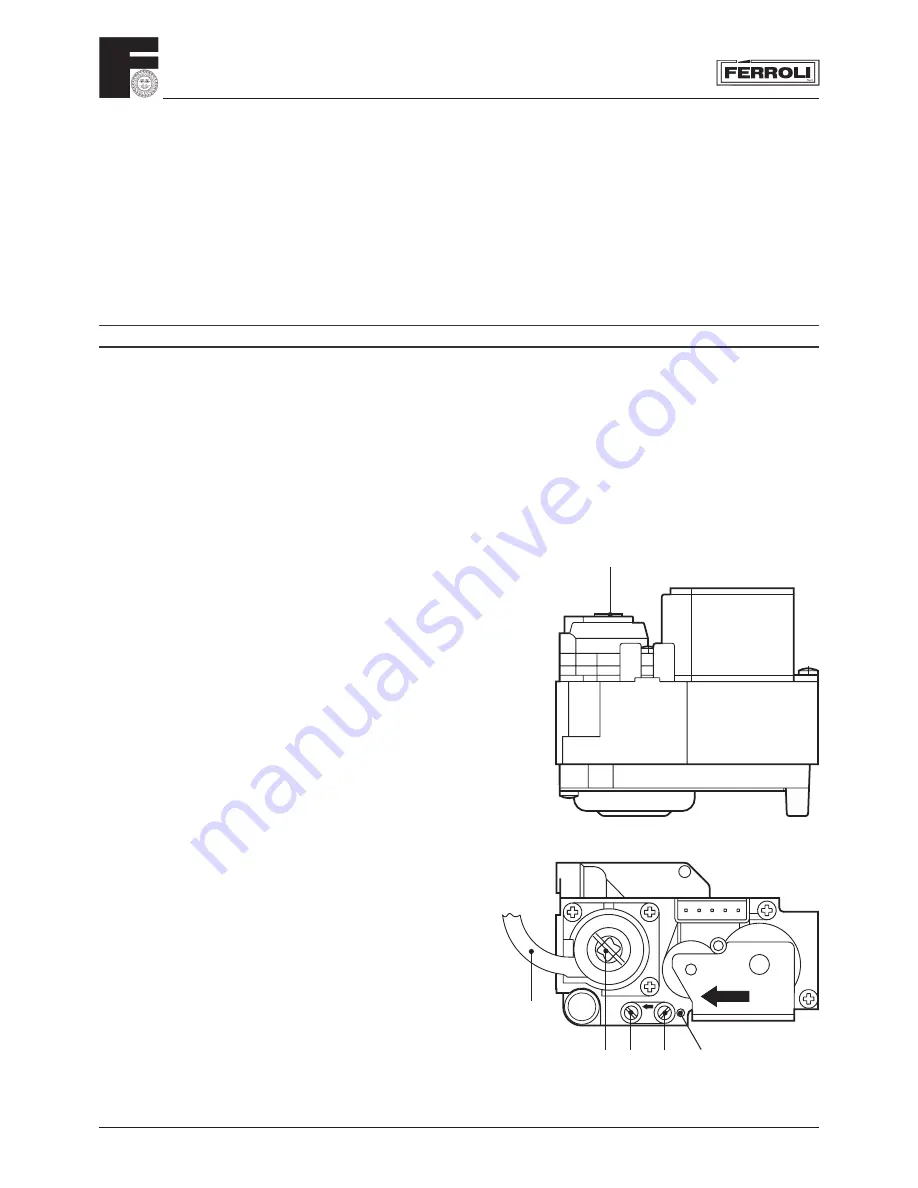
FERROLI F30
26
5. ADJUSTMENT AND GAS CONVERSION
5.01 Adjusting the pressure and fl ow rate to the main burner
This boiler operates on the fl ame modulation principle. It has two fi xed pressure values, minimum and maximum,
which must be as shown in the table (pages 5), whichever type of gas is used.
Note -
Because correct minimum and maximum pressures are critical to the efficient operation
of the boiler it is ESSENTIAL that the following adjustments are carried out by COMPETENT
personnel ONLY.
5.02 Adjusting minimum and maximum pressure Honeywell V K4105G gas valve
- Connect suitable pressure gauge to burner test point “
B
”
downstream of the gas valve.
- Disconnect the pressure compensation tube «
F
».
- Remove the protective cap «
C
».
- Adjust potentiometre
P3
(on the main board) at minimum
(clockwise).
- Operate boiler for central heating
- Adjust minimum pressure by rotating screw «
D
» clockwise
to reduce pressure and anticlockwise to increase pres-
sure.
- If it is not possible to achieve the right pressure adjust
minimum pressure by potentiometer
P5
- Adjust potentiometre
P3
at maximum (anticlockwise)
- Adjust max pressure by rotating screw «
E
», clockwise to
increase pressure and anticlockwise to reduce pressure.
- Reconnect the pressure compensation tube «
F
».
- Replace protective cap «
C
».
Maximum + Minimum possible gas pressures are now
set. Range Rating the central heating is not necessary
(see paragraph 5.04).
IN
OUT
C
F
E
B
A
D
Key
A = Gas inlet test point
B = Gas outlet test point (burner pressure)
C = Protection cap
D = Min. pressure adjusting screw
E = Max. pressure adjusting screw
F = Balancing tube
hot water tap is turned on and off.
• Check that the domestic hot water flow and T correspond to the table. Do not rely on empirical
measurements. Temperature should be measured using thermometers as near as possible to the boiler,
in mind the heat loss from the pipes.
• Check that the gas valve modulates correctly both during the central heating phase and the domestic
hot water production phase.
• To determine combustion effi ciency and the composition of the fl ue gases (refer to 6.04)
• If any of the above are not correct refer to Technical Data (page 5). Adjustment (page 23) and Fault
Finding (page 32).
Fig. 23
Содержание Domina 102
Страница 47: ......