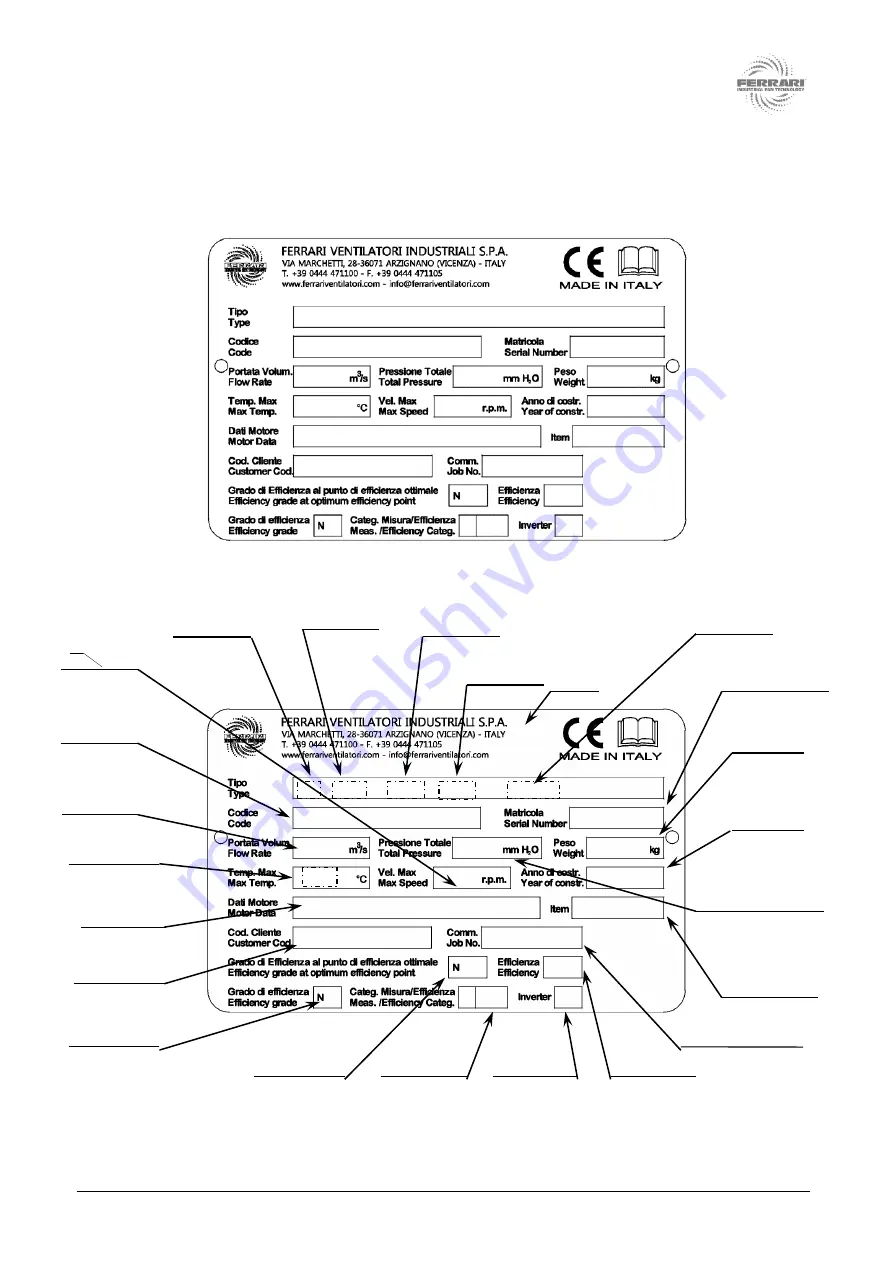
MVA 02 rev 5 - December 2017
13 of 120
2.3
Fan identification
The identification plate is the only means of fan identification recognized by the manufacturer. It must not be
modified, and must not be removed or damaged. Fig. 2-3 shows the plate fitted to the fan.
Fig. 2-3 Identification plate of fan described by this manual
Fig. 2-4 Key to reading fan identification plate
Fan construction
year
2013
1310460
GR. 132 7,50 kW 4 POLI 50 Hz
EF0906I04AA02
EF 906/I 4A/A 132 A19
FVI
customer
code (optional)
FVI
customer order
number (optional)
FVI
customer item
number (optional)
Type and
characteristics of
motor installed
Fan flow capacity
(optional)
Total fan pressure
(optional)
Serial number
Fan identification
code
Fan series
Fan size
Version/use/flow
Blade fitting
angle
60
Maximum temperature of
fluid moved in °C
Manual
Installed motor
size
Fan weight
Efficiency grade*
*In conformity with EU Regulation No. 327/2011
Efficiency grade at
optimum energy
efficiency point*
Efficiency
measurement
category*
Powered with
inverter*
Efficiency*
Maximum
rotational speed