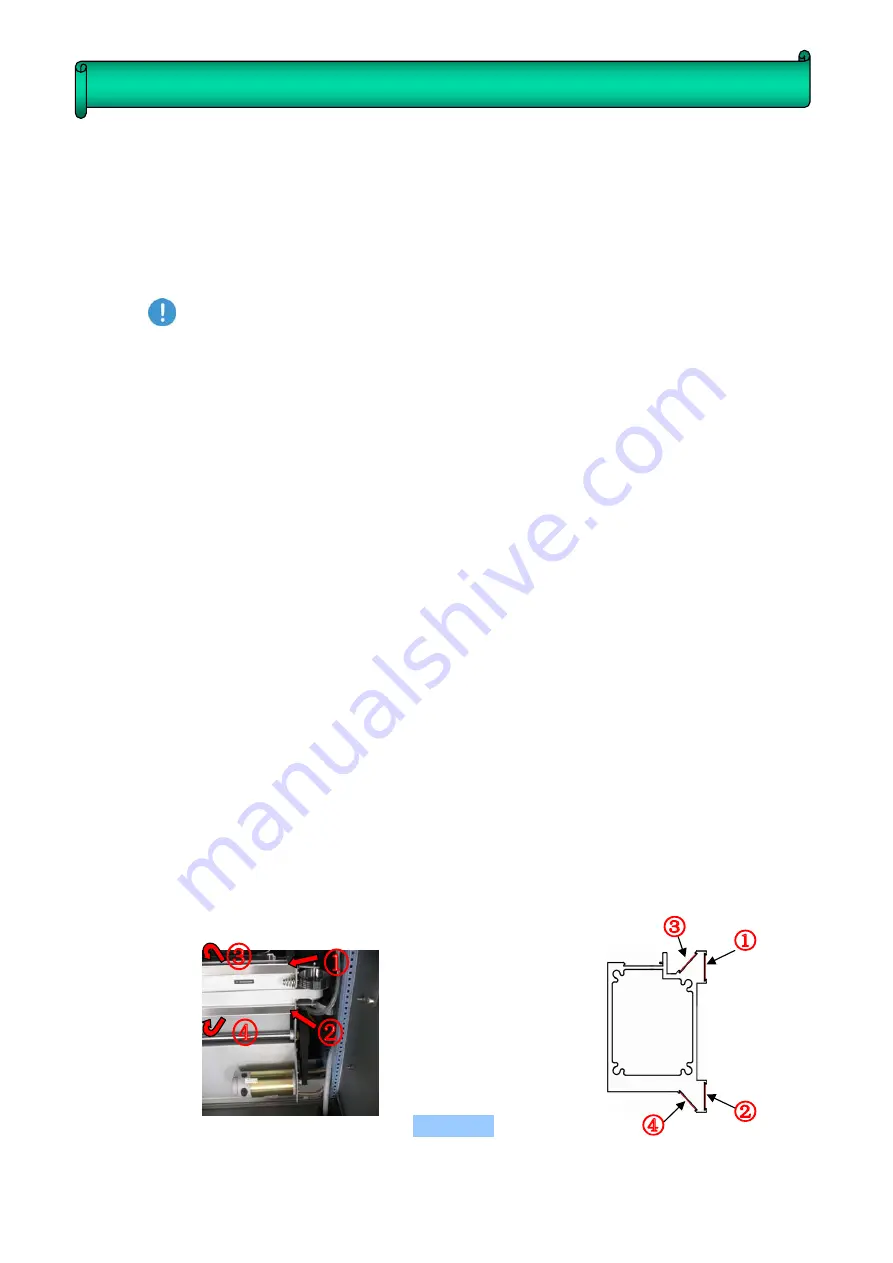
37
5.1 Normal Cleaning
:
Positive Pressure Cleaning
Press the cleaning button, and then use sponge stick or soft fabric to wipe the surface
of the printhead.
Warning: Using the material other than sponge stick or soft fabric to wipe the
printhead may risk damaging nozzles.
5.2 Cleaning procedures for nozzle clogging
Ⅰ
.
Disconnect
the
tube
connector
for
the
tube
from
the
Subtank
to
the
printhead.
Wait
until
the
ink
finishes
dropping
almost,
and
then,
connect
the
tube
to
the
solvent
tube.
Press
both
of
the
flush
buttons
to
clean
the
printhead
with
solvent.
Stop
until
the
solvent
becomes
clear
nearly.
Ⅱ
.
Use
tube
cover
to
seal
the
ink
incoming
tube
for
the
printhead.
Use
fresh
wrap
to
cover
the
nozzle
surface.
Leave
it
for
12
hours.
Ⅲ
.
Take
the
fresh
wrap
off.
Disconnect
the
tube
cover
and
wait
until
the
solvent
is
removed
almost.
Connect
the
tube
to
the
subtank,
and
fill
the
printhead
with
ink.
The
condition
of
printhead
should
be
improved
after
performing
the
above
cleaning
procedures.
5.3
Carriage Bearing and Steel Rail Maintenance
Due
to
the
carriage
slides
on
four
steel
plates
and
eight
bearing,
clean
and
lubricate
four
steel
plates
with
grease
everyday.
Ⅰ
.
Wipe
a
thin
layer
of
grease
on
steel
plates
to
maintain
cleanliness
and
grease
everyday
before
and
after
usage.
Ⅱ
.
Be
aware
of
the
smoothness
of
the
carriage
bearing
Figure
5
‐
1
Chapter
5
Maintenance
Guide