.
Then apply a thin layer of lubricant to the guide rail.
10.4
Lubrication
Lubrication interval and accessories
NOTICE!
The lubrication interval S
int
is dependent on the load acting on the product.
Load factors include e. g.:
•
Dusty and dirty environment
•
Nominal stroke
>
2000 mm or
<
300 mm
•
Speed
>
2 m/s
•
Ambient temperature
>
+40 °C
•
Service age of product
>
3 years
•
Travel profile matches triangular operation (frequent acceleration and brak
ing)
If one of these factors applies:
•
Halve lubrication interval S
int
.
If several factors apply at the same time:
•
Divide service interval S
int
by four.
Lubrication
Recirculating ball bearing guide KF
Guide rail
Lubrication interval
–
Calculate
è
14.1 Technical data, mechanicalthe com
parative loading factor f
v
using the formula
for combined loads.
–
Lubrication intervals S
int
as a function of the
load comparison factor f
v
can be taken from
the diagram.
If required, e. g. if the
grease layer is too low.
Accessories
è
Lubrication point
Lubrication hole
Surface
Lubricant
Roller bearing grease LUBKC1
Onehanded pressure grease gun with pinpoint nozzle LUB1, 647958
Grease gun
–
Lubrication adapter, axial output,
LUB1TRI, 647959
–
Lubrication adapter, radial output,
LUB1TRL, 647960
–
Lubrication adapter LUB1KU, 744166
(EGCHD125TB only)
–
Tab. 8 Overview of lubrication intervals and accessories
Lubricate guide
Recirculating ball bearing guide KF
Lubrication hole, on both sides (EGC…GK/GV only)
Grease quantity per lubricating opening:
EGCTB (size)
–
50: 0.2 g
–
70: 0.3 g
–
80: 0.6 g
–
120: 1.2 g
–
185: 3.6 g
EGCHD...TB (size)
–
125: 1 g
–
160: 1.1 g
–
220: 2.7 g
Tab. 9 Overview of lubrication
1. Inject lubricant into all lubrication holes.
2. During the lubrication process, travel the entire distance in order to distribute
the lubricant evenly inside the machine.
11
Malfunctions
11.1
Fault clearance
WARNING!
Unexpected movement of components.
Injury due to impacts or crushing.
•
Before working on the product, switch off the control and secure it to prevent
it from being switched back on accidentally.
WARNING!
Risk of injury due to unexpected movement of components.
•
Protect the positioning range from unwanted intervention.
•
Keep foreign objects out of the positioning range.
•
Perform commissioning with low dynamic response.
Malfunction
Possible cause
Remedy
Coupling distance too
short.
Observe permissible coupling spacings
è
Instruction manual for motor mounting kit,
Tensions
–
Install axis without tension. Note the flat
ness of the contact surface
è
–
Change the layout of the attachment com
ponent (e.g. payload).
–
Align axes parallel to one another.
Current controller set
tings.
Optimise controller data (e.g. velocity, accelera
tion, ...).
Resonance oscillation
of the axis.
Change the travel velocity.
Wear on bearing or
guide.
–
Contact local Festo Service.
–
Replace axis
è
Toothed belt wear.
–
Contact local Festo Service.
–
Replace axis
è
Loud running noises,
vibrations or rough
running of the axis.
Insufficient lubrication
of guide.
Lubricate the guide
è
Vibrations on the slide.
Operation at the reson
ant frequency of the
axis.
–
Change the travel velocity.
–
Change the acceleration.
–
Increase axis stiffness (e.g. shorter support
distances).
–
Change the useful load geometry.
Long oscillations of the
profile.
Resonant frequency of
profile and payload too
low.
–
Increase axis stiffness (e.g. shorter sup
port distances).
–
Change the useful load geometry.
Coupling slips.
Check the mounting of the shafthub connection
è
Instruction manual for the motor mounting
kit, www.festo.com/sp.
Loads too high.
Reduce forces and torques. Consider dynamics.
Screws too long for fix
ing the attachment
component (e.g . pay
load).
Observe the screwin depth
è
Tab. 5 Information on attachment
Slide does not move.
Toothed belt ripped.
–
Contact local Festo Service.
–
Replace axis
è
Overruns the end posi
tion.
Sensor does not
switch.
Check sensor, installation and parameterisation.
Idling torque too high.
Wear in the drive train.
–
Contact local Festo Service.
–
Replace axis
è